Time-to-market can play a decisive role in the success or failure of a new product. The more flexible the production line, the faster it can adapt and begin turning out a new item. To get that flexibility, OEMs design manufacturing machinery to be highly modular. To see how that works in practice, one need look no further than Ruhlamat.
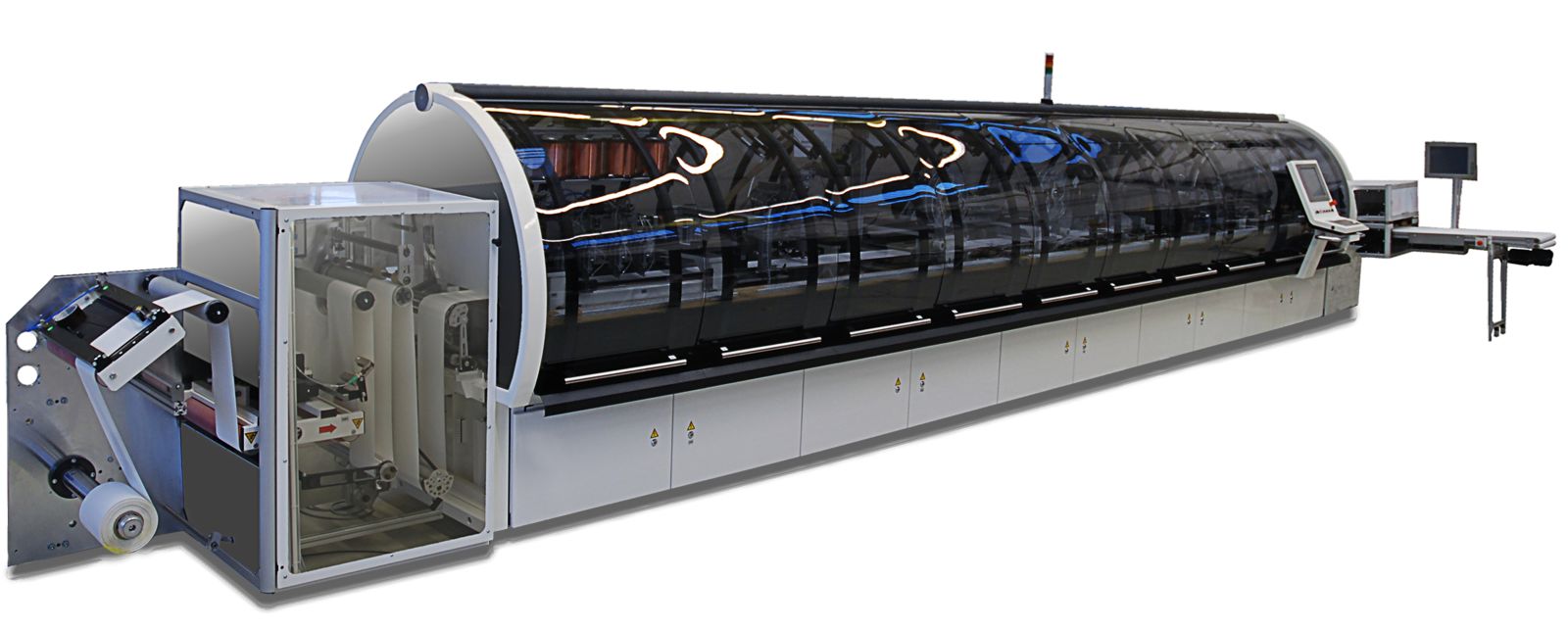
Ruhlamat builds highly flexible assembly lines for the RFID inlays used in credit cards and passports. Among them is the Wire Coil Embedding (WCE) machine series, which includes an array of machine modules that can be arranged to form a completely integrated inlay assembly line. "If you were to build a line like that as a monolith, it would be much more risky and time consuming. So what we were looking for in an automation system was a sustainable reduction in development and commissioning time," says the leader of Ruhlamat's software development team, Martina Oehring. Dedicated mechatronic units handle each of the key processes: from wire laying, component mounting and soldering to testing, punching and finishing.
Maximum modularity
On top of the wide variety of line configurations, there were also demanding technical challenges. A prime example is the module that lays the wire that will serve as the antenna in the finished card. It uses ultrasonic technology to embed extremely thin wire in a substrate with a precision of 10 µm. "We have an inline optical quality inspection module that allows us to mark defective products," adds Oehring.
The WCE has twelve machine modules that can be arranged around the backbone to perform a variety of processes, from wire laying and optical inspection to winding, unwinding and transport. "We designed the modules as integratable units, so that they can each be subject to their own product lifecycle," explains Oehring. "That way, we're able to freely configure each new variant of the machine using standardized machine modules." To do this, Oehring and her team used a function of B&R's Automation Studio programming tool, which makes it possible to encapsulate the software in application modules. "On the inside, all of our modules have the same structure," says Oehring. That includes data handling, operating modes, position calculation and alarm handling, whereby the actual technological functionality is mapped in a main step sequence. That allows the developers to save valuable time by using some modules unchanged in other machine series. "This was a strong argument in B&R's favor, because encapsulation was something we'd been wanting for a long time," says Oehring.
All functions in a coordinated framework
An important component of the modular software project is the superordinate framework in which all the processes are coordinated. In addition to parameter structures and job management, this includes control of operating modes, safety and drive functions, the user interface and the interface to the individual application modules. "The configuration of the framework is an important part of the design phase. With B&R's expert support, we have developed a routine that allows us to achieve the shortest possible processing times," says Oehring.
The framework also includes designing the hardware structure, which is linked to the corresponding logic in Automation Studio via a configuration layer. This separation is essential, because it clearly isolates the hardware from the software. When an application module is added or removed, the two worlds can be linked or separated via the configuration layer alone. "That also works during operation," adds B&R software engineer Tobias Baumgärtner, who has seen the advantages in numerous customer applications, where module replacement is part of a normal changeover process. "The operator only has to stop the machine and can then remove or replace entire modules, even if that changes the configuration of the safety technology," emphasizes Baumgärtner.
Multiple programmers working in parallel
Oehring is especially happy with the ability to have multiple developers working independently on the same system at the same time. "On one particular order, we had to develop numerous new options with a very tight deadline. At times, we had five programmers working simultaneously to develop and deploy their respective modules. Not only did we deliver ahead of schedule – we also significantly reduced the error rate," she reports, not without pride.
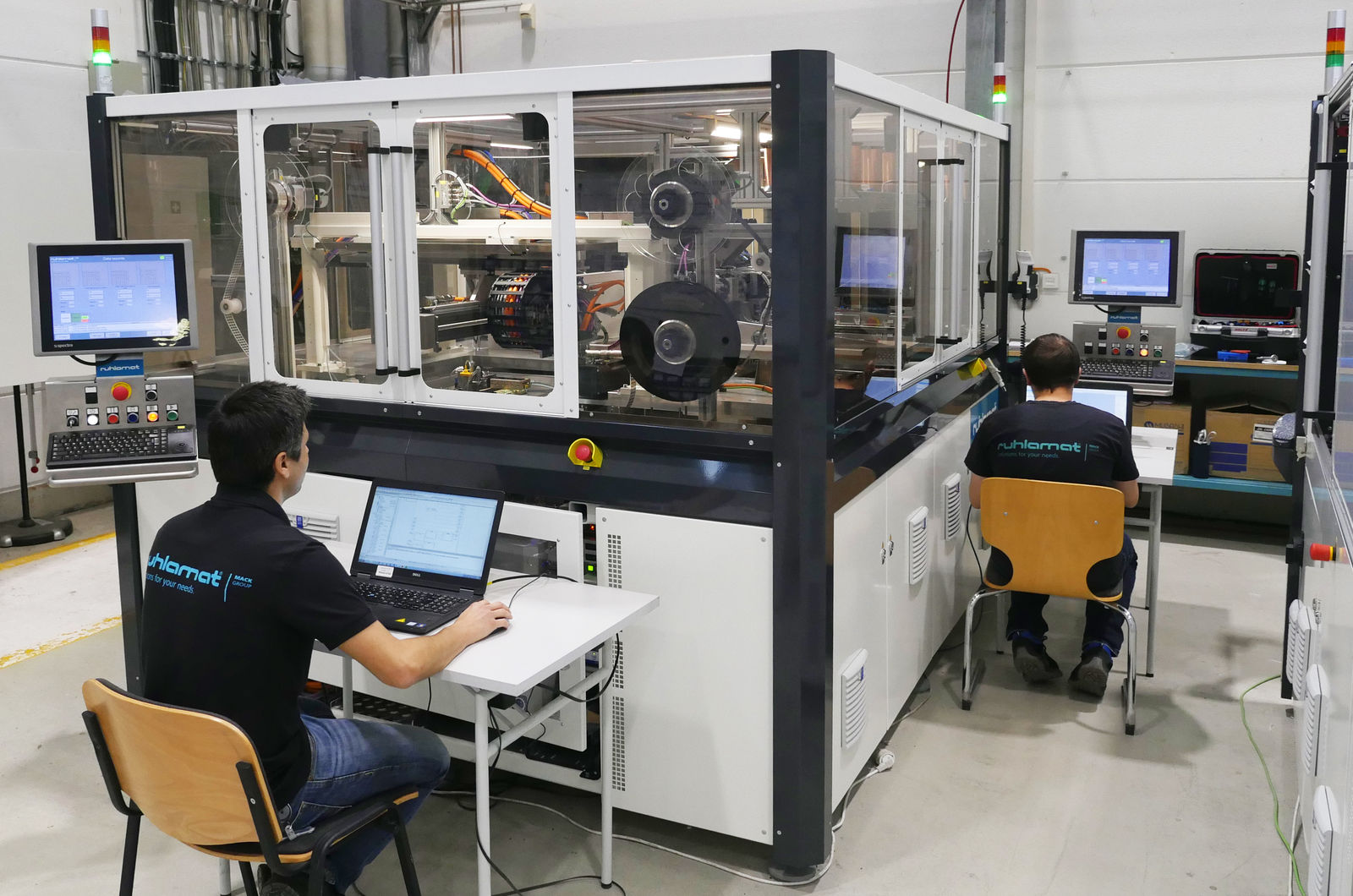
Martina Oehring
Team Leader - Software Development, Ruhlamat
"The fully encapsulated software enables concurrent engineering, which significantly shortens commissioning times while at the same time reducing the error rate."