Avec ses godets à grande capacité, une excavatrice extrait en quelques secondes ce qu'un humain muni d'une pelle extrait en plusieurs semaines. Et plus la quantité de matière extraite par ces machines est importante, plus les arrêts machine imprévus coûtent cher. Les compagnies minières dépensent donc beaucoup d'argent pour éviter les pannes. Le recours à des solutions de maintenance intelligentes permet néanmoins de réduire considérablement ces coûts.
Les excavatrices utilisées aujourd'hui pour l'extraction minière atteignent des dimensions gigantesques. La plus grande au monde atteint 24 mètres de long, 8,8 mètres de large, 11 mètres de haut, et pèse 800 tonnes. Son conducteur contrôle à l'aide d'un simple joystick un énorme godet de 47 mètres cube. En seulement 20 secondes, il peut ainsi extraire 80 tonnes de matières. "Lorsqu'une excavatrice de ce calibre tombe inopinément en panne, l'exploitant de la mine doit s'attendre à d'importantes pertes financières, et l'ensemble de la chaîne logistique est impacté," explique Stefan Taxer, chef de produit Mobile Automation chez B&R.
Pour ces machines géantes, la prévention des arrêts inopinés est donc la priorité numéro un. Il est ainsi d'usage aujourd'hui de surdimensionner les composants rotatifs comme, par exemple, les pompes hydrauliques, les moteurs et les réducteurs, ou de les remplacer à titre préventif à intervalles réduits. De plus, pour réduire le plus possible les arrêts machine, les compagnies minières entretiennent également un stock de pièces détachées à proximité de la mine. "Toutes ces solutions ont en commun qu'elles induisent des coûts supplémentaires," souligne Stefan Taxer. Ces coûts peuvent être réduits en utilisant les méthodes d'analyse et de maintenance les plus récentes.
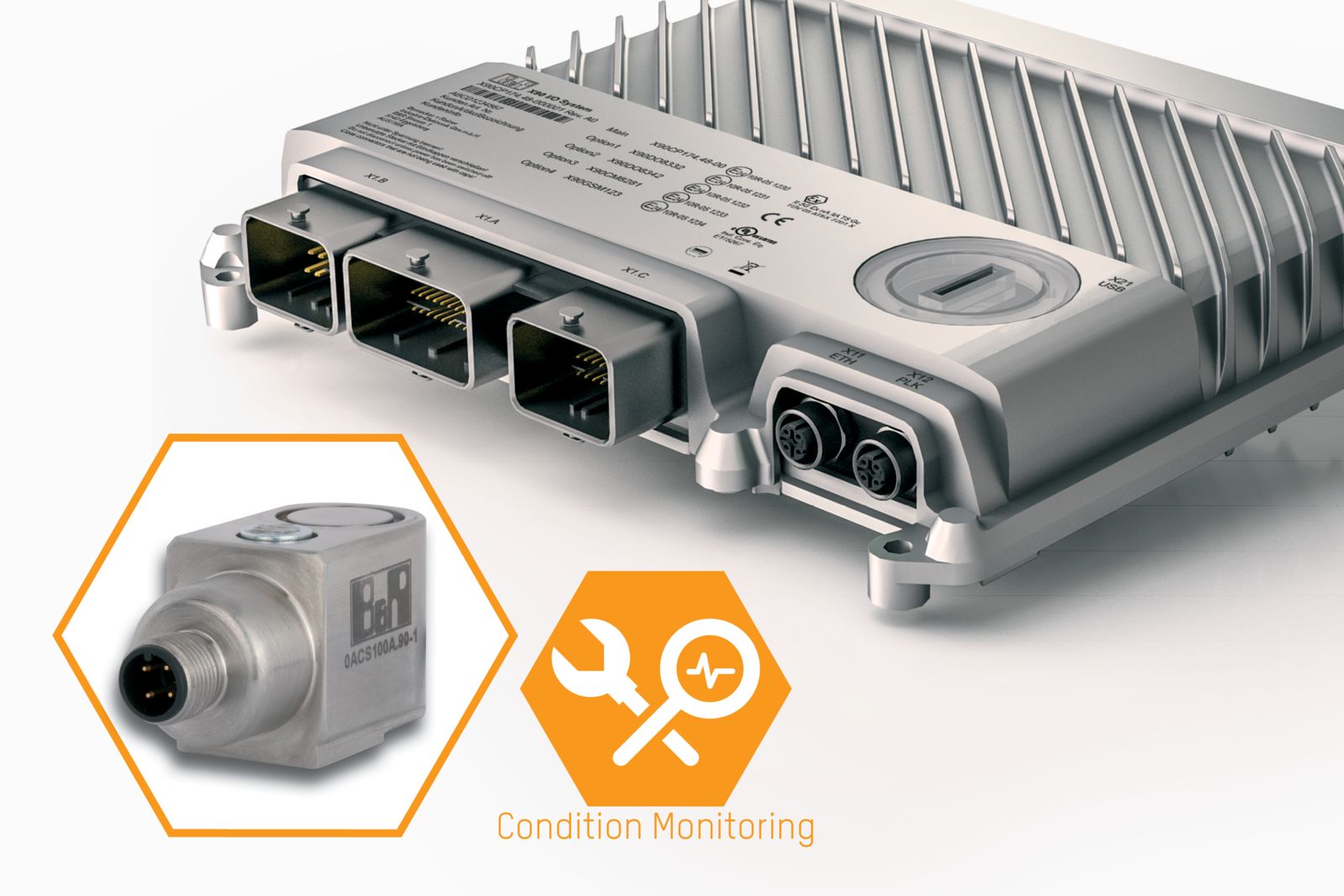
Prédire les défaillances
Les composants machine rotatifs s'usent avec le temps. Même une oreille non avertie peut percevoir la différence de bruit dûe à cette usure. "Les bruits que génèrent les roulements usés d'un roue s'entendent distinctement sur une voiture," indique S. Taxer. Cependant, les excavatrices minières sont si bruyantes qu'elles ne permettent pas de distinguer des bruits anormaux. "La surveillance vibratoire rend ici un grand service."
Les vibrations ne sont rien d'autres que des oscillations à certaines fréquences. Si le système de surveillance conditionnelle utilisé est correctement configuré, un pic de vibration dans une plage de fréquence spécifique sera la signature d'un défaut naissant. L'amplitude du pic permet d'évaluer l'importance du dommage, et donc à quel moment la pièce concernée doit être remplacée.
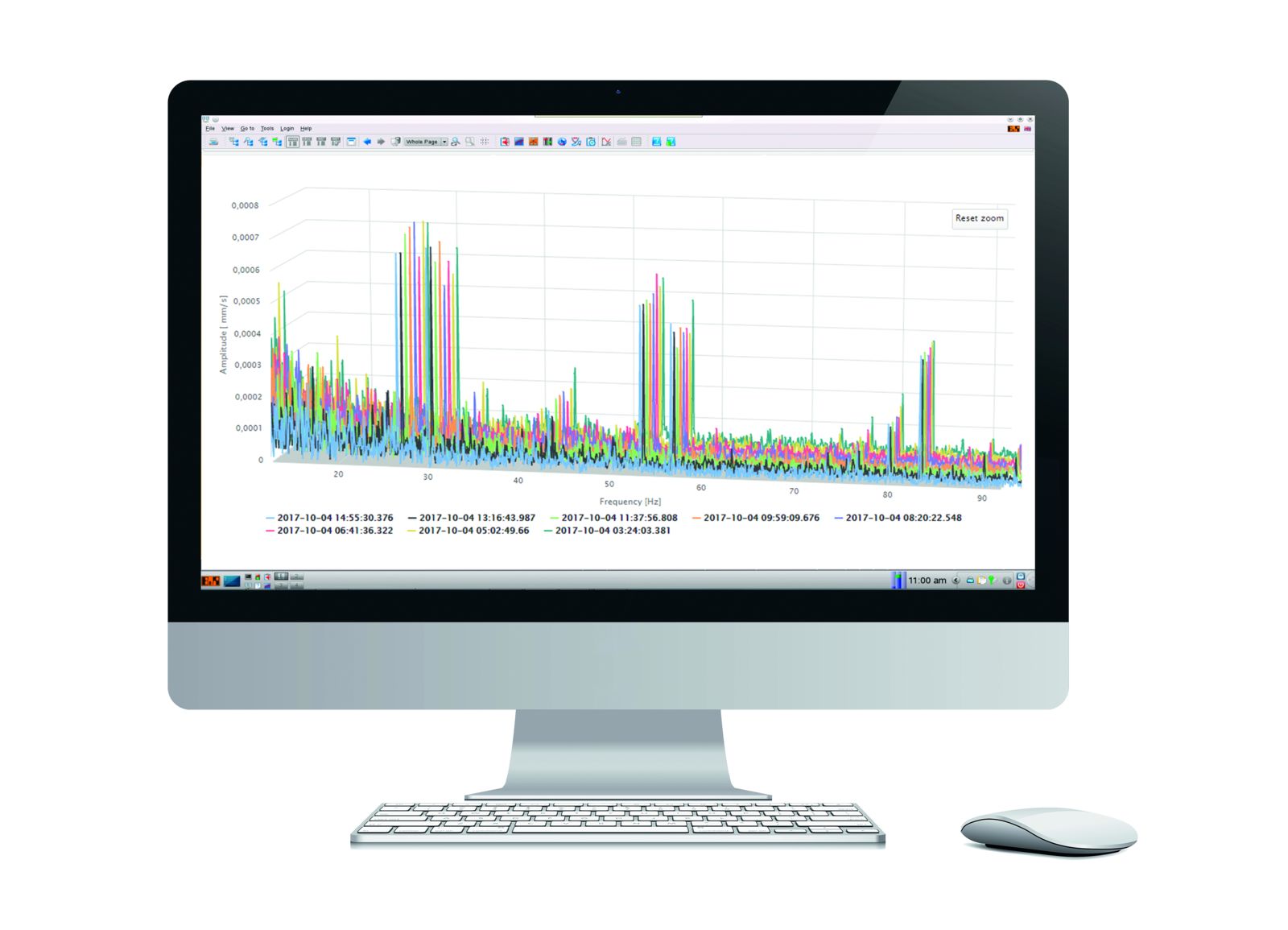
Bien utiliser les données de vibration
"L'évaluation des données de vibration repose sur deux éléments critiques," note S. Taxer : des composants matériels performants pour collecter les données à des fréquences suffisamment hautes, et des logiciels intelligents capables de détecter et filtrer les plus petits écarts à partir d'une énorme quantité de données.
"Notre système modulaire de contrôle et d'E/S X90 offre une plateforme matérielle particulièrement adaptée," selon S. Taxer. Le cœur du système est le contrôleur X90 équipé d'un processeur ARM performant et comptant jusqu'à 48 voies d'E/S multi-fonctions. Modulaire, ce contrôleur peut héberger des cartes optionnelles pour offrir des interfaces, des E/S supplémentaires, ou encore un système de surveillance conditionnelle.
"Combinée avec nos composants logiciels mapp, cette plateforme permet de disposer d'un système très performant pour surveiller l'état de santé des machines et informer les opérateurs à temps qu'une action doit être effectuée," ajoute S. Taxer. "Une fois paramétrés, les composant mapp communiquent automatiquement les uns avec les autres, ce qui réduit le travail de programmation au strict minimum."
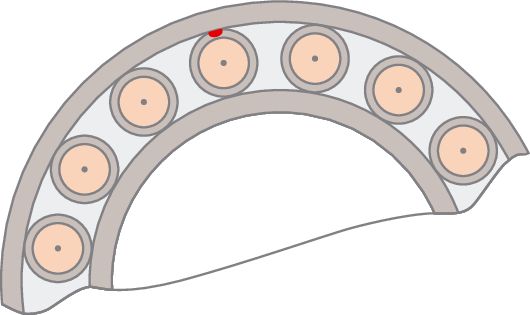

Recevoir un email de sa machine
L'interaction entre le système d'alarmes mapp Alarm et le système de notification mapp Tweet illustre parfaitement la manière dont communiquent les composants mapp. "Le simple fait de créer un lien entre ces composants permet l'envoi automatique d'un email ou d'un SMS au technicien de maintenance dès qu'une alarme se produit," explique S. Taxer. Le message peut indiquer, par exemple, qu'un roulement est usé et qu'il doit être remplacé au bout d'un certain temps.
"Le système d'alarmes est simple à configurer. Mais le plus important est l'impact que cela peut avoir sur la stratégie de maintenance de l'exploitant," ajoute S. Taxer. Les composants sont remplacés lorsque leur état le justifie vraiment et non à intervalles fixes, ce qui évite de remplacer des composants coûteux et en parfait état bien avant la fin de leur durée de vie. Dès lors, la planification de la maintenance peut être optimisée, et les stocks de pièces détachées nettement réduits.
L'utilisateur a également la possibilité de mettre à disposition du fabricant de machines des données de condition monitoring. "Un fabricant qui connaît l'état de santé de ses machines en exploitation peut ainsi considérablement réduire la probabilité qu'elles tombent en panne," indique S. Taxer. Dans l'intérêt, bien sûr, de l'exploitant.
Les fabricants d'équipements mobiles peuvent aussi utiliser des données pour optimiser la conception, ou développer de nouveaux modèles économiques en proposant, par exemple, la surveillance des équipements comme un service. L'exploitant ne doit plus alors se soucier de la maintenance des machines. Il est simplement informé si une pièce de remplacement va être livrée et montée.

Stefan Taxer, chef de produits Mobile Automation chez B&R.
Situation gagnant-gagnant
S. Taxer souligne également un autre aspect : "Il n'est plus nécessaire de complexifier l'ingénierie des composants." Les deux parties y gagnent : la fabricant peut réduire ses coûts de fabrication, et l'utilisateur dépense moins pour sa machine. Le contrôleur X90 peut être connecté à des architectures CAN existantes. L'option Condition Monitoring peut donc être aussi mise en œuvre dans des machines existantes. "Cette approche permet aussi de migrer par étapes vers un bus temps réel moderne permettant de gérer les gros volumes de données que génèrent les machines d'aujourd'hui."
Les stratégies utilisées jusqu'à présent pour éviter les arrêts machine imprévus coûtent beaucoup d'argent et de ressources. Avec le système X90 et l'option Condition Monitoring de B&R, les excavatrices deviennent plus fiables, et leur maintenance devient nettement moins coûteuse.
Auteur : Carmen Klingler-Deiseroth, journaliste freelance
Transfert d'expérience
La société B&R a près de 40 ans d'expérience dans la conception et la fabrication de systèmes d'automatisation innovants pour de nombreuses industries. Depuis des années, elle met en œuvre avec succès des protocoles Ethernet Industriel haute performance comme POWERLINK. Le système de contrôle X90 capitalise tout ce savoir-faire et offre ainsi aux fabricants d'équipements mobiles une solution durable et à haute valeur ajoutée pour répondre aux défis d'aujourd'hui et demain.