Simple and fast production with ACOPOStrak
The mapp Trak system software simplifies development of applications for the ACOPOStrak track system and optimizes time to market for new products. It prevents shuttles from colliding, crossing virtual barriers or violating configurable speed limits.
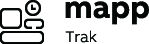
Increase your productivity

Save time and money
mapp Trak makes intelligent track systems easy to work with. The system software helps you get new products to market faster for an attractive return on investment.

Track programming has never been so easy
With mapp Trak, the track system application is created using process-oriented programming. You simply define the rules for how the shuttles should behave on the track.

Use the power of simulation
With the integrated simulation options in mapp Trak, you can test the optimum number and speed of shuttles to maximize productivity.

Benefit from FDA-compliant tracking
mapp Trak links the product data with the respective shuttles and thus makes the entire manufacturing process completely traceable.
Fast track to a fast Trak
The highly scalable ACOPOStrak architecture allows for layouts with track lengths in excess of 100 meters and populated by hundreds of shuttles. Yet, even in the most complex setups, mapp Trak makes the system easy to work with.
Collision impossible
mapp Trak offers key ACOPOStrak functionality out of the box – including collision avoidance, dividing and merging product flows at full speed and calculating optimal routes. Freed from having to worry about these tasks, application developers save valuable engineering time. Even with products of different sizes and weights, there are no collisions. Product size can be configured manually or measured with sensors, and mapp Trak automatically adjusts the shuttle controls to prevent collisions.
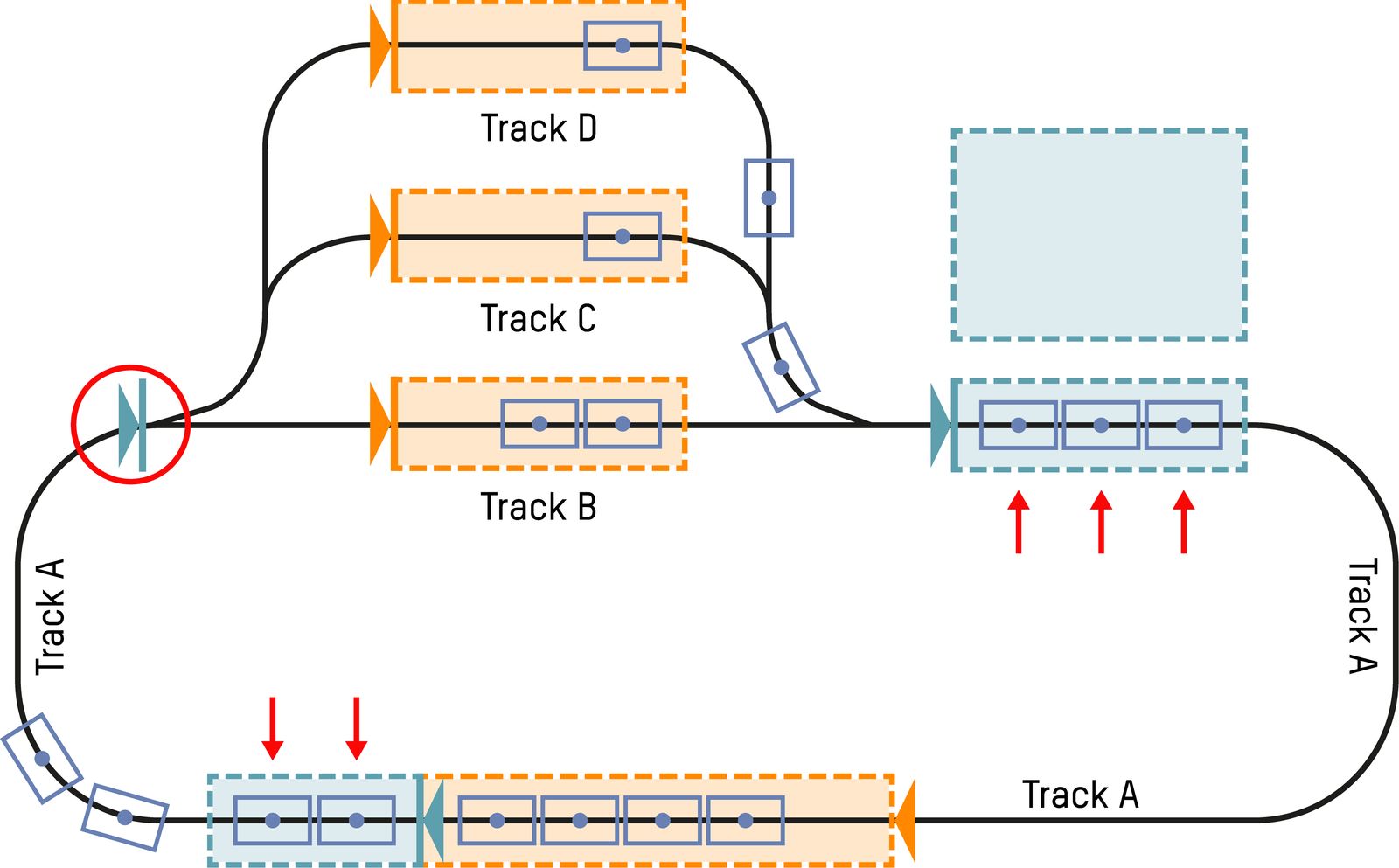
Process-oriented programming
A second factor that substantially simplifies the engineering process is process-oriented programming. With mapp Trak, the application software engineer describes rules for how the shuttles should behave on the track. The rules become active when shuttles pass virtual trigger points. This simple methodology based on state machines makes implementing motion sequences extremely efficient. With ACOPOStrak, there's no need to program axes and motion profiles for each shuttle individually. A further benefit of process-oriented programming is that shuttles can be taken off the track or added without requiring any changes to the application software.
The mapp Trak architecture
The software architecture of mapp Trak is divided into four basic levels. The lowest one, the segment control level, controls the movement of the shuttles located on the respective segment.
The next layer up, the shuttle control level, is where things like the position setpoints for the shuttles are calculated. If the application engineer wants to couple the shuttles to an external axis or to another shuttle, for example using PLC function blocks, that happens at this level. This is also the level that handles shuttles being added to and removed from the track – for example when ACOPOStrak is used in combination with conventional conveyor belts or if shuttles are added and removed by humans or robots.
Software elements on the third level, logistics control, provide automated routing from processing station to processing station.
The fourth level is dedicated to process control. This level also represents the programming interface for the software engineer to describe the process flow.
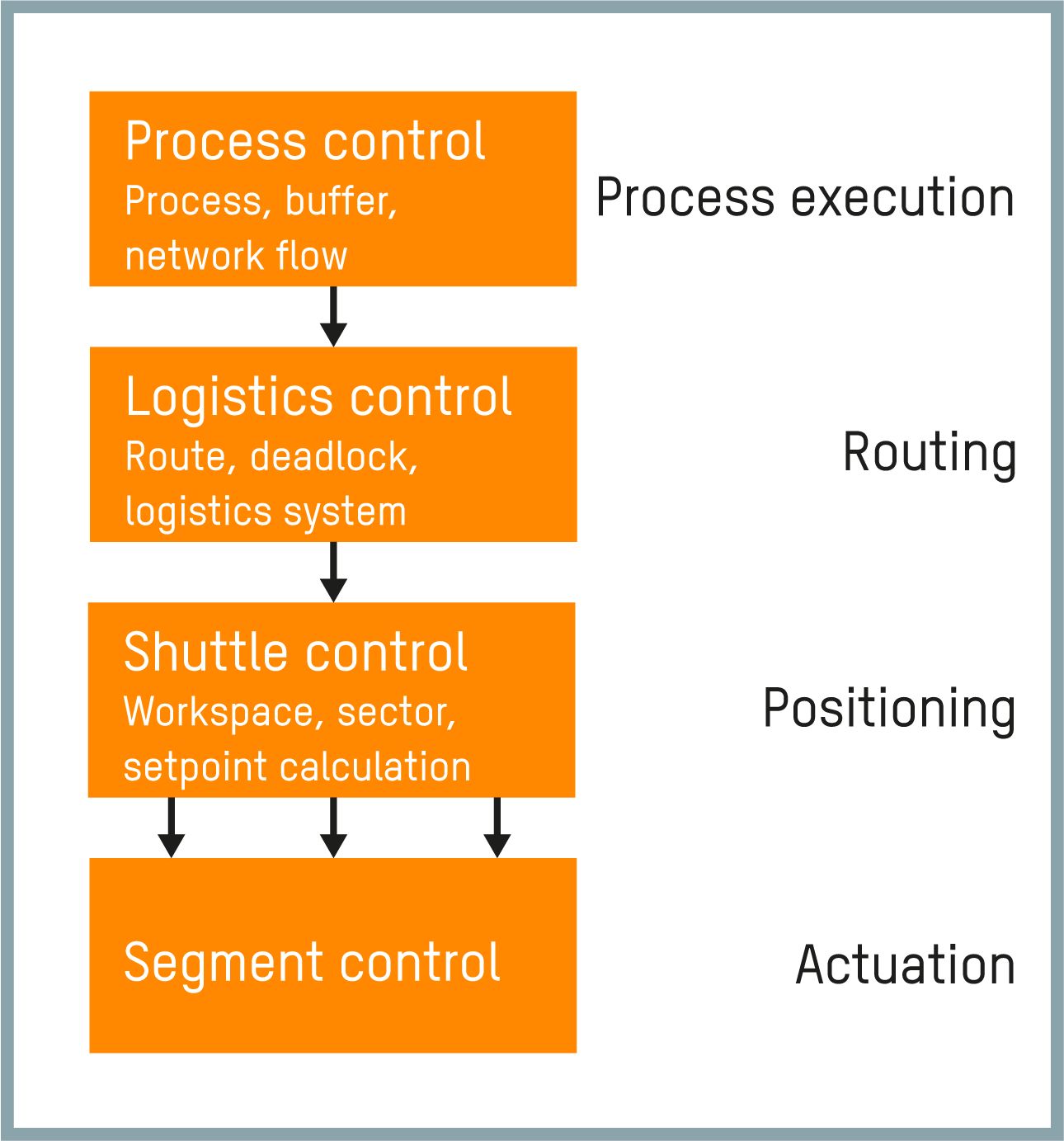