Nordfish-Foodmark is committed to leveraging Industry 4.0 manufacturing technology to optimize its operations. To give its existing brownfield plants the necessary connectivity, the company evaluated an innovative solution from B&R that allows it to monitor and optimize the performance of its jar-packing line.
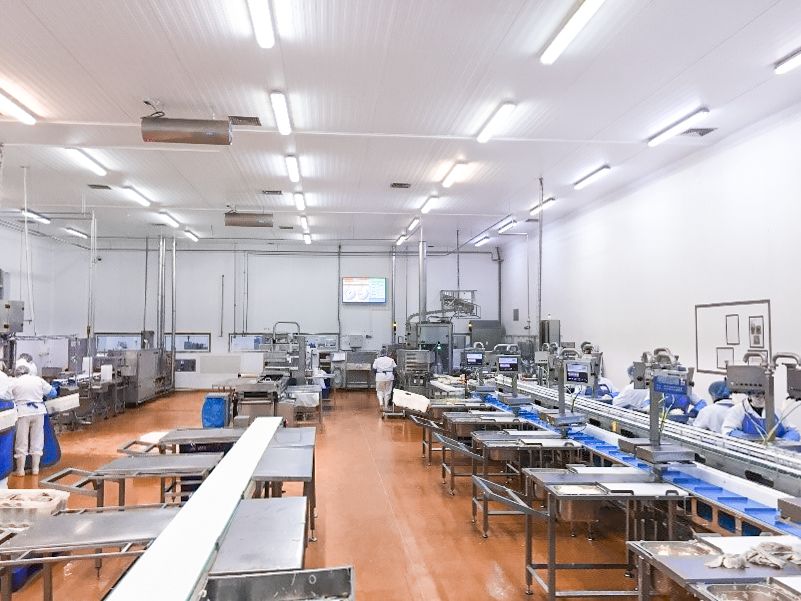
At its plant in Charzyno, Poland, Nordfish-Foodmark processes and packages herring, sprat and mackerel. Adam Schwan, head of operational excellence, realized that a lack of insight into the line's availabilitiy was standing in the way of further optimization. In order to take well-informed action to improve system availability and production quality, operators would need comprehensive information about the performance and health of their equipment.
Well informed is half the battle
When he saw B&R's innovative Orange Box solution, Schwan knew he had found what he was looking for. "The Orange Box lets us tap into energy and process data from older, digitally isolated machines," he explains, noting that they can get that data without having to make any changes to existing hardware or software. "The HMI shows a clear overview of performance metrics, making it easy for us to identify the most effective ways to boost overall equipment efficiency."
Nordfish-Foodmark is able to use its Orange Box to calculate real-time KPIs, generate and archive statistical reports, log information about production stoppages and audit changes to settings and variables. They can also easily share production reports with higher-level systems.

How it works
Nordfish-Foodmark began with a test implementation of the Orange Box on its jar-packing line in Charzyno. The 20 machines and other standalone units that make up the line were grouped into four technology zones. Each zone was equipped with a collection of buttons that allows operators to log the reasons for any downtime or interruptions – both scheduled and unscheduled.
The Orange Box acquires data from the line and transmits it to the appropriate operators. Communication takes place via OPC UA, and data is read using distributed I/O islands and a legacy third-party controller.
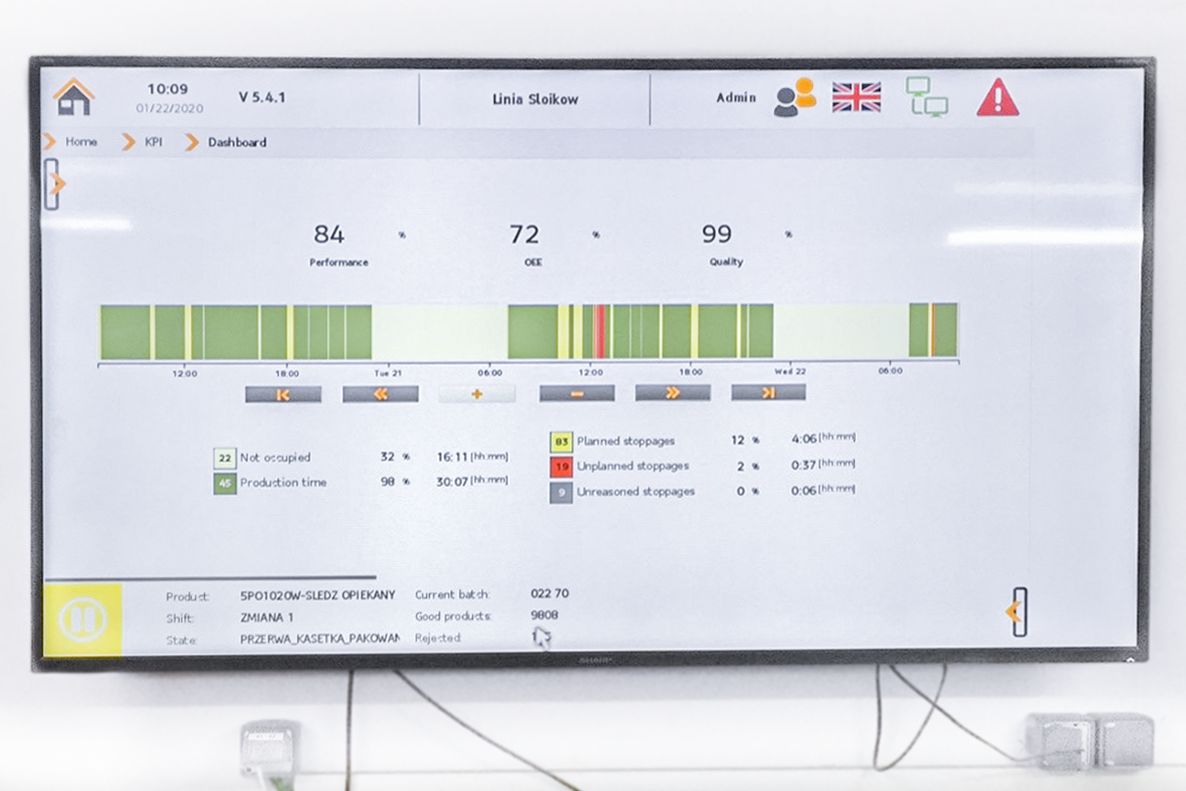
Enjoying the rewards
With B&R's tool, operators can now react in real time when they see a dip in performance, and they know exactly what to do to resolve quality issues. Schwan is pleased to have succeeded in getting his operators the data they need. "When something happens on the line – an emergency stop, a conveyor jam, a tripped fuse – they know about it in less than a second and can take immediate action."
The Orange Box also allows them to implement predictive maintenance. Continuous monitoring of the condition of key equipment gives insight that allows maintenance personnel to restore operation faster or prevent stoppages altogether. Schwan also appreciates the quick live analysis of planned and unplanned stoppages.
With the Orange Box, the plant employees responsible for performance reporting no longer spend all their time obtaining the information they need, and can instead focus their efforts on what is most important – developing mechanisms that increase line efficiency.

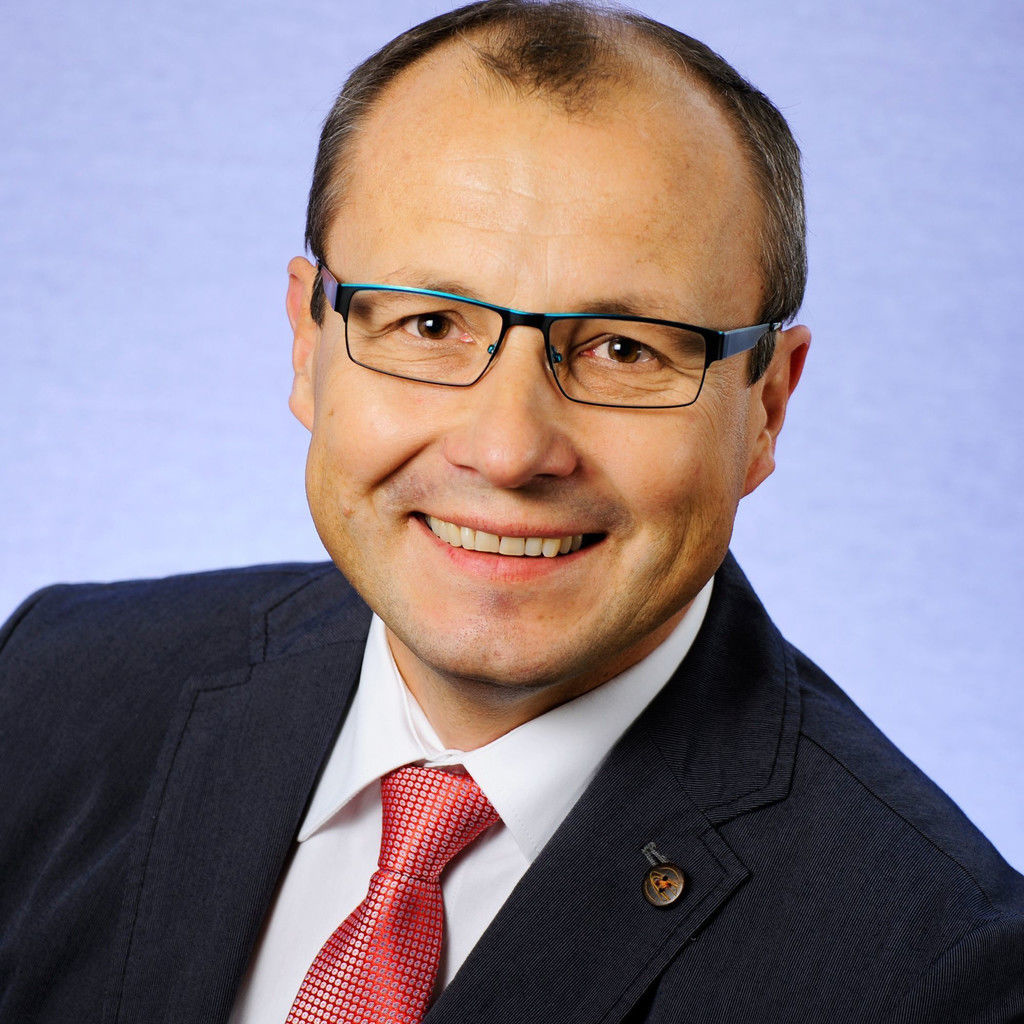
Adam Schwan, Head of Operational Excellence
"When something happens on the line – an emergency stop, a conveyor jam, a tripped fuse – they know about it in less than a second and can take immediate action."

What's next?
Having evaluated the Orange Box on its jar-packing line, Nordfish-Foodmark is preparing to roll out its modernization project on the other five automatic lines. Planning is also underway for a master Orange Box, which will act as a master system for data archiving, forwarding to ERP systems, generating reports and managing Orange Box versions.
In conclusion, Schwan is eager to point out: "We completed this project using our own technical team and during the busy season – and that says quite a lot about how well-designed and easy this solution is to work with."
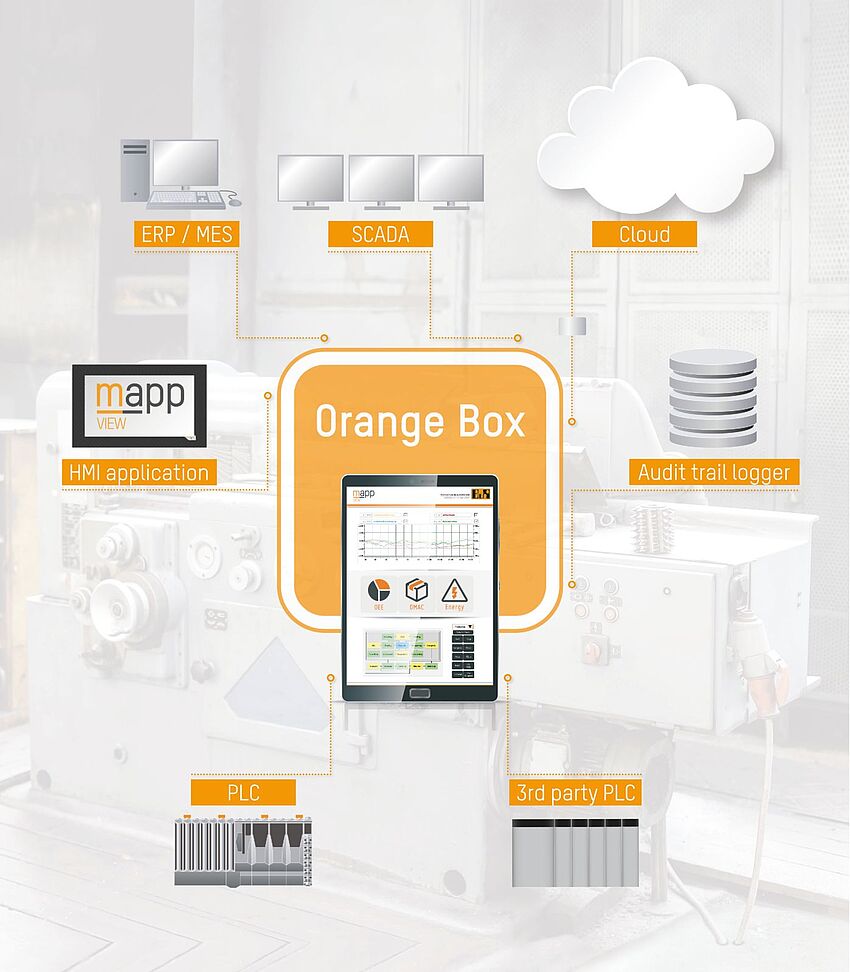
Orange Box is an Industrial IoT solution for brownfield installations. The solution consists of selected B&R hardware and preinstalled software. Machine data can be collected via hardwired I/Os or selected fieldbus connections and used to calculate OEE ratings and other KPIs in real time. This makes it possible to promptly implement well-targeted optimizations and corrective measures. The HMI solution is based on future-proof HTML5.