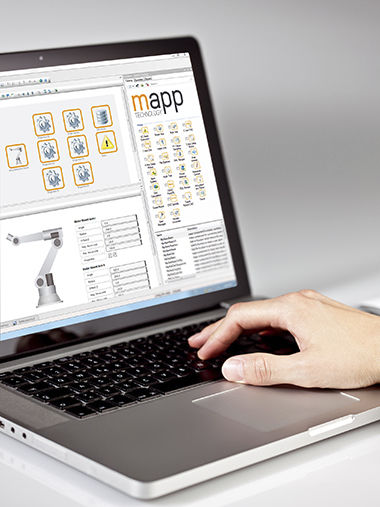
Develop 3 times faster
Plastics processing machinery needs to be more flexible and more efficient than ever. With these requirements increasingly being solved in software form, software engineering is consuming a rapidly growing share of the development budget and schedule. mapp Technology makes software development much easier and faster:
- Development completed an average of 3x faster
- Intelligently linked components
- Configure basic functions instead of programming them
Components are available for individual steps performed by plastics machinery, including the injection process. mapp Technology allows OEMs to focus their time and resources on what matters most: Developing and optimizing machine-specific functions.
EUROMAP – The next step toward Industry 4.0
The unprecedented levels of machine-to-machine and plant-wide networking that distinguish IoT and I4.0 solutions can only be achieved with uniform communication standards. The plastics industry was quick to recognize and implement this requirement with the EUROMAP recommendations:
- EUROMAP 27 for extrusion line communication
- EUROMAP 63, 77 for the interface between MES and injection press
- EUROMAP 67 for the interface between robotics / handling unit and injection press
B&R has incorporated these interfaces directly into its products in the form of precoded blocks that offer OEMs ultimate convenience during development.
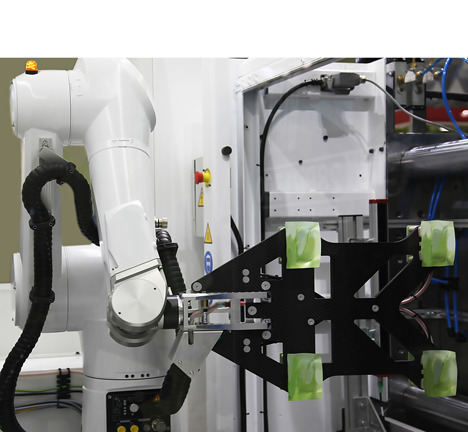
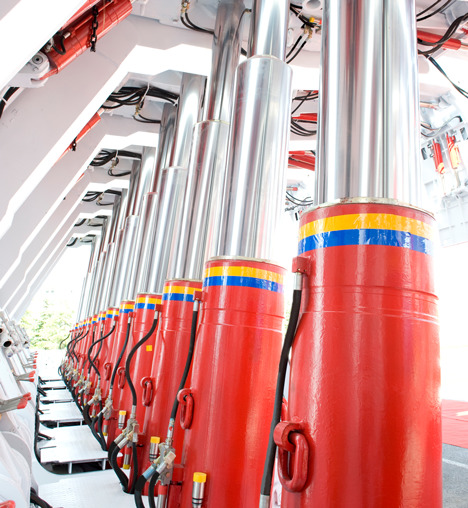
Optimal tuning for hydraulic controls
Servo hydraulics play an essential role in plastics processing machinery. Automatic tuning processes help get the most out of every system – for machines that are fast to set up and efficient to operate. The quality of the end product depends heavily on pressure and speed being regulated with extremely fast response times. B&R offers integrated functions for optimizing servo-hydraulic systems:
- Integrated control loop optimization
- Automatic valve identification
- Powerful diagnostics
Temperature control made easy
Precise temperature control is a hallmark of all types of plastics processing machinery – from injection and blow molding to extrusion and thermoforming. B&R offers a comprehensive array of ready-made function blocks for fully automated control loop tuning, multi-zone synchronization and efficient, robust closed-loop control. Users can also take advantage of B&R's sample applications to streamline development of their own applications.
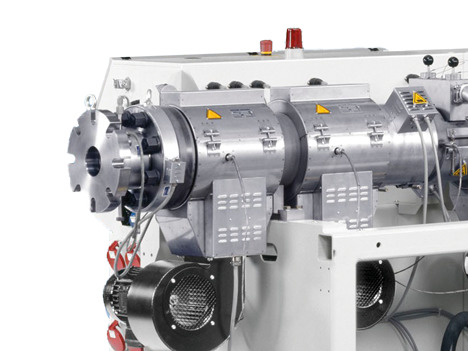
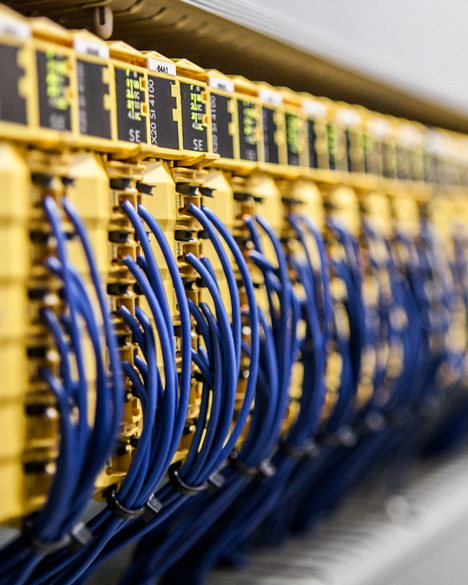
Higher productivity, more functions, easy safety
Integrated safety technology enables safe reactions that make plants more productive. Safety solutions with digital, analog and temperature measurement modules from B&R satisfy all of today's toughest requirements for safety technology, from general guidelines like EN ISO 13849 and IEC 61508 to C-type standards such as EN 201 and EN 1114. B&R safety is so efficient, it even pays off for small-scale applications with few I/O channels. Other benefits include:
- Minimal space requirements
- Improved diagnostics
- Easy scalability
- Cost-effective hardware
POWERLINK for maximum efficiency
The communication protocol also has a decisive impact on the performance of a machine. Direct connection of servo valves simplifies installation and ensures fast response times for optimal injection molding performance. Connecting handling robots directly to plastics machinery increases the efficiency of the entire system. Advantages of POWERLINK:
| ![]() |
Process and evaluate data efficiently
Modern production processes generate enormous volumes of data that can provide valuable feedback about equipment utilization, productivity and energy efficiency. With this data available in real time, the potential is there for continuously optimized operation. It takes intelligent systems, however, to process this flood of data and arrive at the right conclusions. B&R offers the necessary tools with its APROL Solutions:
- APROL PDA
Centralized data acquisition and analysis - APROL EnMon
Optimized energy consumption and costs - APROL ConMon
Early detection for maximum uptime
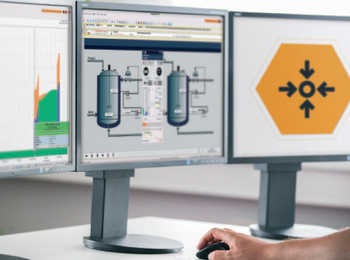