Conectar los módulos individuales de la máquina para formar una línea de producción continua puede representar mucho trabajo y ocupar mucho espacio. Optima ha conseguido unir una máquina de llenado y envasado de forma que encajan perfectamente ambos procesos. Ello es posible gracias a una solución única que incluye el sistema de transporte inteligente ACOPOStrak de B&R.
"Para nosotros, los fabricantes de máquinas, la conexión de los diferentes módulos de las máquinas es siempre un reto especial", comenta Andreas Dreschner, director técnico de ventas de Optima. Cuando Optima arrancó el proyecto en la primavera de 2019, evaluaron posibles sistemas de transporte para interconectar las unidades de llenado y envasado. "Para nuestra aplicación, no había ningún otro sistema que ofreciera el mismo tipo de flexibilidad o que cumpliera nuestros requisitos de velocidad y dinámica como lo hace ACOPOStrak", explica Dreschner.
La nueva aplicación se utilizó por primera vez en una línea de llenado y envasado de un minorista de alimentación holandés para producir cápsulas de café de aluminio individuales. Cada una de las lanzaderas incluye un soporte de producto para sostener una cápsula de café, lo que significa que cada cápsula puede moverse a través de la línea de producción con total independencia del resto. Ello permite agrupar cualquier número de cápsulas sobre la marcha durante el transporte.
Flujo de producción eficiente
"Una de las dificultades de esta aplicación eran los huecos que se producen durante el proceso de fabricación", comenta Dreschner. Esto ocurre, por ejemplo, cuando se rechazan cápsulas por no pasar la inspección de calidad. Dado que incluso una ligera variación en el peso, un sellado imperfecto o una pequeña desviación en la posición de la tapa pueden hacer que se rechace una cápsula, los operarios de la planta asumen una tasa de rechazo de entre el 0,2 y el 0,3 por ciento. "Las cápsulas suelen envasarse en cajas de diez o más unidades, por lo que, en última instancia, se produce un porcentaje aún mayor de cajas defectuosas".
Gracias a la capacidad de las lanzaderas ACOPOStrak de moverse de forma independiente, pueden cerrarse fácilmente los huecos en el flujo de producción. Las cápsulas que no pasan el control de calidad se eliminan de inmediato. "ACOPOStrak pasa inmediatamente a la siguiente cápsula, y el flujo de productos continúa sin perder el ritmo", explica Dreschner.
Agrupación flexible
Una vez rellenadas y selladas las cápsulas de café, la línea de llenado pasa doce cápsulas a la vez para realizar el siguiente paso de producción. La entrada de la línea de envasado, en cambio, tiene quince carriles. Aquí, de nuevo, la línea de producción aprovecha las ventajas de las lanzaderas flexibles del sistema de transporte de B&R. ACOPOStrak recibe grupos de doce cápsulas de la máquina de llenado y, cuando llegan a la entrada de envasado, se han reagrupado en grupos de quince.
Configure grupos sobre la marcha
Los diferentes grupos de productos que van a envasarse juntos suelen distribuirse mediante tornillos de alimentación, ruedas de alimentación, cintas y cadenas. Para que la máquina produzca una configuración diferente de grupos, es necesario modificar el hardware manualmente. Con el sistema de Optima, las lanzaderas facilitan enormemente el cambio entre grupos. Las configuraciones pueden cambiarse sobre la marcha durante el funcionamiento, simplemente seleccionando la receta correspondiente en el terminal de operario.
Cuatro metros menos
En términos de espacio, la innovadora solución de Optima tiene una clara ventaja sobre los sistemas que utilizan tecnología convencional para la agrupación de productos. "Con un diseño convencional con tornillos, la función de agrupación requiere una máquina con dos campos, cada uno de 220 centímetros de longitud", explica Dreschner. "En cambio, la nueva solución ACOPOStrak añade solo 80 centímetros a la longitud total del sistema, por lo que es casi cuatro metros más corto que antes".
No obstante, consigue un mayor rendimiento que su homólogo convencional: el minorista de alimentación holandés produce y envasa 720 cápsulas en 72 cajas cada minuto. Hay un total de 80 lanzaderas en circulación. Se distribuyen en dos pistas ovaladas independientes y apiladas, de 7,2 metros de longitud cada una. Las lanzaderas aceleran a 30 m/s² y alcanzan velocidades máximas de hasta 2,6 m/s.
Una de las razones de la división en dos pistas fue la separación necesaria entre los productos de menos de 50 mm, aunque las propias lanzaderas ya tienen 50 mm de ancho. Por lo tanto, los segmentos ovalados de la pista y los soportes de los productos están diseñados de tal manera que las pinzas del segmento ovalado superior y las del segmento ovalado inferior se apoyan alternativamente en el mismo nivel. En este nivel, los soportes de los productos solo tienen unos 40 mm de ancho cada uno, por lo que puede conseguirse la separación de productos necesaria inferior a 50 mm.
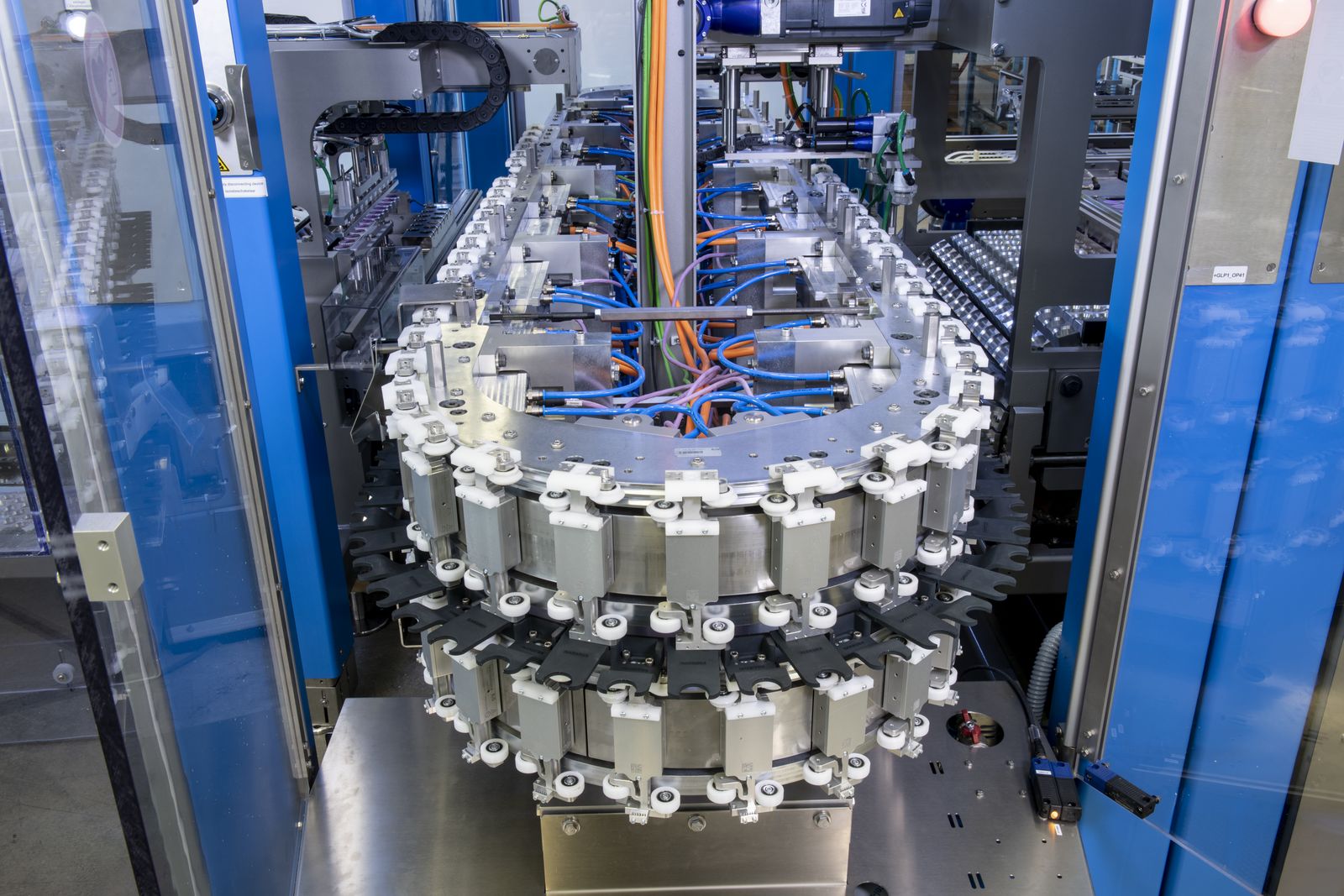
Transporte suave
A pesar de su dinamismo, el manejo de las cápsulas es notablemente cuidadoso. "En comparación con un proceso de agrupación convencional, hemos reducido considerablemente el número de pasos de producción", afirma Dreschner. "Los soportes de productos también evitan que las cápsulas choquen entre sí durante el reagrupamiento". Por lo tanto, ACOPOStrak resulta especialmente adecuado para productos sensibles como las cápsulas de café individuales de aluminio de alta gama.
Ingeniería orientada a la simulación
Las opciones de simulación inteligente que ofrece el software de ingeniería de B&R fueron de gran ayuda para desarrollar la máquina. "Gracias a la posibilidad de realizar simulaciones en nuestro concepto inicial, nos dimos cuenta muy pronto de que una pista no sería suficiente", afirma Dreschner.
"Tras dividirlo en dos pistas y repetir la simulación, pudimos avanzar con la confianza de que el proceso de transporte se desarrollaría según lo previsto y que alcanzaríamos los objetivos de rendimiento del cliente sin sorpresas desagradables de última hora". El esfuerzo adicional para la simulación fue mínimo. Optima pudo aprovechar todas las reglas del proceso creadas para la simulación y aplicarlas en la aplicación real de la máquina simplemente pulsando un botón.
Ventaja competitiva gracias a una tecnología innovadora
El diseño modular, la sencilla implementación del movimiento de la lanzadera y la ayuda de los expertos de B&R ayudaron a acortar la curva de aprendizaje de Optima con la nueva tecnología. "ACOPOStrak estaba todavía parcialmente en estado de prototipo al comienzo del primer proyecto", observa Dreschner. "La cooperación entre todos los implicados fue perfecta. Desde los desarrolladores de software hasta la cúpula directiva, todo el mundo tenía el mismo objetivo. Esto es lo que nos ha permitido conseguir que el sistema sea apto para el uso industrial en poco tiempo". Los esfuerzos han dado sus frutos: el primer sistema entregado ya funciona sin problemas ininterrumpidamente para la satisfacción de todos.
Y no solo eso: "La solución es un verdadero hito para nosotros y no deja de sorprender a cualquiera que lo ve en acción", comenta Dreschner. "No existe nada igual en nuestro mercado. Resulta especialmente interesante para los fabricantes de marcas blancas, que producen para clientes muy diferentes y variados y que siempre han deseado el tipo de flexibilidad de agrupación sobre la marcha que ahora podemos ofrecer".
- Ventajas de la agrupación ACOPOStrak
- Ahorro de espacio
- Agrupación flexible
- Flujo de productos sin huecos
- Alto rendimiento
- Cuidadoso transporte de los productos
- Diseño de uso alimentario
![]() | Andreas Dreschner Director técnico de ventas de Optima "Para nuestra aplicación, no había ningún otro sistema que ofreciera el mismo tipo de flexibilidad o que cumpliera nuestros requisitos de velocidad y dinámica como lo hace ACOPOStrak". |