As part of their efforts to reduce CO2 emissions, car manufacturers are building vehicle bodies from lightweight materials such as aluminum and carbon composites, combined with high-strength and ultra-high-strength steel. To solve the challenging task of joining these different materials together, EJOT developed and patented the new EJOWELD process, implemented using B&R technology.
The spot welding process performed in car body construction is very demanding. The strength of the joint and the achievable cycle time are subject to the same demands as for welded joints. In addition, there are a whole range of technological conditions that must be precisely adhered to and documented for the different combinations of materials. On top of that, the robot-guided tool must be able to reach all the required locations on the body without any collisions.
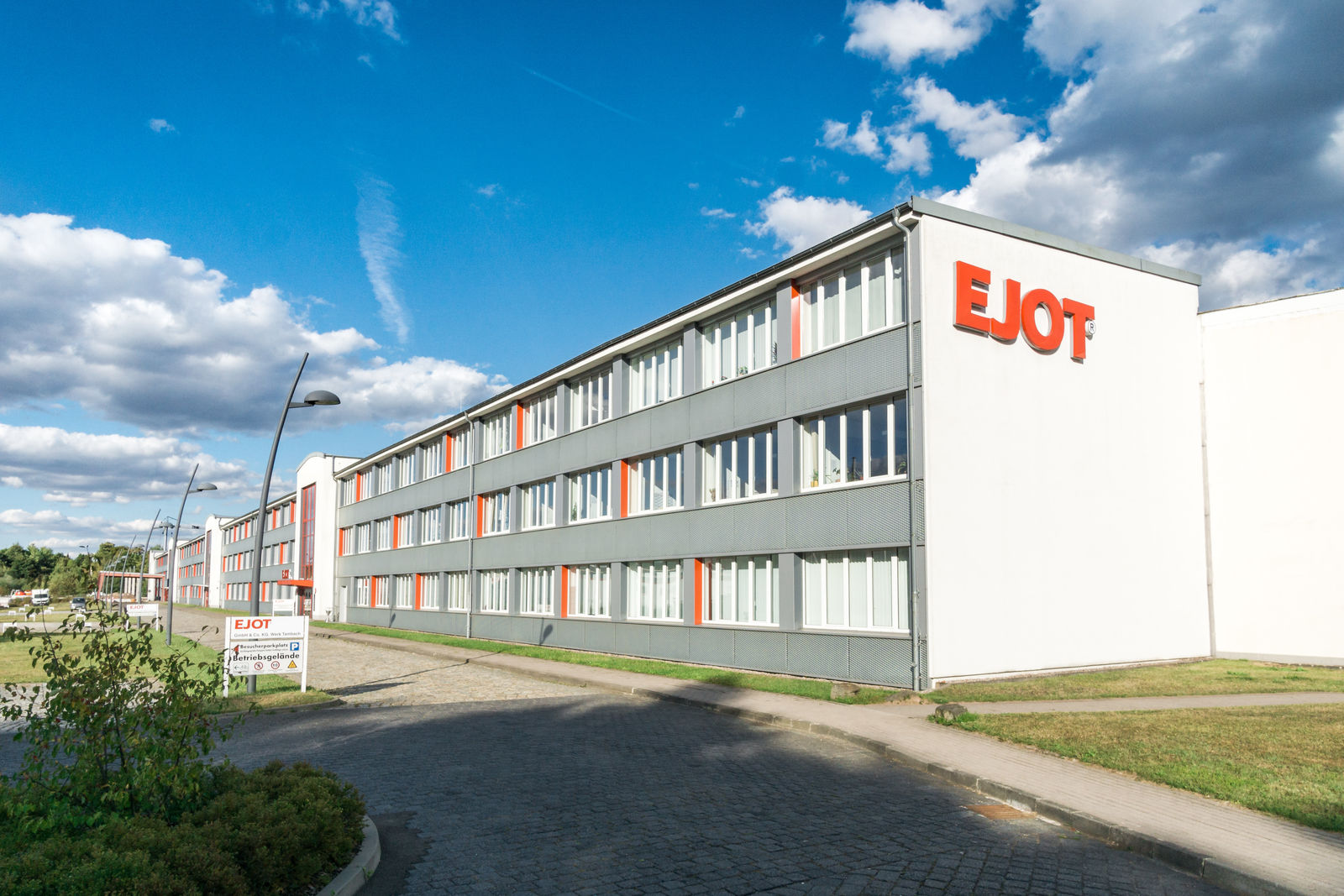
High-precision friction welding
At first glance, the friction welding process used in the EJOWELD solution appears to be relatively simple. A setting tool presses and rotates a connecting element through the softer outer material in a four-stage process, and the resulting friction heats it up to approximately 1,100°C, permanently joining it with the harder layer below. The devil is in the details, however. For starters, the whole process takes only between 0.7 and 1.8 seconds. "If you don't adhere to the process parameters very precisely," Schrodt explains, "the connection won't hold, and before long the layers will begin to separate." To monitor the process and store the results for quality assurance, up to 30,000 data points are logged during each welding process. "That's quite a demanding task for the control system," says Robert Heiland, who leads EJOWELD development. "B&R's Automation PC, ACOPOSmulti and POWERLINK technology do an outstanding job mastering the challenge."
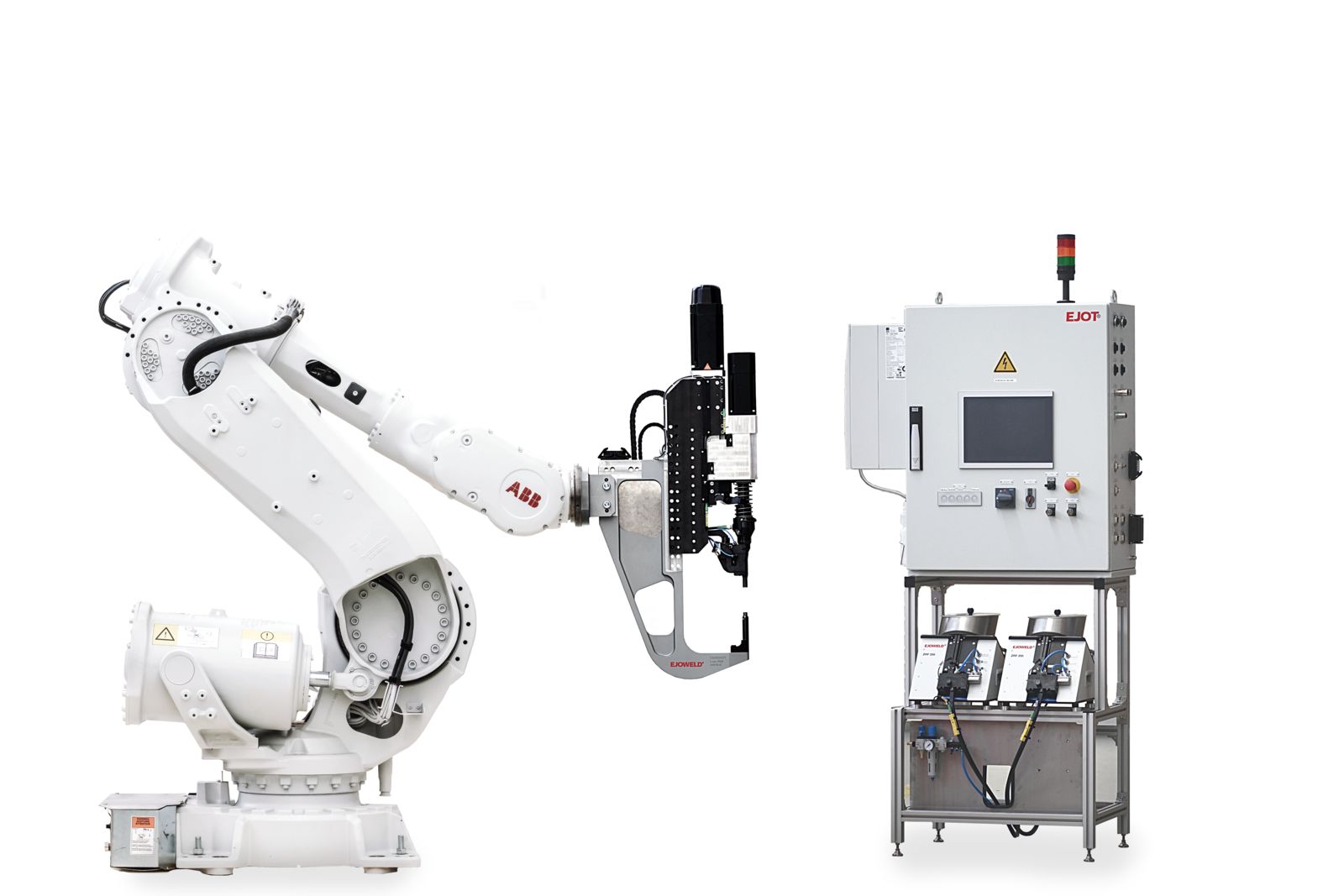
Equipped for global use
"In order to deploy the solution anywhere in the world, the power supply for the drive technology must be independent of the mains supply. This is important to ensure consistent processing conditions without having to install different components for each type of power grid." That's exactly why B&R designed the power supply modules of its ACOPOSmulti drive system to supply the DC bus with a constant 750 VDC over a wide range of mains voltages and frequencies. The reactive power is regulated to cos φ = 1, which is important for optimized mains power regeneration.
Drive precision ensures optimum quality
During the friction welding process, it is necessary to switch between different control processes in real time. "We have to be able to identify the moment when the friction element reaches the harder material with a precision of just a few microseconds in order to be able to switch to the corresponding control process," says Heiland. The servo drive reads the values of a separate axial force sensor and applies them highly dynamically as additional input parameters in the current control loop. Additional control signals are incorporated from peripheral devices and must be processed in a matter of microseconds.
These signals are read by B&R X67 I/O modules mounted on the setting tool in the immediate vicinity of the process, and transmitted directly to the drive and controller via POWERLINK.
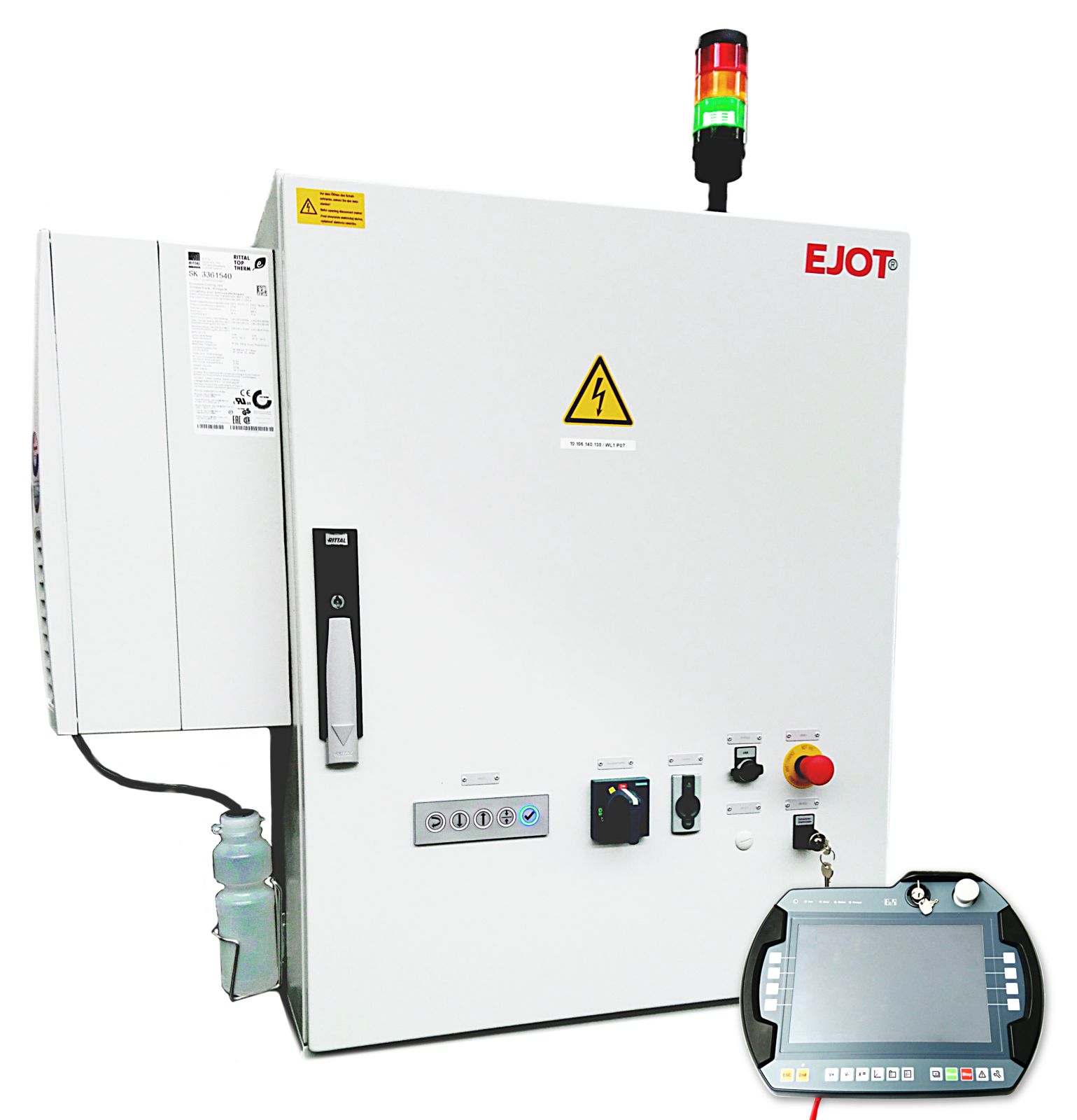
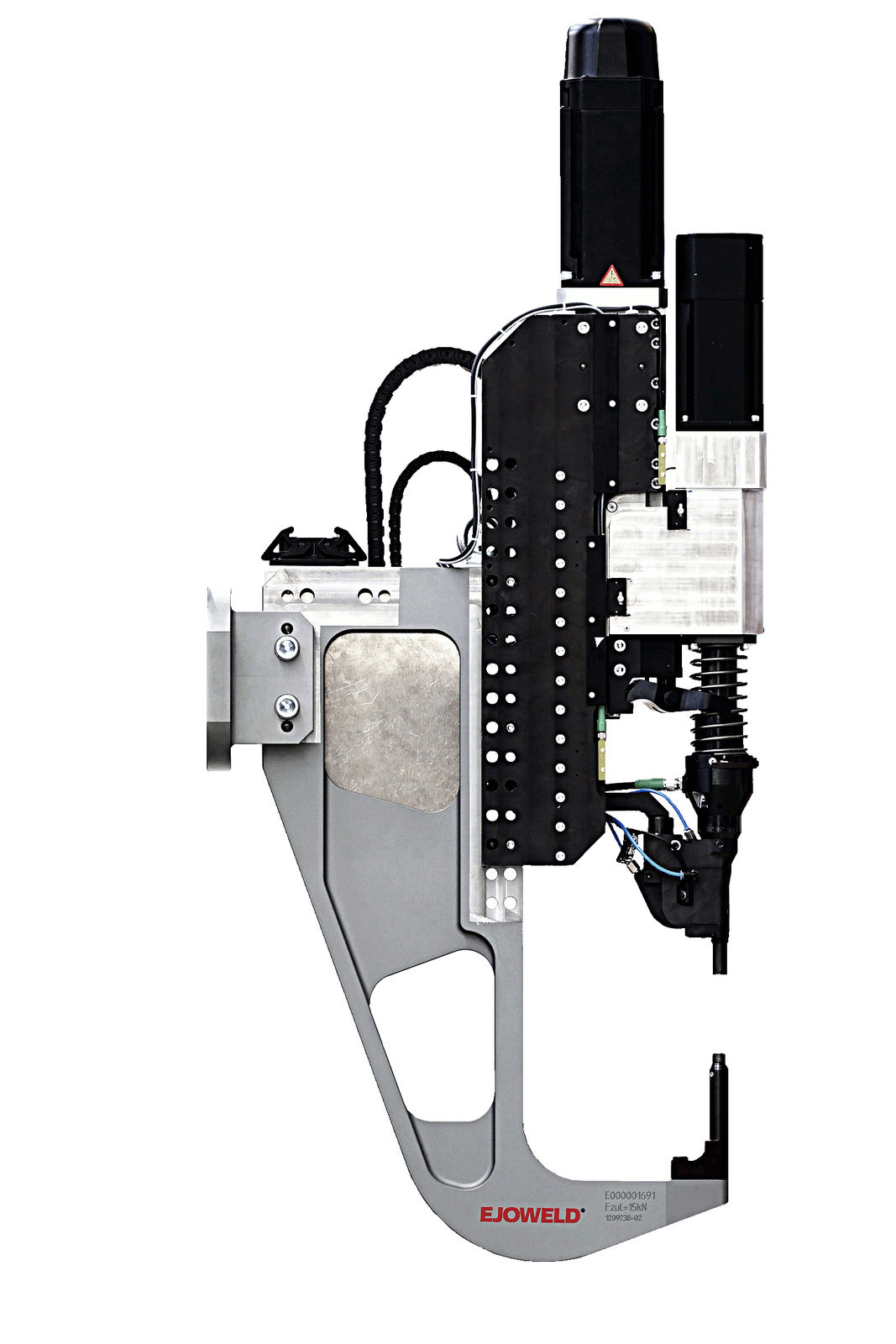
Modular, interoperable hardware ensures flexibility
The greater the differences in the materials being joined, the more flexible the automation system needs to be in order to adapt to the different requirements. "With B&R, we have a partner whose products enable us to implement these adaptations perfectly and without any compatibility problems," says Heiland. The different hardware and software interfaces required for integration with the robot and other production equipment are standard features of the B&R portfolio.
Thanks to B&R's integrated safety technology, the same level of adaptability is also possible for the safety solution. Last but not least, the complete interoperability of B&R's X20 PLC and Automation PC allows EJOT to scale the solution as needed without having to make adjustments in the software application. "We can easily upgrade to a powerful industrial PC for more advanced process control," says the sales manager, giving some insight into future development plans. Another goal is to further optimize the setting tool design with even more compact motors.
In so doing, EJOT is making an important contribution to the use of lightweight materials that make automobile manufacturing more environmentally friendly.
Robert Heiland EJOWELD Systems Engineer, EJOT "Developing a whole new system generation is a momentous decision. Choosing a partner with such a well thought-out concept and comprehensive service helped us turn our vision into reality and offer a solution that is well-equipped to handle whatever new requirements the future brings." |