Como parte de sus esfuerzos para reducir las emisiones de CO2, los fabricantes de automóviles están construyendo las carrocerías de los vehículos con materiales ligeros como el aluminio y compuestos de carbono, combinados con acero de alta resistencia y ultra alta resistencia. Para resolver la difícil tarea de unir estos diferentes materiales, EJOT ha desarrollado y patentado el nuevo proceso EJOWELD, implementado gracias al uso de la tecnología de B&R.
El proceso de soldadura por puntos que se aplica en la construcción de las carrocerías es muy exigente. La resistencia de las juntas y el tiempo de ciclo alcanzable están sujetos a las mismas exigencias que para las juntas soldadas. Además, existe un amplio abanico de condiciones tecnológicas que deben cumplirse y documentarse con precisión para las diferentes combinaciones de materiales. Además, la herramienta guiada por robot debe poder alcanzar todas las posiciones requeridas en la carrocería sin colisiones.
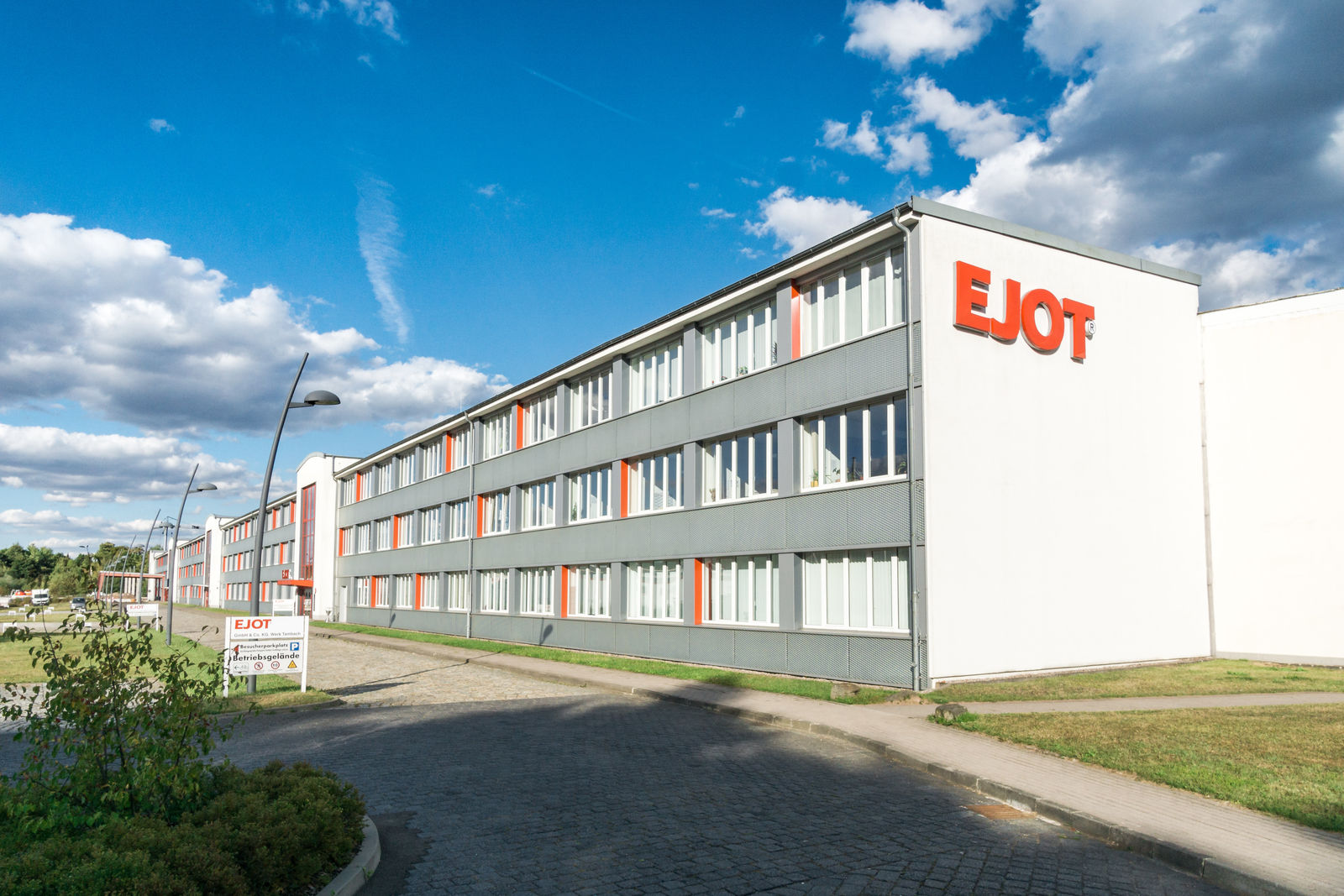
Soldadura por fricción de alta precisión
A primera vista, el proceso de soldadura por fricción utilizado en la solución EJOWELD parece relativamente sencillo. Una herramienta de ajuste presiona y gira uno de los elementos de conexión a través del material exterior más blando en un proceso de cuatro etapas, y la fricción resultante lo calienta hasta unos 1100 °C, uniéndolo de manera permanente con la capa más dura subyacente. Sin embargo, el problema está en los detalles. Para empezar, todo el proceso dura solamente entre comprendida entre 0,7 y 1,8 segundos. "Si no nos ceñimos a los parámetros de proceso con mucha precisión", explica Schrodt, "la unión no se mantendrá y, en poco tiempo, las capas comenzarán a separarse". Para monitorizar el proceso y almacenar los resultados de forma que se pueda garantizar la calidad, se registran hasta 30.000 entradas de datos durante cada proceso de soldadura. "Se trata de una tarea bastante exigente para el sistema de control", comenta Robert Heiland, que lidera el desarrollo de EJOWELD. "La tecnología POWERLINK, ACOPOSmulti y Automation PC de B&R realiza un trabajo excepcional a la hora de controlar el proceso".
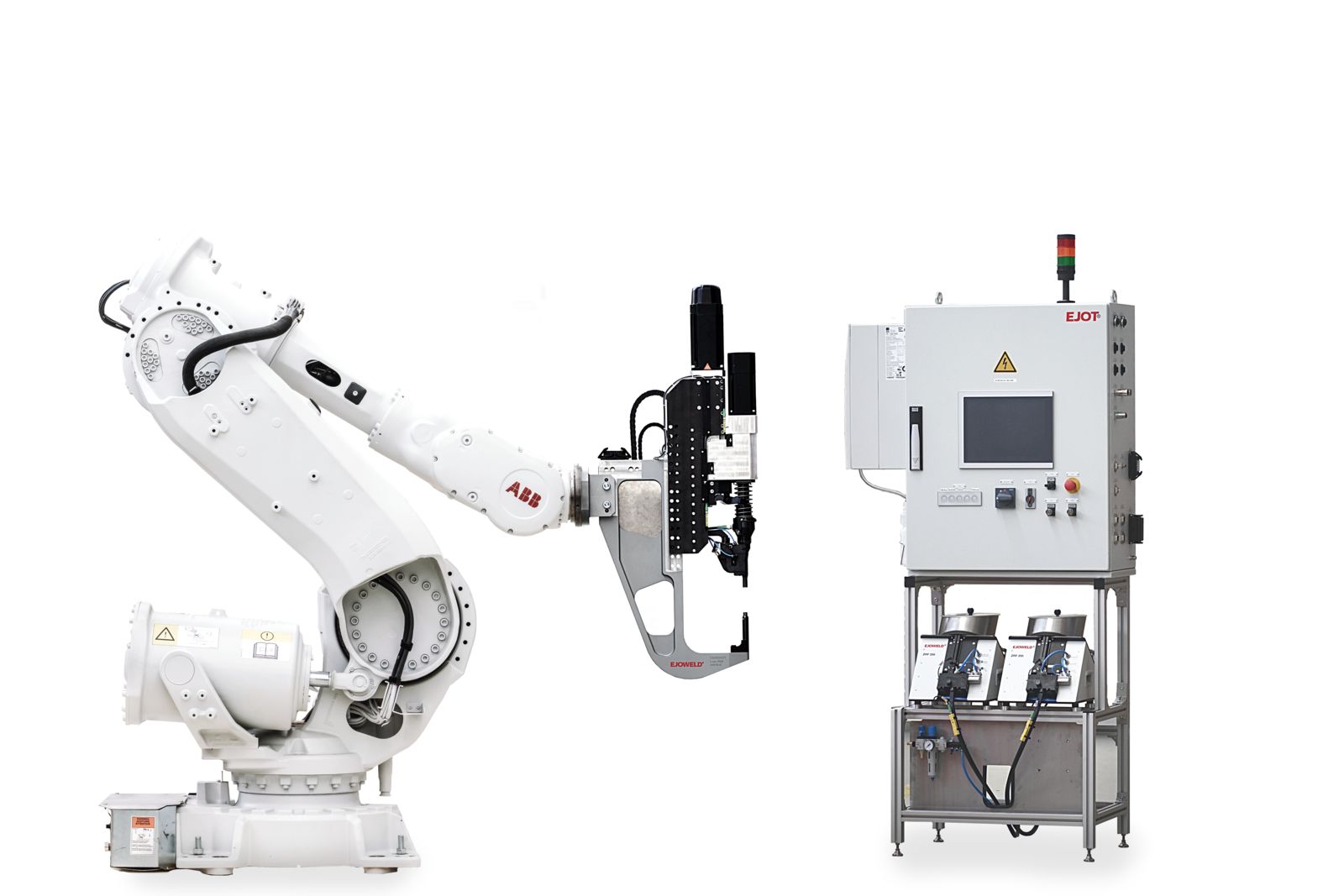
Equipado para uso global
"Para poder implementar la solución en cualquier parte del mundo, el suministro de energía para la tecnología de los servoaccionamientos debe ser independiente de la red eléctrica. Esto es importante para garantizar unas condiciones de procesamiento uniformes sin tener que instalar diferentes componentes para cada tipo de red eléctrica". Precisamente por eso, B&R diseñó los módulos de alimentación de su servoaccionamiento ACOPOSmulti para alimentar el bus de continua con una tensión constante de 750 VCC en una amplia gama de tensiones y frecuencias de red. La potencia reactiva está regulada a cos φ = 1, lo cual es importante para la regeneración optimizada de la red eléctrica.
La precisión del servoaccionamiento garantiza una calidad óptima
Durante el proceso de soldadura por fricción, es necesario alternar entre diferentes procesos de control en tiempo real. "Debemos poder identificar el momento en que el elemento de fricción alcanza el material más duro con una precisión de solo unos pocos microsegundos para poder cambiar al proceso de control correspondiente", comenta Heiland. El servoaccionamiento lee los valores de un sensor de fuerza axial independiente y los aplica de forma altamente dinámica como parámetros de entrada adicionales en el actual lazo de control. Se incorporan señales de control adicionales desde dispositivos periféricos que deben procesarse en cuestión de microsegundos.
Estas señales son leídas por los módulos de E/S X67 de B&R instalados en la herramienta de configuración en las inmediaciones del proceso, y se transmiten directamente al servoaccionamiento y al control a través de POWERLINK.
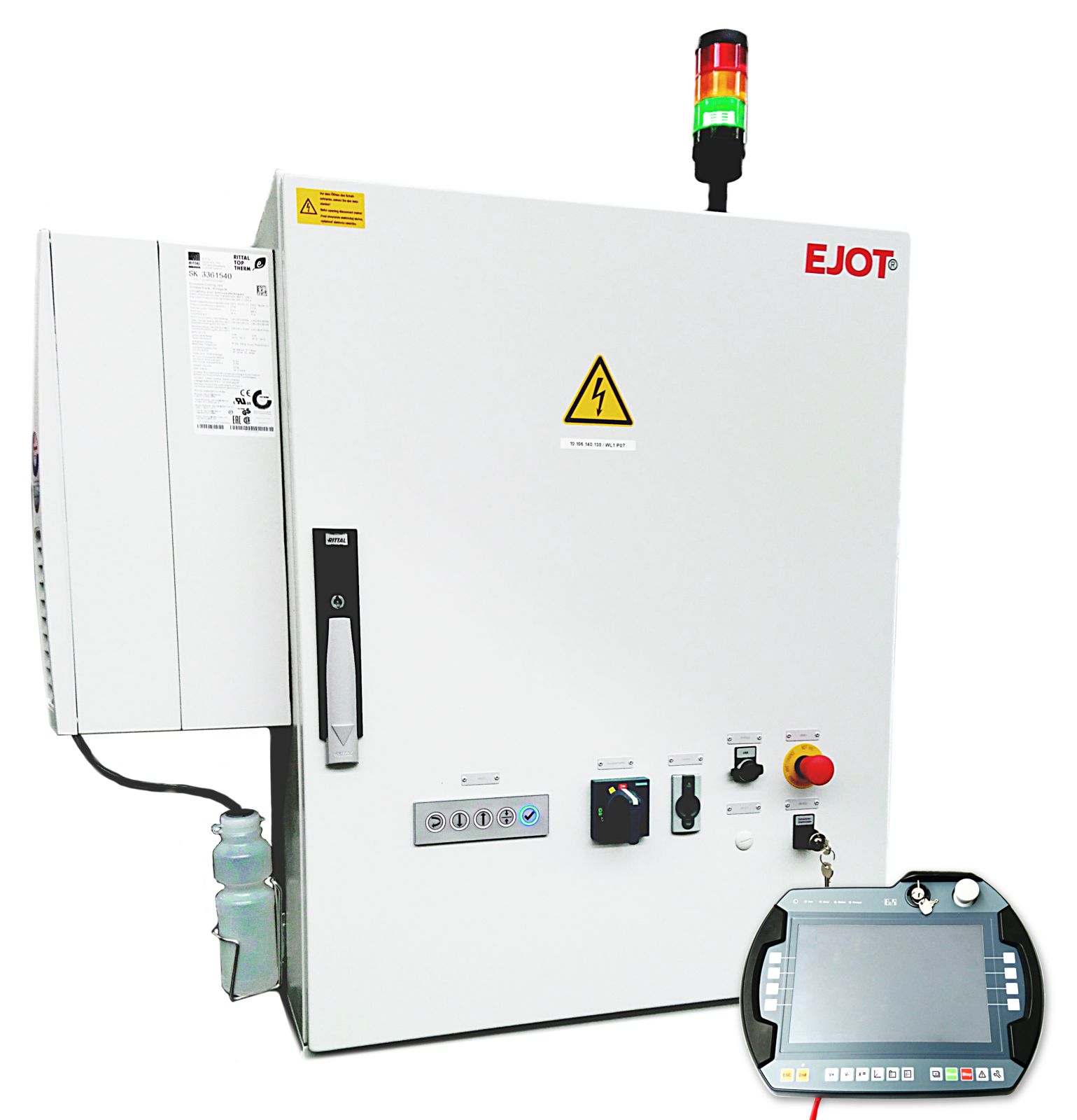
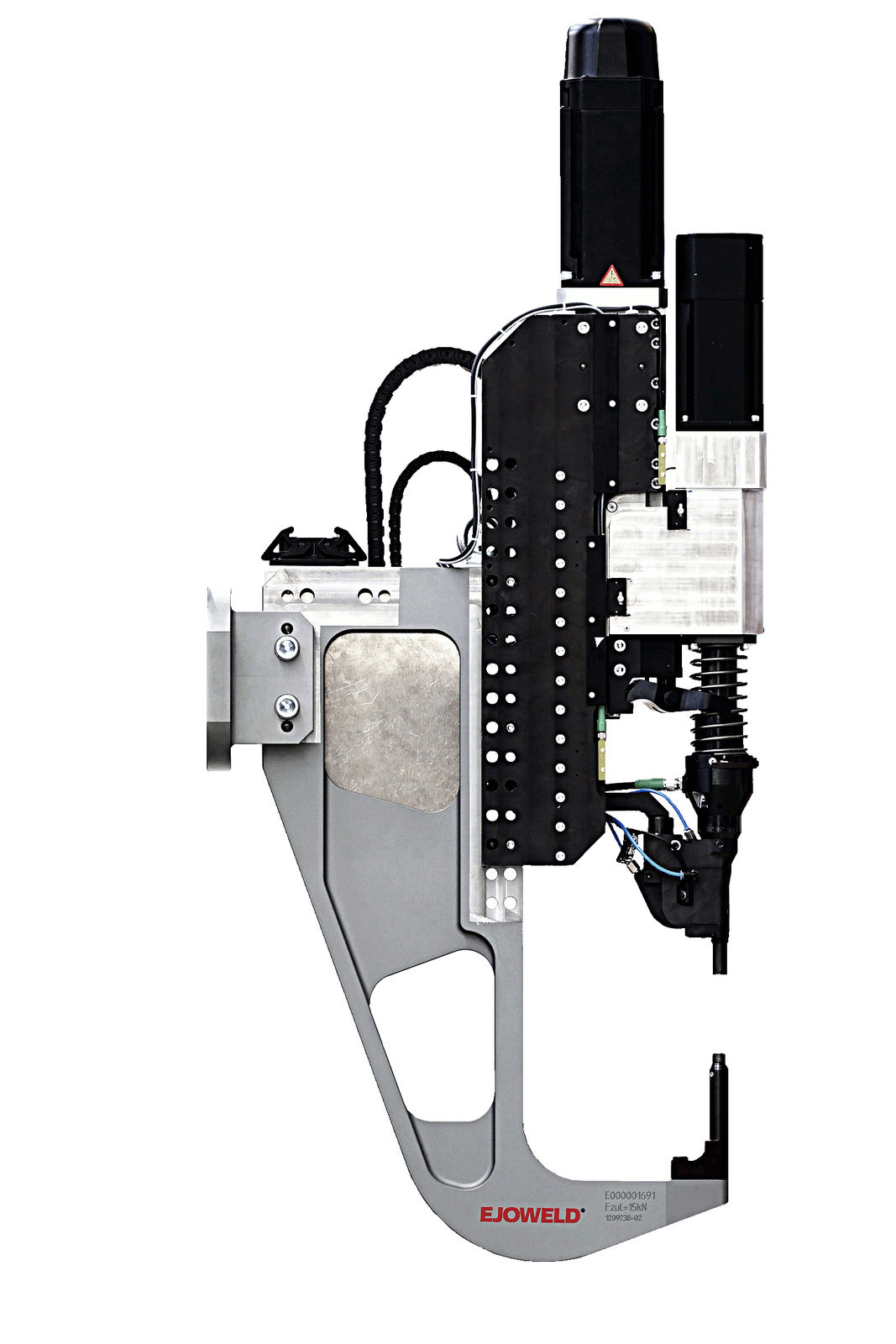
El hardware modular e interoperable garantiza la flexibilidad
Cuanto mayores son las diferencias en los materiales a unir, más flexible debe ser el sistema de automatización para adaptarse a las diferentes necesidades. "Con B&R, tenemos un socio cuyos productos nos permiten implementar perfectamente estas adaptaciones sin problemas de compatibilidad", comenta Heiland. Las diferentes interfaces de hardware y software necesarias para la integración con el robot y otros equipos de producción son características estándar de la gama de productos de B&R.
Gracias a la tecnología de seguridad integrada de B&R, también puede aplicarse el mismo nivel de adaptabilidad para la solución de seguridad. Por último, pero no menos importante, la completa interoperabilidad del PLC X20 de B&R y el Automation PC permite a EJOT adaptar a medida la solución según sea necesario, sin necesidad de realizar ajustes en la aplicación del software. "Podemos actualizar fácilmente a un potente PC industrial para poder realizar un control avanzado de procesos", comenta el jefe de ventas, avanzando en cierta forma los planes de desarrollo futuros. Otro objetivo es optimizar aún más el diseño de la herramienta de ajuste con unos motores aún más compactos.
De esta forma, EJOT realiza una importante contribución al uso de materiales ligeros que consiguen que la fabricación de automóviles sea más respetuosa con el medio ambiente.
![]() | Robert Heiland Ingeniero de sistemas de EJOWELD, EJOT "Desarrollar toda una nueva generación de sistemas es una decisión trascendental. La elección de un socio con un concepto tan bien pensado y un servicio integral nos ayudó a convertir nuestra visión en realidad y ofrecer una solución bien equipada para podernos enfrentar a los nuevos requisitos que el futuro nos depare". |