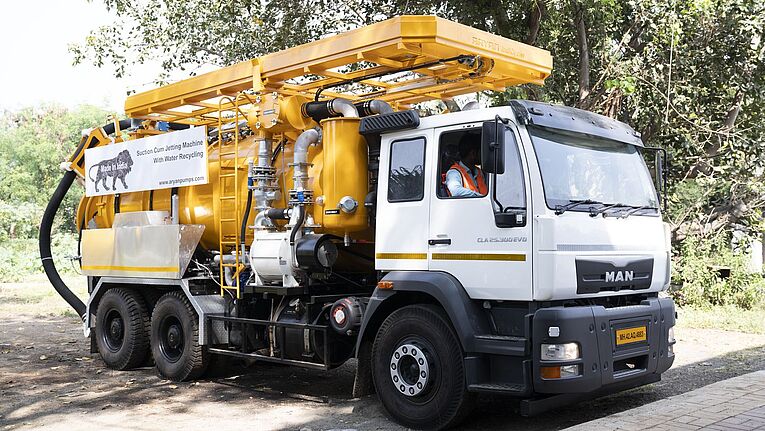
Smart wastewater doesn't waste water
Wastewater management systems rely on municipal cleaning vehicles to keep things running smoothly. Aryan's IndiCycler does the job efficiently and sustainably by recycling extracted sewage water.
Wastewater management systems rely on municipal cleaning vehicles to keep things running smoothly. Aryan's IndiCycler does the job efficiently and sustainably by recycling extracted sewage water.