It may have taken a while, but condition monitoring has made its way to the wind power industry. This is owed in no small part to contributions from experts like Bernd Höring, co-founder of 8.2 Monitoring GmbH. As a member of the influential 8.2 Group, his company specializes in condition assessment of wind turbine drivetrain components, monitoring of photovoltaic systems and development of related software tools. Condition monitoring increases the reliability of wind and solar power systems, prevents costly and dangerous failures – and ultimately makes them both safer and more profitable. But how does it do that?

Bernd, can you begin by telling us about the 8.2 Group and what it does?
Since it was founded in 1995, the 8.2 Group has grown into a network of 30 engineering offices all around the world, the majority of them in Germany. With a total of around 50 employees, our location here in Hamburg is the largest. We primarily deal with onshore and offshore wind farms, although over time our focus has widened to include all types of renewable energy. Today we're also strong in photovoltaics, biomass and grid integration. As experts in the field, we provide services ranging from technical inspections and damage analysis to online condition monitoring. We also offer a variety of consulting services. Essentially, 8.2 covers the entire renewable energy value chain.
The cooperation between 8.2 and B&R goes back a number of years. What was it that led you to B&R?
When we started working with B&R in 2013, it was important to us that we find a partner where the chemistry is right. To me, that means building the relationship on openness and honesty. When you have that – like we do with B&R – working together is a pleasure. Equally important, the level of quality is on par with our demanding requirements. B&R has developed condition monitoring hardware that fits perfectly into our portfolio, while our services and analytical software complement B&R's portfolio.
Can you give us some background on how you came to co-found 8.2 Monitoring and your current role in the company?
Until 2002, wind turbines were plagued by unexpected failures – particularly in the gear teeth and bearings of their gearboxes and generators. This was partially due to a tendency to underestimate the highly dynamic loads and severe operating conditions, as well as the fact that they were only equipped with fairly rudimentary control instrumentation. With such high failure rates, insurance companies viewed turbines as a poor investment and were threatening to get out of the wind power business rather than operate at a loss. To get a handle on the situation, wind power companies leveraged existing condition monitoring expertise from industrial applications. In 2003, the Allianz Center for Technology (AZT) – followed shortly thereafter by Germanischer Lloyd (GL) – published guidelines for the certification of condition monitoring systems (CMS). These systems allowed for early detection of wear so that components can be replaced before they cause more serious equipment failure. As a result, rather than €150,000 in repairs, a company might only be looking at €10,000.
Why is condition monitoring so important for wind turbines?
Until 2002, wind turbines were plagued by unexpected failures – particularly in the gear teeth and bearings of their gearboxes and generators. This was partially due to a tendency to underestimate the highly dynamic loads and severe operating conditions, as well as the fact that they were only equipped with fairly rudimentary control instrumentation. With such high failure rates, insurance companies viewed turbines as a poor investment and were threatening to get out of the wind power business rather than operate at a loss. To get a handle on the situation, wind power companies leveraged existing condition monitoring expertise from industrial applications. In 2003, the Allianz Center for Technology (AZT) – followed shortly thereafter by Germanischer Lloyd (GL) – published guidelines for the certification of condition monitoring systems (CMS). These systems allowed for early detection of wear so that components can be replaced before they cause more serious equipment failure. As a result, rather than €150,000 in repairs, a company might only be looking at €10,000.
What are the potential downsides to using a CMS?
There aren't any. I do know a few farmers who operate turbines, and their well-trained ears prick up immediately when something isn't running smoothly.Wear and tear is generally accompanied by vibrations and noise, after all. That's the exception though. These days, the operator is normally sitting in front of a computer screen at a big monitoring center and has only process data to go by – so simply listening for damage is not an option. Here, it's the CMS that gives you an ear on the machine.
Where is the market headed with regard to condition monitoring?
We're currently working primarily with standard CMS applications that operate independently of the turbine controller. This is going to shift in favor of integrated systems now that the necessary automation hardware is available. By incorporating additional process parameters and system-level monitoring, these solutions will deliver better results. Controller-integrated systems will likely also be able to meet the same quality standards for cheaper. Industry 4.0-related topics such as cloud computing, digitalization and big data are also important. As requirements for availability and yield stability grow more rigorous, the market for condition monitoring will benefit. In Germany, offshore wind farms are already required to be equipped with a CMS. Even onshore, as turbines are built larger and larger, the consequences of a failure become more serious. That's why almost all wind turbine builders are including a CMS as standard equipment on systems larger than 2.5 megawatts. The international market – in China, for example – is growing as well. This will in turn ramp up the pressure on manufacturers to minimize lifecycle costs and eliminate risk factors. Paired with the corresponding independent analysis service, a CMS can play a key role in meeting these challenges.
Many companies approach topics like cloud computing with hesitation, worried that they may pose a security risk. Where do you stand?
It's certainly an area we're looking at. Our own server is located here in Hamburg because performance is a top priority for us – but our capacity is not unlimited. Far from being a liability, I think a cloud solution is actually the more secure option. Often it's the in-house server that represents a greater risk in terms of data loss. In my opinion, the level of data security you get from a larger cloud computing service provider is going to be more advanced and kept up to date better than what a smaller company is able to manage on its own. Cloud performance is also constantly improving.
Is wind power going to develop into a mass market for condition monitoring? What's your prediction?
For well-established CMS companies it already is a mass market – every turbine manufacturer has a CMS supplier. Industrial applications are still the bread and butter for the majority of CMS suppliers, however. They've been there for decades and have plenty of satisfied customers. It really depends on how well controls suppliers like B&R are able to gain a foothold in the wind sector. If they are successful, the cost of CMS hardware will drop and it will become a standard component of turbine automation systems. The advantage that automation providers have is that, since they operate all the interfaces, they're in a position to meet the requirements of customers who want to make information available to other software systems. It will be another five to ten years before we see that happen, however. With all its technical advantages and new developments, we mustn't forget that condition monitoring is still an area where the experienced analyst plays an important role.
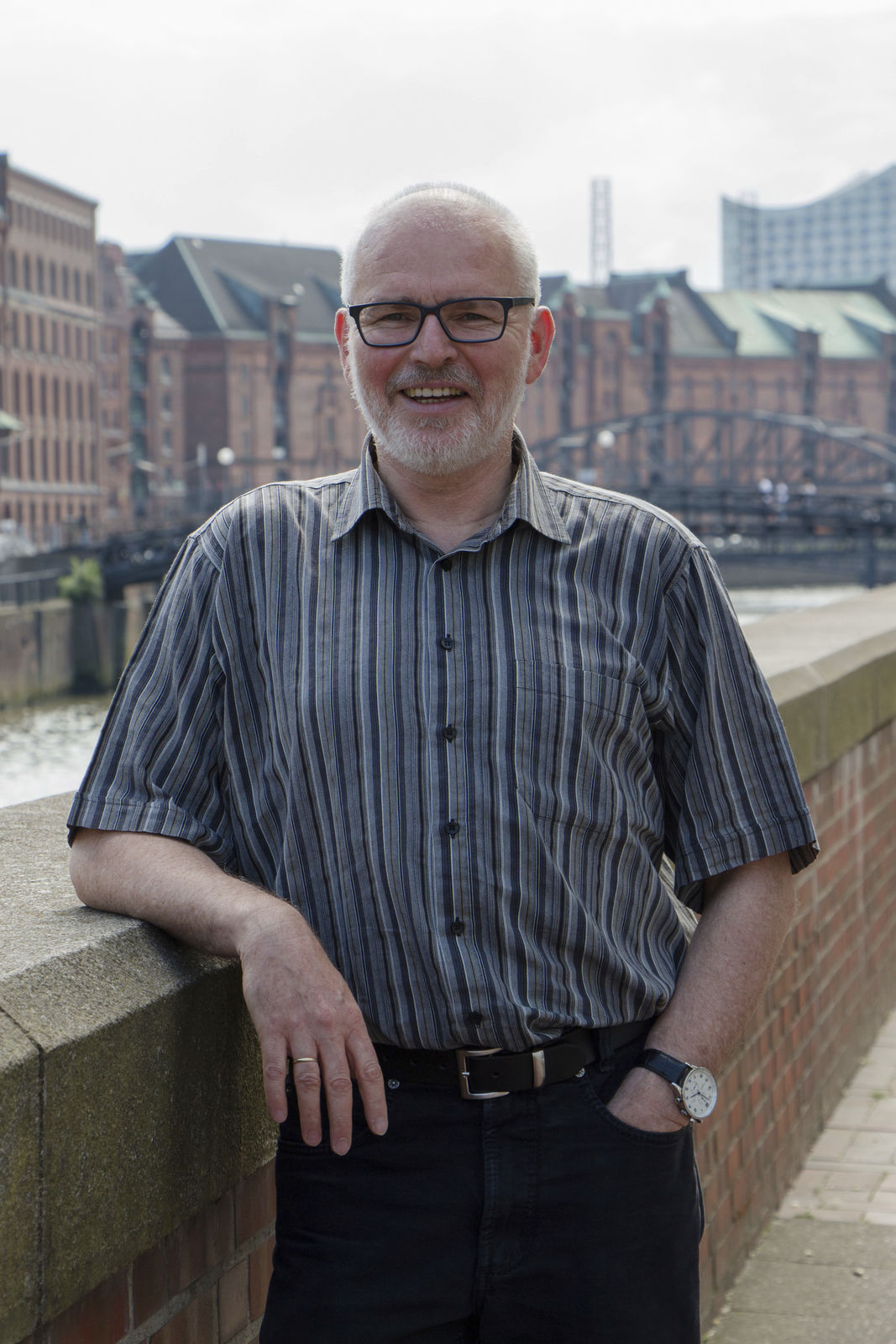
Bernd Höring, CEO and Condition Monitoring Expert, 8.2 Monitoring GmbH
"It was important to us that we find a partner where the chemistry is right. That means building relationships on openness and honesty. Our quality standards are as demanding as our technical specifications. That's why we needed a well-established supplier like B&R who can meet these requirements all around the world." (Source: Alexandra Fabitsch)
What is condition monitoring?
Dynamic loads and severe weather take their toll on a turbine's drivetrain. If worn bearings, gearboxes or generators are not replaced in time, the result can be catastrophic failure and costly extended downtime. To keep things running smoothly for maximum availability and yield, turbines are equipped with condition monitoring systems (CMS) that provide a continuous stream of information about component health based on the vibrations caused by worn components.
How does condition monitoring work at B&R?
B&R's easily configurable condition monitoring modules provide reliable and precise wear detection for efficient predictive maintenance. All of these modules are part of the X20 control system series and can therefore be used in any control topology with no limitations. A special feature of these modules is that they perform vibration analysis locally on the module – providing fully processed condition parameters for easy integration. In combination with analysis software like VibraLyzePRO from 8.2, they allow effective online monitoring of complex systems. These results also provide detailed insight into the system mechanics, allowing existing processes to be optimized with maximum efficiency.