Kay Trumpler and his company TMS are dedicated to the field of precision optics. Well established in the field of servicing and retrofitting optical manufacturing equipment, TMS recently began constructing its own CNC machines for milling, drilling and cutting optical glass. The automation for these new TMS machines – like all other automation technology installed by the company since its founding in 2008 – comes from B&R.
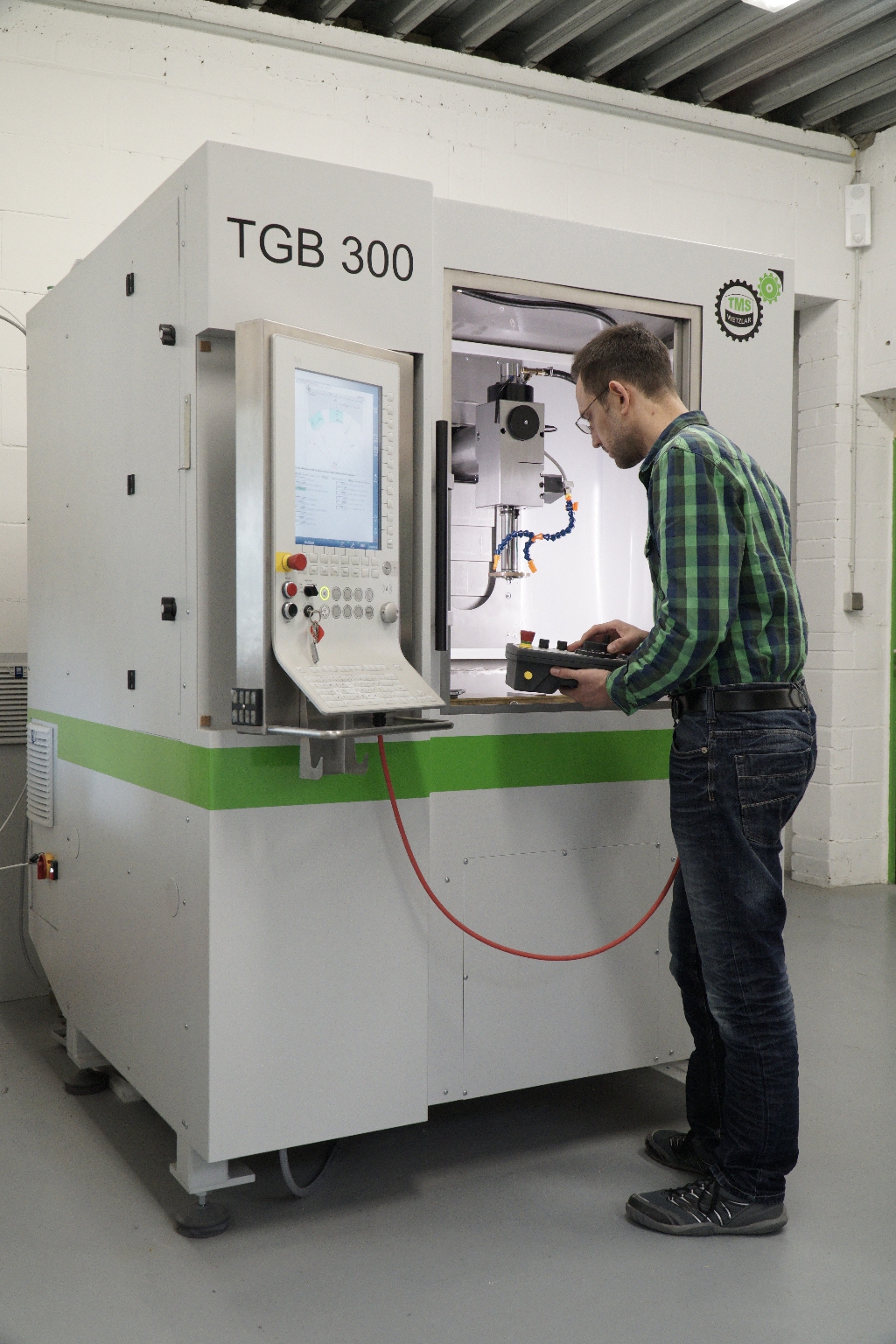

For Kay Trumpler, a trained machinist and industrial foreman with decades of experience in the optics industry, there are clear reasons for choosing a B&R automation solution for his machines, whether retrofit or new constructions. "Particularly in retrofitting jobs, we have to deal with all sorts of unique automation challenges. To cover such a broad spectrum, we need a highly integrated, extremely flexible automation solution. That's exactly what we get with B&R."
Since retrofitting is generally only a feasible option for relatively simple machinery, the complexity of the task is kept within reasonable limits. Constructing new machines is a whole different story. New machinery has complex automation architectures that integrate safety functions, CNC, motion control and sequential control. "The exceptional scalability and seamless integration of B&R's solutions have been pivotal in our smooth transition into product-based business," says Trumpler.
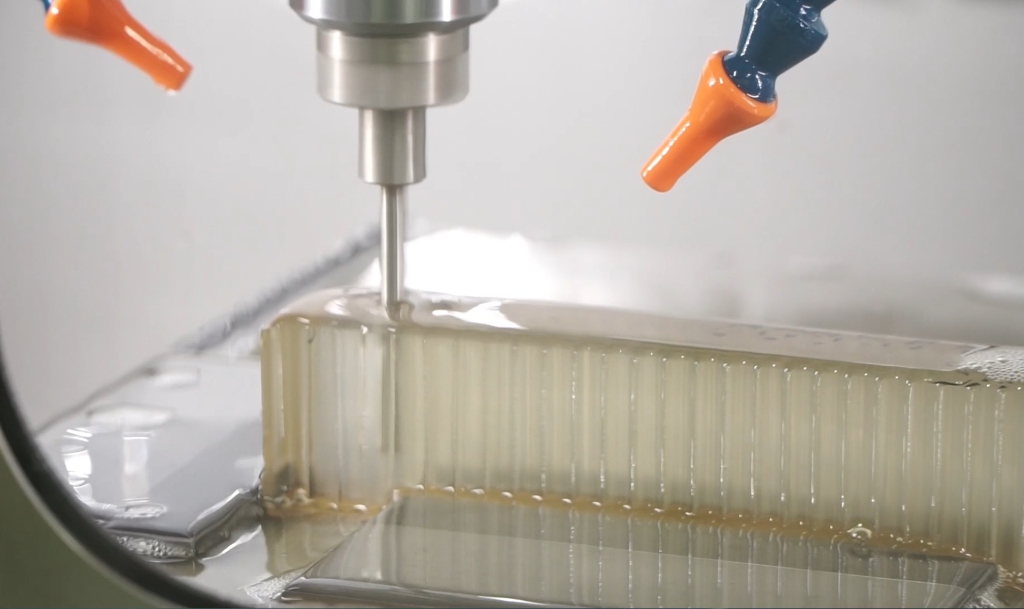
One engineering environment for the entire project
As a smaller company, TMS has to be especially careful about how it uses its personnel and resources. "That's where we really benefit from the universal engineering environment in Automation Studio," says Trumpler. With Automation Studio, TMS is able to handle everything from communication and HMI to CNC and machine control with a single software package, regardless of which hardware is used. "And we can do all this without constantly having to purchase new licenses and upgrades," adds Trumpler. "That and B&R's outstanding support make it easy for us to get up to speed on new topics, lower our expenses and complete projects more quickly."
With this support, TMS successfully transitioned into the new construction business with a low-cost centering machine – in under a year and with only five employees.
Positive feedback from the market inspired TMS to begin development of an entire product family based on a shared machine platform. The first products from this new family are the TGS 300 glass cutter and the TGB 300 glass processing machine.
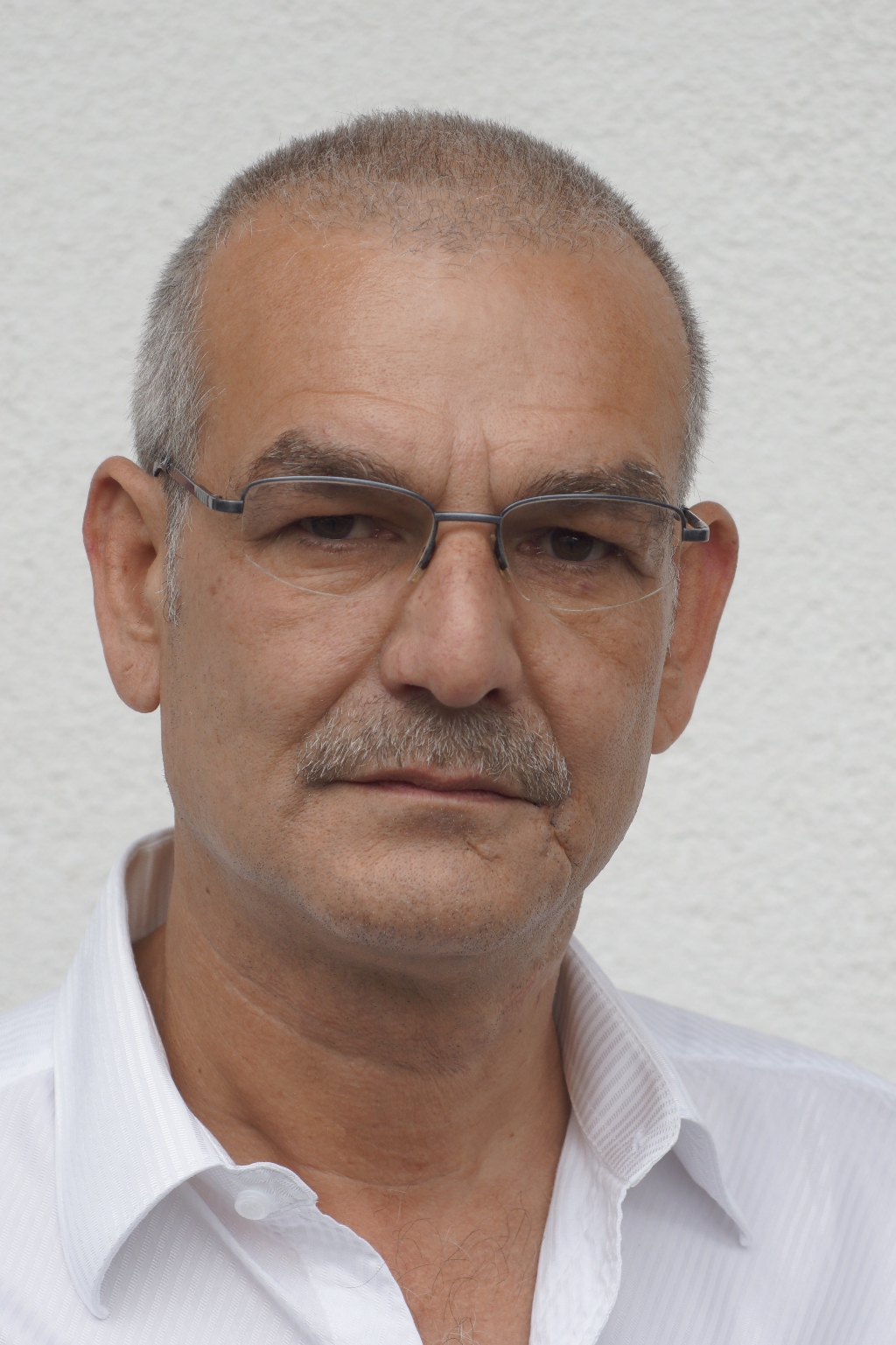
"The ability to unite CNC, PLC, motion and HMI on a single software platform is one of the most remarkable aspects of the B&R solution." Kay Trumpler, Owner, TMS e.K.
Universal glass milling machine
The TGB 300 allows optics producers to mill workpieces out of glass blocks measuring up to 300 millimeters in diameter for in-house production of prototypes and small batches. "This type of task used to require three separate machines," explains Trumpler. "Now all you need is one TGB 300." This is the first processing solution for optics production that offers all the functionality of a universal milling machine for metalworking, but is designed for the specific requirements of glass.
For example, TMS completely encapsulated the machining center and eliminated all guides and metal blinds to provide immunity for the machine against the abrasive glass-diamond residue created during processing.
The TGB 300 is equipped with up to five CNC axes (X, Y, Z, rotary table and indexing head) controlled by ACOPOSmulti servo drives. To keep the machine accessible during setup, the servo drives feature B&R's integrated SafeMOTION technology, which allows the axes to be operated safely at reduced speed. The machine's safety equipment, such as its E-stop buttons, are all integrated via safe I/O modules from the X20 system.
TMS retrofits optical manufacturing equipment for other manufacturers as well as building its own glass processing machinery. The small team of engineers is confronted with a broad spectrum of automation challenges ranging from basic controllers to complex, multi-axis CNC machines with safety functions. That's why TMS chose to work with Automation Studio, because it allows them to program every aspect of the software – from communication to CNC and HMI – in a single environment.
Real space savings with a virtual safety controller
The safety functions are controlled by a compact SafeLOGIC-X module. "The virtual controller supports all the same SafeMOTION functions as the more powerful safety controllers," explains Fabian Hölzel, who worked with Trumpler on the design and construction of the machine. He was the one responsible for programming all of the control and application software, including the CNC and HMI applications, in Automation Studio. "The software is absolutely modular and is identical for both machine types," explains Hölzel. "The only adaptation required is to change a few parameter settings." Users can also easily adapt the HMI application to their requirements so that even semi-skilled workers are able to operate the machine.
For its operator interface, TMS selected an operator panel from B&R that combines a touch screen display, key switch, keyboard and E-stop in a single, ergonomic housing.
A powerful Automation PC 910 provides a high-performance hardware platform for the machine control, CNC and HMI applications. "The ability to unite CNC, PLC, motion and HMI within a single software platform is one of the remarkable aspects that sealed the deal for the B&R solution," concludes Trumpler.
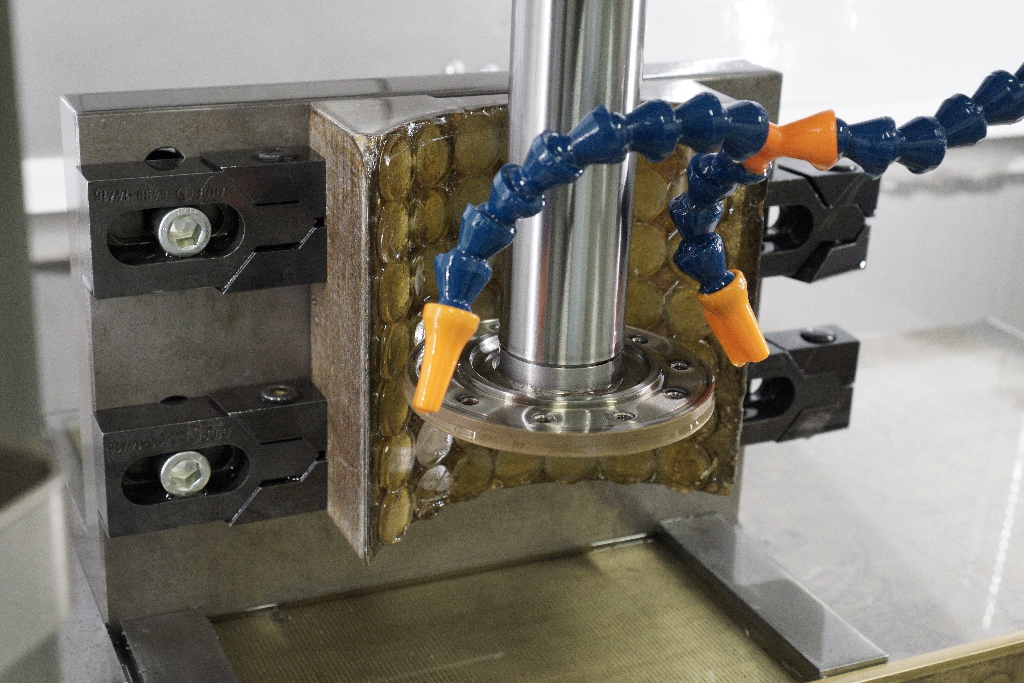