Maschinenbauer und Anlagenbetreiber haben ein großes Ziel: flexible und digitale Produktionen. Um diesem Ziel näher zu kommen, ist die Industrie auf Forschungseinrichtungen wie die Technische Universität in Graz (Österreich) angewiesen. In der Smart Factory der renommierten Universität dreht sich alles um agile und datensichere Fertigungskonzepte. Projektleiter Rudolf Pichler erzählt im Interview welchen Beitrag die Smart Factory zur Umsetzung der intelligenten Fabrik leistet und welchen Nutzen Industriebetriebe aus der Lern- und Forschungsfabrik ziehen können.
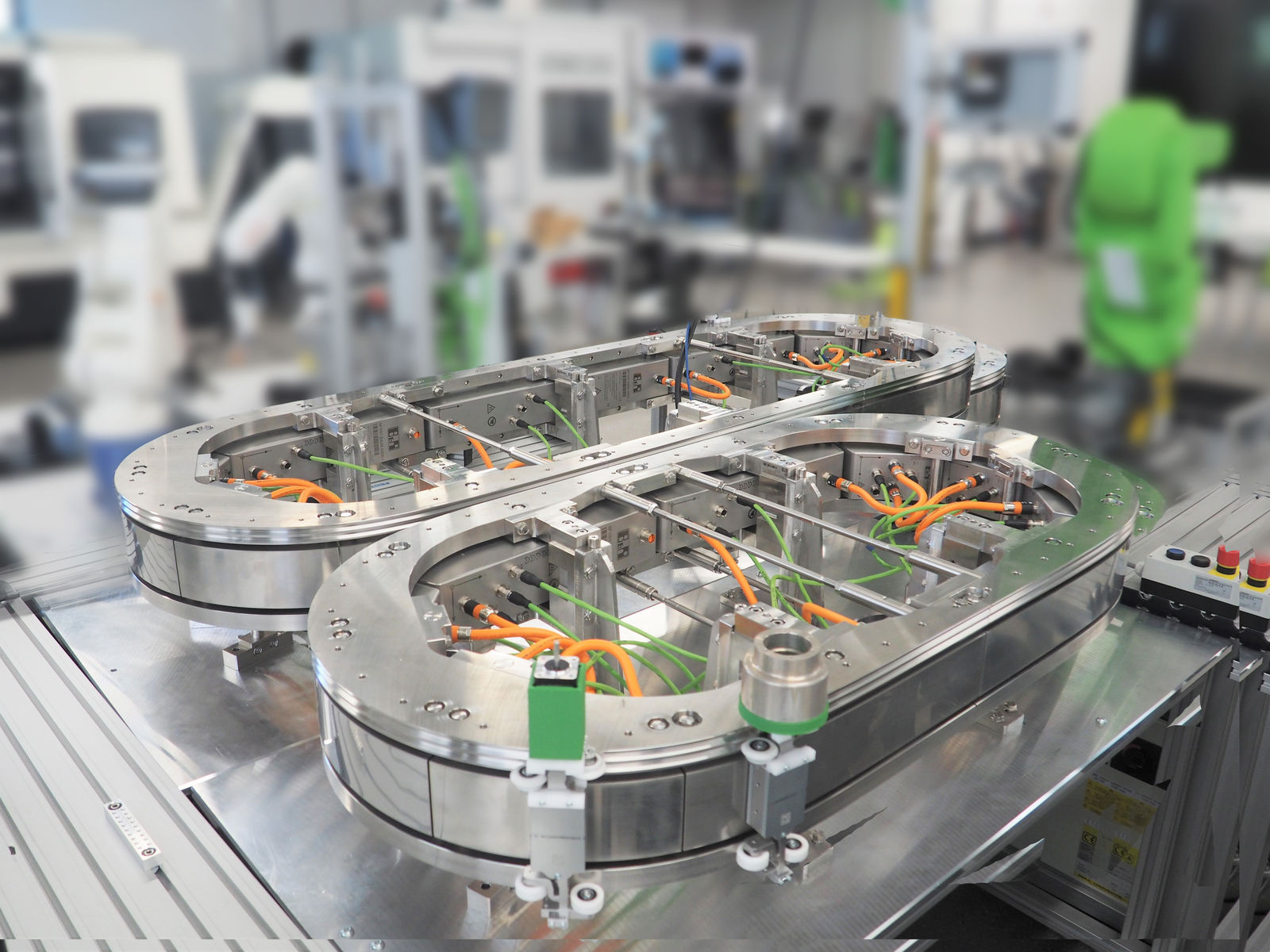
Herr Pichler, im April 2021 wurde die Smart Factory offiziell eröffnet. Welche Möglichkeiten bietet die Lern- und Forschungsfabrik für die Industrie?
Rudolf Pichler: Kurz zusammengefasst verbindet die Smart Factory modernste Anlagen der mechanischen Fertigung und Montage mit fortschrittlichen Produkten der Informationstechnologie. Das heißt, wir erproben neuartige Lösungskonzepte für die Industrie 4.0 in einer realen Fabrikumgebung. Unser Schwerpunkt liegt dabei auf Agilität und Datensicherheit. Darüber hinaus bieten wir unsere Smart Factory auch als eine Art Labor für Unternehmen an. Firmen können zu uns kommen und die Lernfabrik für ihre eigene Forschung an disruptiven Technologien für die industrielle Fertigung nutzen.
Das heißt, die Smart Factory funktioniert im Grunde wie ein Industriebetrieb?
Pichler: Ja, genau. Wir haben eine durchgängige Wertschöpfungskette und stellen ein mehrteiliges industrielles Produkt her. Nach der Fertigung wird unser Produkt zu verschiedenen Stationen transportiert, zum Beispiel zum Waschen, Vermessen oder Montieren. Auch einen Prüfstand haben wir integriert. Das Entscheidende dabei ist aber, dass wir die unterschiedlichen Prozessstationen möglichst flexibel miteinander verbunden haben und der gesamte Herstellungsprozess smart gestaltet ist. Wir zeigen unter anderem, wie Roboter, Automaten und CNC-Maschinen miteinander vernetzt sind und so optimal zusammenarbeiten.
![]() | Rudolf Pichler Projektleiter Smart Factory, Technische Universität Graz „Mit ACOPOStrak von B&R konnten wir für den Produkttransport den kürzesten Weg wählen und den Footprint der gesamten Anlage massiv verringern." |
Und wie haben Sie das geschafft?
Pichler: Wie schon erwähnt, liegt unser Fokus sehr stark auf Agilität. Also waren wir auf der Suche nach einer flexiblen Lösung für unsere Prozesse. Schließlich haben wir uns dafür entschieden, sämtliche Anwendungen und Maschinen auf mobilen Arbeitsstationen zu installieren. So eine Station ist zum Beispiel eine pneumatische elektrische Presse oder ein Roboter. Wichtig war uns dabei, dass die Stationen alle autark und so energetisch unabhängig sind. Alle Maschinen sind miteinander vernetzt, egal von welchem Hersteller sie stammen. Schließlich mussten wir noch eine Lösung finden, um die Arbeitsstationen miteinander zu verbinden und das Produkt von einer Station zur nächsten zu transportieren.
Welche Lösung haben Sie dafür gefunden?
Pichler: Einer unserer insgesamt 20 Partnerbetriebe aus der Industrie, B&R, hat uns hierfür einen äußerst spannenden Vorschlag gemacht: das flexible und intelligente Track-System ACOPOStrak.

Interessant. Was unterscheidet das Track-System von herkömmlichen Lösungen?
Pichler: Mit ACOPOStrak werden ganze Produkte oder auch nur Produktbestandteile auf einzelnen Shuttles schnell und flexibel durch eine Anlage oder durch die ganze Produktion bewegt. Damit war grundsätzlich unsere Intralogistik gesichert. Aber ACOPOStrak bietet noch viele weitere Vorteile für eine moderne Fertigung, die den Marktanforderungen nach kleinen Losgrößen und hoher Flexibilität gerecht werden muss.
Welche Vorteile sind das genau?
Pichler: Mit ACOPOStrak hat man zum Beispiel absolute Freiheit bei der Gestaltung der Anlage. Es gibt verschiedene Segmente und Kurven, die sich individuell zusammenstellen lassen. So konnten wir für den Produkttransport den kürzesten Weg wählen und den Footprint der gesamten Anlage massiv verringern. Auch die Produktivität lässt sich mit dem Track-System von B&R deutlich erhöhen, weil sich durch eine spezielle Hochgeschwindigkeitsweiche Produktströme teilen und wieder zusammenführen lassen. Generell ist der ACOPOStrak extrem flexibel und kann innerhalb sehr kurzer Zeit auf ein neues Produkt angepasst werden. Das war für uns wichtig, da wir so die Arbeitsstationen jederzeit für ein neues Produkt schnell und unkompliziert neu anordnen und mit dem Track verbinden können.
Sind auch noch andere B&R-Produkte in der Smart Factory integriert?
Pichler: Wir nutzen auch das Vision-System von B&R sowie das zugehörige Ringlicht und natürlich B&R-Steuerungen, zum Beispiel für unseren Getriebeprüfstand. Eine unserer Laborübungen beschäftigt sich mit dem Thema Retrofit. Auch hier setzen wir auf Hard- und Software von B&R. Für die Integration der Sensorik von älteren Maschinen in unser Gesamtsystem ist das B&R-System nämlich optimal. Wichtig ist auch, dass B&R das herstellerunabhängige Kommunikationsprotokoll OPC UA einsetzt. So können wir Produkte unterschiedlicher Hersteller einfach miteinander verbinden.
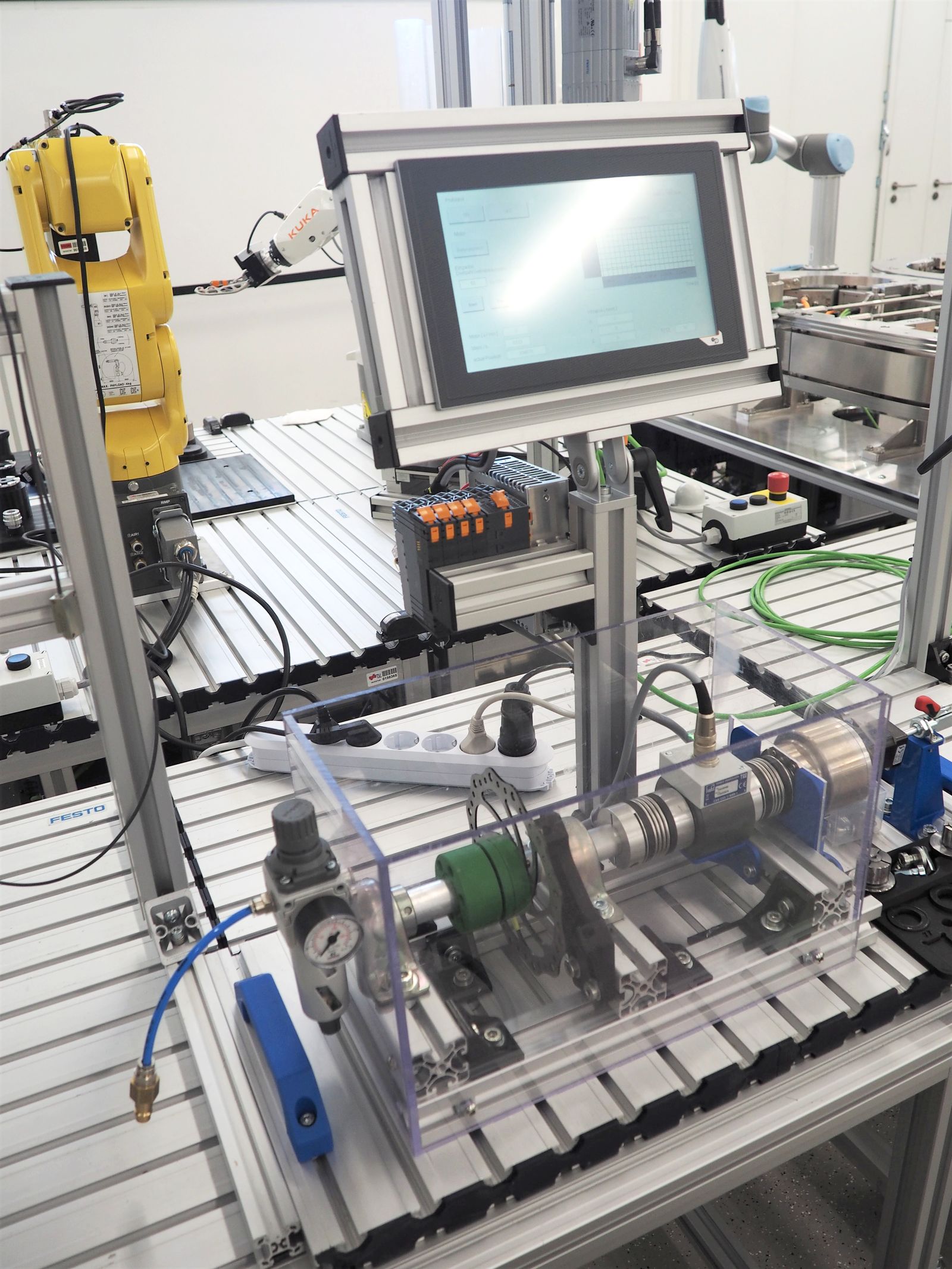
Die Lern- und Forschungsfabrik wurde nun über mehrere Jahre entwickelt. Was waren die größten Herausforderungen dabei?
Pichler: Die Herausforderungen waren tatsächlich vielfältig. Zuallererst war es wichtig, ein Konzept zu finden, das einzigartig ist. Lernfabriken gibt es bereits einige und wir wollten uns abheben und aus der Masse herausstechen. Deshalb haben wir uns für die Themen Agilität und Datensicherheit als Grundpfeiler entschieden. Eine weitere Herausforderung war die Finanzierung der Smart Factory. Vor allem Industriepartner zu finden, die in das Projekt investieren möchten – schließlich geht es dabei um sehr große Summen.
Welche Aufgaben gestalteten sich noch schwierig?
Pichler: Nachdem wir Konzept und Finanzierung auf die Beine gestellt hatten, war es wichtig, qualifizierte Mitarbeiter zu finden, die bei diesem innovativen Vorhaben mitwirken wollen. Das ist auch für Universitäten immer ein schwieriges Unterfangen, aber es ist uns letztlich sehr gut gelungen. Darüber hinaus hatten wir sehr viele Ideen, was wir alles in der Smart Factory umsetzen möchten. Die Herausforderung bestand darin, ein sinnvolles Ganzes, also eine durchgängige Produktionskette zu schaffen. Um Digitalisierung zu zeigen, war es notwendig, die einzelnen Aggregate informatorisch zu vernetzen. Dafür benötigten wir eine Vielfalt an Anlagen, die nicht immer dieselbe Sprache sprechen. Mit unseren Industriepartnern konnten wir diese Herausforderung aber in aufwendiger Arbeit gut meistern.
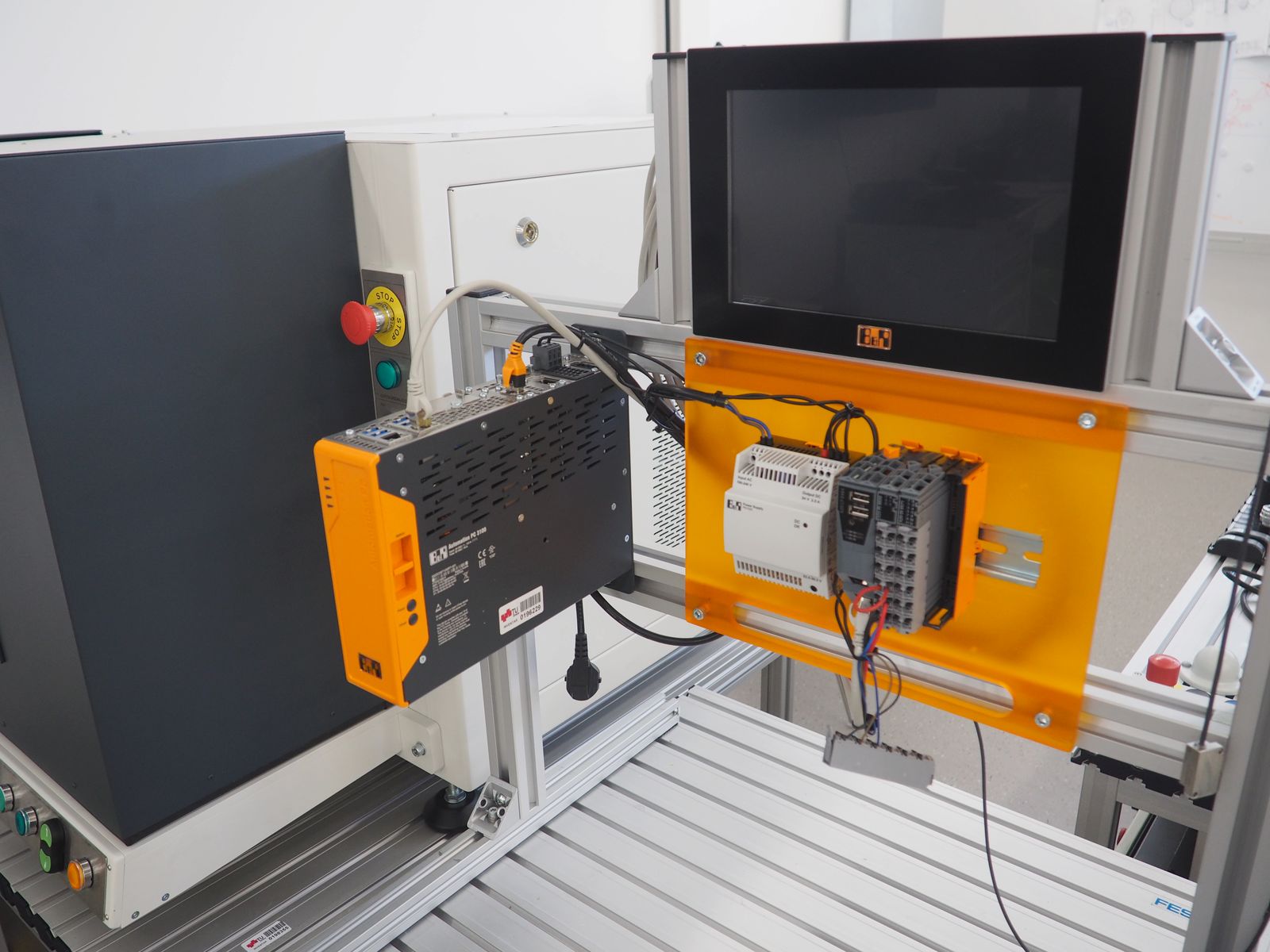
Was wünschen Sie sich für die Zukunft der Smart Factory? Gibt es schon konkrete Pläne, welche Technologien bald dort einziehen dürfen?
Pichler: Unsere Lern- und Forschungsfabrik lebt von Innovationen und wird sich ständig weiterentwickeln. Die wesentlichen und immer wiederkehrenden Themen der Smart Factory bleiben aber Agilität und Konnektivität. Das wird sich in Zukunft auch noch verstärken. Mir war es von Anfang an sehr wichtig, dass wir eine gute Mischung von Komponenten unterschiedlicher Hersteller in unserer Lernfabrik haben. Schließlich ist eine große Fabrik in der realen Welt auch nicht nur mit B&R-Produkten ausgestattet. Für die Zukunft wünsche ich mir auf alle Fälle, dass möglichst viele Industriebetriebe zu uns kommen und die Infrastruktur in der Smart Factory nutzen, um zukunftsorientierte Konzepte bei und mit uns zu entwickeln.
Vielen Dank für das Gespräch.
Smart Factory – Lernfabrik für agile und datensichere Fertigung
Die auf 300 m² aufgebaute realitätsnahe diskrete Fertigung umfasst alle Wertschöpfungsstufen vom Engineering bis zur Endmontage und zeigt die Vernetzung von Einzelaggregaten, die Verknüpfung von IT und OT und die Vorzüge einer digitalisierten Fertigung anhand einer modernen, IT-gestützten Losgröße-1-Fertigung und modernstem Daten-Management. Die Smart Factory ist sowohl Zentrum für Wissensvermittlung als auch Testumgebung für interessierte Industriebetriebe.