Cuando nos apresuramos en la construcción de una máquina nueva sin realizar pruebas exhaustivas, corremos el riesgo de que algunos defectos fundamentales en el diseño pasen desapercibidos hasta la puesta en marcha. En ese momento, cualquier cambio en la máquina terminada es extremadamente costoso y lleva mucho tiempo llevarlo a cabo. Por ello, un número cada vez mayor de fabricantes de máquinas están utilizando modelos simulados -gemelos digitales- para probar e implementar nuevos diseños de máquinas de una forma rápida y rentable.
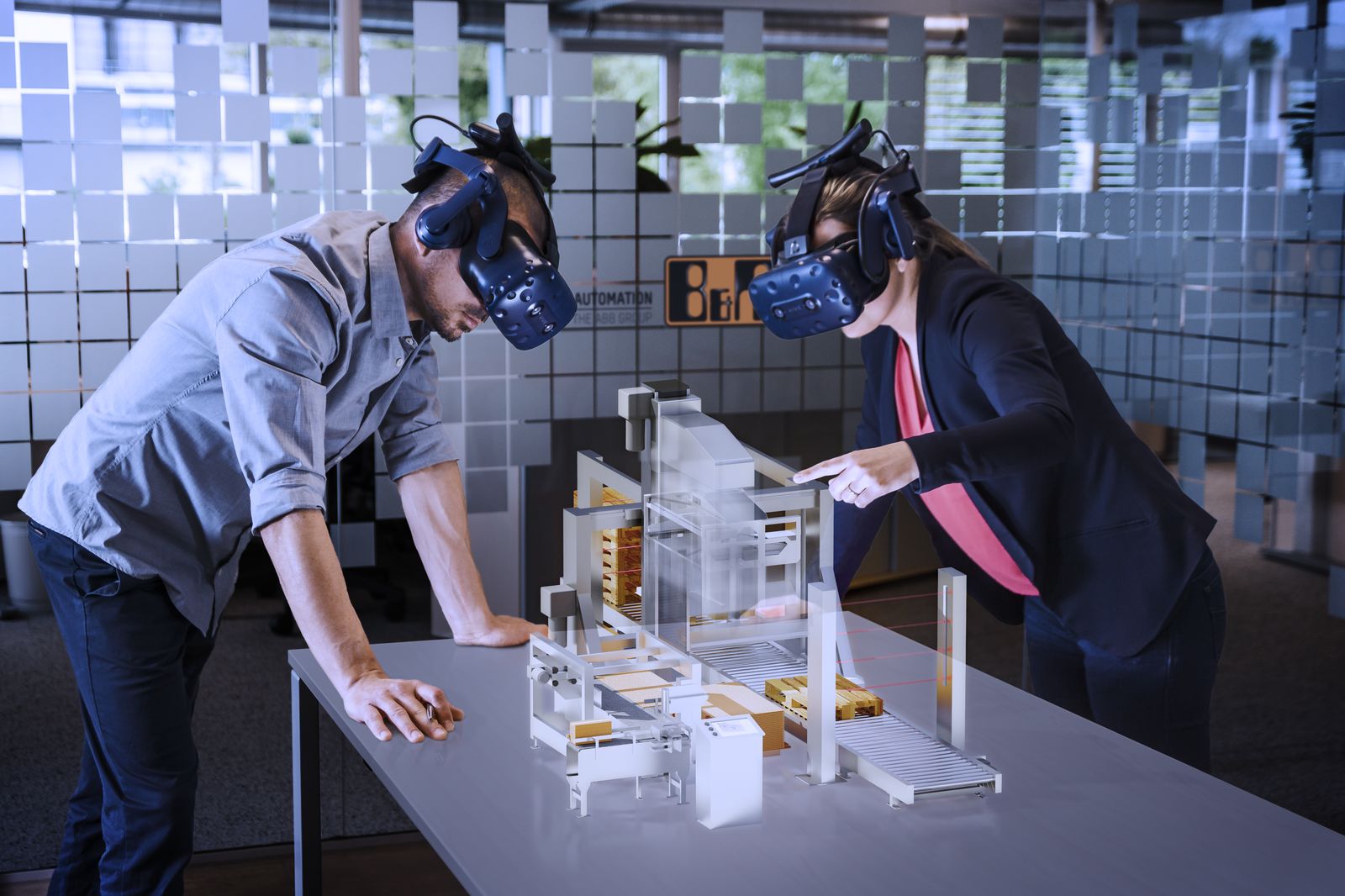
Cuando se diseña una máquina nueva, una de las principales preocupaciones de los fabricantes de equipos originales es construirla y comercializarla lo antes posible. Los retrasos, las complicaciones y los prototipos fallidos pueden amenazar rápidamente la viabilidad económica de un proyecto. Los enfoques convencionales para el desarrollo y la implementación de las máquinas ya no están a la altura de las circunstancias. Aquí es donde entran en juego las gemelos digitales.
La dualidad digital acompaña a la máquina durante todo su ciclo de vida, desde la planificación conceptual hasta el servicio posventa. Se desarrolla, adapta, mejora y comprueba en paralelo a la máquina real. Cualquier defecto de diseño o cambio necesario se hace evidente en la simulación, antes de correr con los gastos de construir un prototipo físico.
Simular los procesos de producción
Además de simular el hardware y el software de la máquina, la dualidad digital también debe ofrecer una representación realista y en tiempo real de los procesos de producción. La simulación del movimiento de los productos en una cinta transportadora, por ejemplo, ayuda a identificar posibles colisiones desde el principio. "Una herramienta de simulación debe visualizar procesos de alta velocidad junto con el control real", observa Kurt Zehetleitner, jefe del equipo de I+D de simulación y tecnología de dualidad digital de B&R. "Así que, además de ser muy potente, también debe poder trabajar en tiempo real."
Estos son dos criterios que industrialPhysics cumple a la perfección. Gracias a la integración de un motor físico en tiempo real, el software simula el comportamiento dinámico de la máquina en 3D. Todas las fuerzas dinámicas que influyen en el flujo de materiales pueden probarse mediante la dualidad digital. El desarrollador de la máquina puede comprobar, visualmente y al instante, cómo las diferentes combinaciones de componentes de la máquina afectan a su comportamiento. También pueden identificarse y eliminarse rápidamente los períodos de inactividad innecesarios.
Importar datos de CAD
industrialPhysics genera gemelos digitales utilizando los datos de CAD de la máquina. El desarrollador solo tiene que importar estos datos en formato STEP para crear una dualidad digital de forma rápida y sencilla. La dualidad digital puede utilizarse para comprobar cómo afectarán a la máquina las diferentes disposiciones cinemáticas, las configuraciones de los componentes y los cambios de código.
B&R ha integrado industrialPhysics en su entorno de ingeniería Automation Studio. "El enlace directo que se establece entre la herramienta de simulación y Automation Studio permite a los desarrolladores ejecutar el modelo virtual de la máquina directamente en el PC, en una configuración de hardware-in-the-loop o de software-in-the-loop, y conectarse con el control", comenta Zehetleitner.
Realidad virtual
Para que los desarrolladores puedan interactuar directamente con la máquina simulada sin distracciones externas, el modelo debe estar disponible en tres dimensiones. industrialPhysics ofrece la opción de ver la dualidad digital con un casco de realidad aumentada o de realidad virtual. El desarrollador podrá ver la máquina planificada en un espacio tridimensional y con movimientos simulados, incluso en cuatro dimensiones. "Con un dispositivo de realidad virtual, el desarrollador puede evaluar los procesos de producción mientras se realiza la simulación. También puede conectarse a un control real o comprobar el manejo", comenta Zehetleitner.
A diferencia de un dispositivo de realidad virtual, el dispositivo de realidad aumentada superpone la dualidad digital al entorno real de la máquina. Ello permite probar situaciones hipotéticas al planificar y desarrollar máquinas con objetos en movimiento. Puede obtenerse información del control en tiempo real y verla junto con la simulación. Los sistemas de realidad virtual y realidad aumentada pueden integrarse fácilmente en el software en cuestión de minutos. Los modelos de simulación de industrialPhysics se muestran directamente en el dispositivo de realidad virtual o de realidad aumentada, en vez de hacerlo en la pantalla del PC.
Puesta en marcha virtual
Una vez desarrollados el hardware y el software de una máquina y comprobados los procesos de producción, llega el momento de la puesta en marcha virtual. Gracias a la dualidad digital, el proceso de puesta en marcha puede repetirse una y otra vez hasta que todo funcione a la perfección. El primer prototipo físico se construye solo cuando todo funciona perfectamente en la puesta en marcha virtual. "La puesta en marcha virtual es extremadamente económica comparada con la real. La dualidad digital se utiliza para eliminar el máximo número de errores posible y ejecutar tantas iteraciones de prototipos como sea necesario antes de construir y poner en marcha la máquina real", explica Zehetleitner. Y esto tiene una influencia positiva en el retorno de la inversión.
Doble digital en el armario eléctrico
No obstante, las ventajas de una dualidad digital no se limitan a la puesta en marcha. Las fábricas conectadas de la IoT industrial generan y procesan unos enormes volúmenes de datos de funcionamiento. Una dualidad digital puede aprovechar estos datos. "Suministrada con los datos en tiempo real de la máquina, la dualidad digital funciona como una copia virtual de la máquina en el armario eléctrico", explica Zehetleitner. Si el comportamiento de la máquina real es distinto al de la dualidad digital, por ejemplo debido al desgaste de un rodamiento, la diferencia se detecta inmediatamente. Los datos recopilados pueden utilizarse para el mantenimiento predictivo, la notificación de averías o los sistemas de mantenimiento remoto.
Una dualidad digital también resulta útil cuando llega el momento de actualizar o de ampliar la máquina. La información obtenida durante el funcionamiento puede utilizarse en el proceso de desarrollo. El fabricante de la máquina puede utilizar el modelo de simulación para comprobar las modificaciones planificadas. Así se minimiza el tiempo que la máquina debe estar inactiva para implementar los cambios.
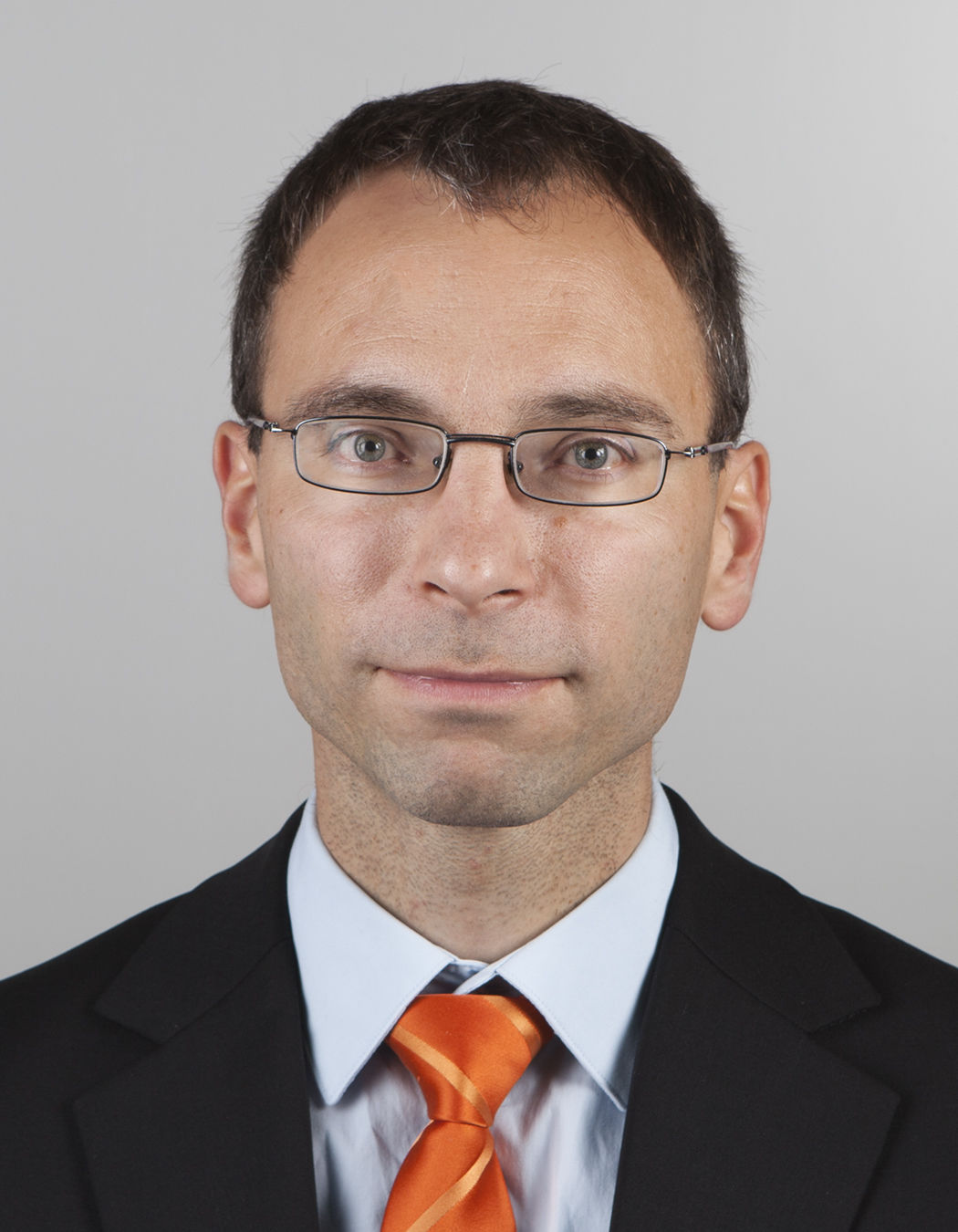
Autora: Carola Schwankner, editora de comunicaciones corporativas de B&R
La dualidad digital como servicio
Para ayudar a los clientes que desean crear una dualidad digital, B&R ofrece un paquete especial de asistencia. Los desarrolladores de B&R construyen un complejo modelo de la máquina utilizando los datos de CAD que tienen a su disposición, una forma rápida y rentable de empezar los proyectos de desarrollo sin problemas. En Automation Studio, la herramienta de ingeniería de B&R, se utiliza la dualidad digital para la verificación inicial y las pruebas de integración. Todo el proyecto de desarrollo se vuelve instantáneamente más predecible y eficiente de gestionar. La dualidad digital también puede utilizarse de inmediato para la comunicación dentro de los equipos de desarrollo individuales.