Beim Gedanken an eine digitale Fabrik entsteht schnell das Bild von menschenleeren Fabrikhallen. Einzig vollautomatisierte Maschinen mit künstlicher Intelligenz bewerkstelligen die Produktion. Fantasie und Realität driften hier allerdings stark auseinander. Moderne Fertigungen im Sinne von Industrie 4.0 sind zwar digital und vernetzt, sie kommen aber keinesfalls ohne Menschen aus.

Industrie 4.0 steht für die Vernetzung der gesamten Wertschöpfungskette in einem Unternehmen. Das heißt: Sie vernetzt Maschinen, Produkte, Systeme und Menschen, sodass weitgehend automatisierte Prozesse möglich sind. Mensch und Maschine arbeiten Hand in Hand. Damit diese Zusammenarbeit funktioniert und zugleich effizient und wirtschaftlich ist, müssen beide Seiten ideal aufeinander abgestimmt sein. Zum einen soll die vernetzte Wertschöpfungskette die Produktivität steigern, zum anderen aber auch den Mitarbeiter in seinen Tätigkeiten unterstützen und ihn entlasten. Automatisierte Prozesse und Maschinen können zum Beispiel monotone Arbeiten übernehmen. Der Mitarbeiter kann sich neuen und anspruchsvolleren Tätigkeiten widmen und so sein Potenzial voll ausschöpfen.
Komplett vernetzt
Beim Automatisierungsspezialist B&R im österreichischen Eggelsberg wird Industrie 4.0 bereits seit mehr als zehn Jahren gelebt und die Mitarbeiterzahl steigt stetig an. Die smarte Fabrik mit rund 40.000m² Produktionsfläche ist horizontal und vertikal komplett vernetzt. Möglich macht dies ein ERP-System, das die Abarbeitung der Produktionsaufträge plant und eine reibungslose Logistik sicherstellt.
Arbeitsplatz der Zukunft
Um die Mitarbeiter in der B&R-Fertigung in Zukunft noch besser zu unterstützen und ihre Zusammenarbeit mit Maschinen zu verbessern, arbeitet B&R gemeinsam mit der Fachhochschule Oberösterreich am Projekt Human Centered Workplace for Industry, dem Arbeitsplatz der Zukunft. Die FH analysiert dafür aktuelle Arbeitsumgebungen und baut dann im Labor einen Prototyp des Arbeitsplatzes der Zukunft auf. So kann zum Beispiel getestet werden, wie sich Arbeitsplätze durch neue Geräte wie Augmented-Reality-Brillen aufwerten lassen.
Digitalisierung ermöglicht Abwechslung
Aktuell hat B&R bereits zahlreiche Assistenzsysteme im Einsatz. Besonders in der Fertigung von Industrie-PCs sind diese notwendig, um zum einen die Mitarbeiter flexibel einzuteilen und ihnen eine abwechslungsreiche Tätigkeit zu bieten und zum anderen, um eine einwandfreie Produktqualität zu gewährleisten. „Unsere PC-Fertigung zeigt die Vorteile der digitalen Fabrik sehr gut auf. Die B&R-Mitarbeiter können nach kurzer Einschulung auf den spezifischen Arbeitsplatz, jeden PC zusammenbauen und das bei bis zu 250 Milliarden unterschiedlicher Konfigurationsmöglichkeiten“, sagt Robert Perperschlager, Produktionsleiter und Mitglied der Geschäftsführung bei B&R. Am Arbeitsplatz der Zukunft der FH testet B&R nun weitere Möglichkeiten für assistierende Systeme auf ihre Praxistauglichkeit. „Insbesondere beim Handling von komplexen Teilen spielen auch zunehmend kollaborative Roboter eine Rolle, welche den Mitarbeiter sozusagen als dritte Hand direkt unterstützen“, erklärt Perperschlager.
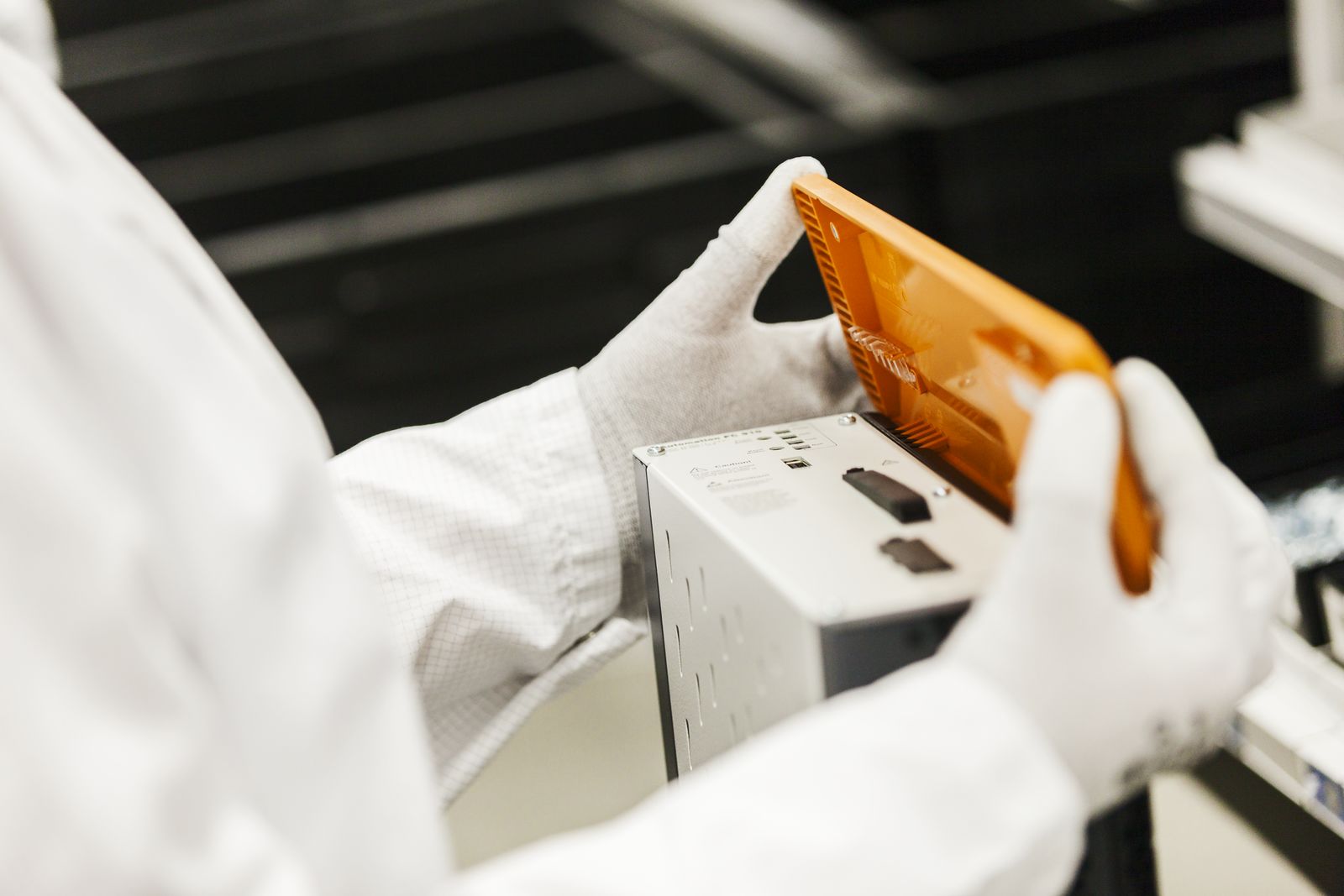
Digitale Anleitung für jeden Arbeitsschritt
Auch ein Ersatz für gängige Anzeigegeräte in Form von Projektionen direkt am Arbeitsplatz wird erprobt. Die Anzeigegeräte werden benötigt, um dem Mitarbeiter die Arbeitsanweisungen für die einzelnen Arbeitsschritte der Produktfertigung aufzuzeigen. „Die große Vielfalt unseres PC-Portfolios macht es zum Beispiel notwendig, unsere Mitarbeiter mit Arbeitsanweisungen zu unterstützen. Dabei handelt es sich um kurze Bildsequenzen, in denen präzise erklärt wird, wie der Arbeitsschritt auszuführen ist“, so Perperschlager.
Ist ein Arbeitsschritt abgeschlossen, muss dieser im System bestätigt werden. Um diesen Vorgang zukünftig intuitiver zu gestalten und ihn an die natürlichen Bewegungsabläufe des Mitarbeiters anzupassen, testet B&R den Einsatz von sogenannten Touchpoints. Die Touchpoints können an der Kleidung angebracht werden, zum Beispiel am Ärmel oder auf dem Handschuh. Mit einer simplen Berührung des Touchpoints bestätigt der Mitarbeiter den Arbeitsschritt. So werden Rückmeldungen an das System wesentlich vereinfacht und der Arbeitsprozess wird nicht mehr künstlich unterbrochen.
Arbeitserleichterung mit Smartwatch
Derzeit evaluiert B&R ein neues System, das Mitarbeiter der Instandhaltung sowie Störungstechniker in ihrer täglichen Arbeit unterstützt. „Droht zum Beispiel bei einer Produktionsmaschine in der Fertigung von B&R ein Ausfall, wird ein zuständiger Mitarbeiter sofort über seine smarte Armbanduhr informiert. Er kann schnell vor Ort sein und die Maschine überprüfen, egal wo er sich gerade am B&R-Firmengelände befindet“, erklärt Perperschlager. Das System erkennt drohende Maschinenausfälle, sendet diese Information weiter ans ERP-System, sucht in einer Datenbank einen für die Reparatur qualifizierten Mitarbeiter und zeigt ihm die Meldung auf dem Display der Smartwatch an. Der Griff zum Telefon wird überflüssig.
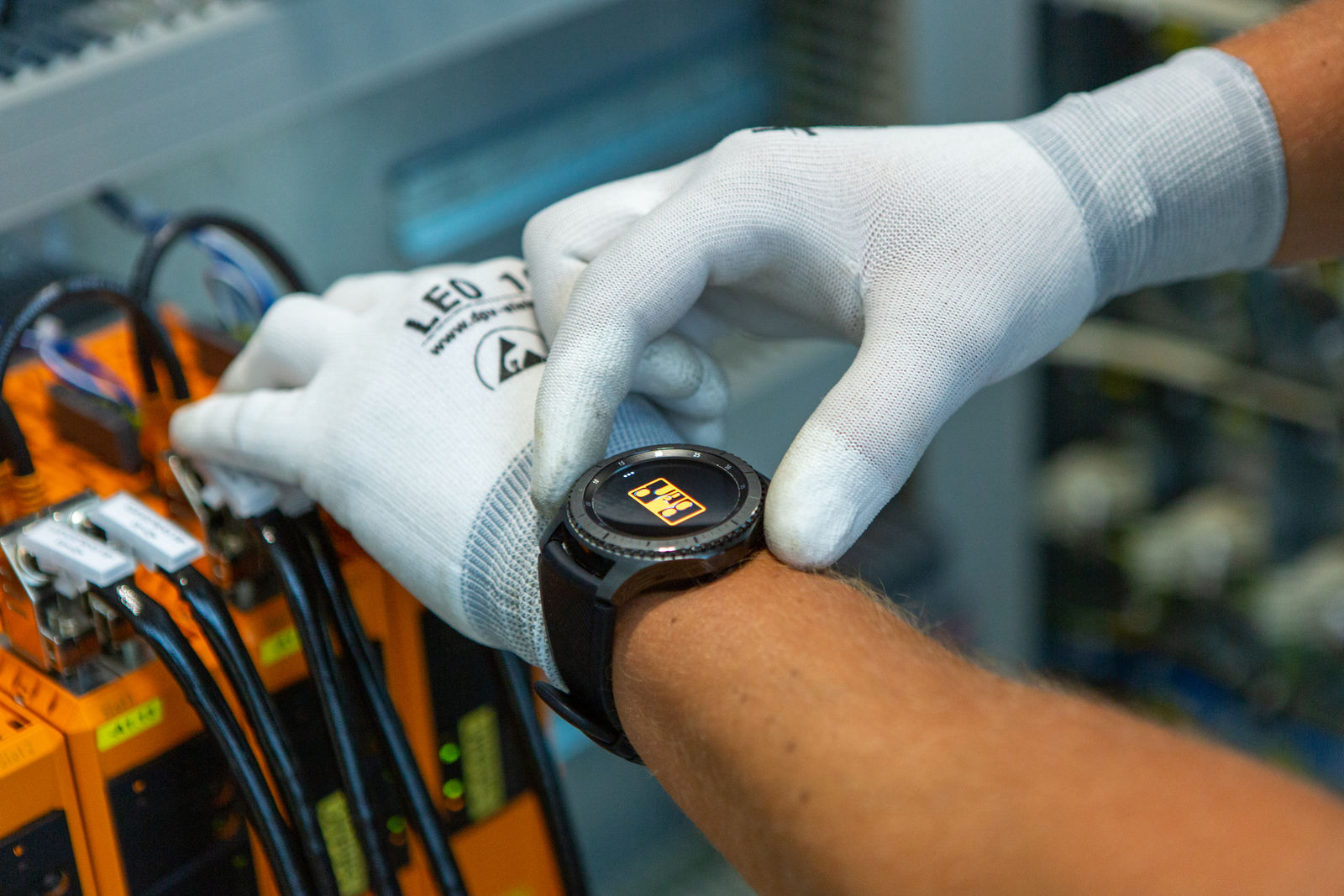
Das smarte Instandhaltungssystem priorisiert die eingehenden Meldungen nach Dringlichkeit. Bei einem drohenden Maschinenstillstand bekommt die Meldung zum Beispiel die höchste Priorität, bei einer Reparatur, die den laufenden Betrieb derzeit nicht beeinträchtigt, die niedrigste. Damit der Mitarbeiter sofort merkt, wie dringend die eingehende Meldung ist, vibriert die Smartwatch unterschiedlich stark. So erkennt er sofort, wenn ein Arbeitsauftrag mit höchster Priorität eingeht. Er kann seine aktuelle Aufgabe pausieren und sofort zum akuten Störfall eilen.
Arbeitssicherheit erhöhen
Darüber hinaus erhöht die Smartwatch die Arbeitssicherheit für Mitarbeiter der Instandhaltung. Durch die bisherige Kommunikation per Telefon, musste der Techniker seine Arbeit abrupt unterbrechen und Anrufe annehmen. Das heißt, klingelte das Telefon, brauchte er mindestens eine Hand dafür. „Durch den Einsatz der smarten Armbanduhr, behält der Mitarbeiter immer die Hand frei. Eine leichte Drehbewegung des Handgelenks genügt bereits um einen Blick auf das Display zu erhaschen“, sagt Perperschlager. Zudem wird die Nachricht so lange angezeigt, bis der Mitarbeiter bestätigt diese gesehen zu haben. Wichtige Arbeitsschritte bei einer Maschinenreparatur kann er somit abschließen, bevor er die Nachricht liest.
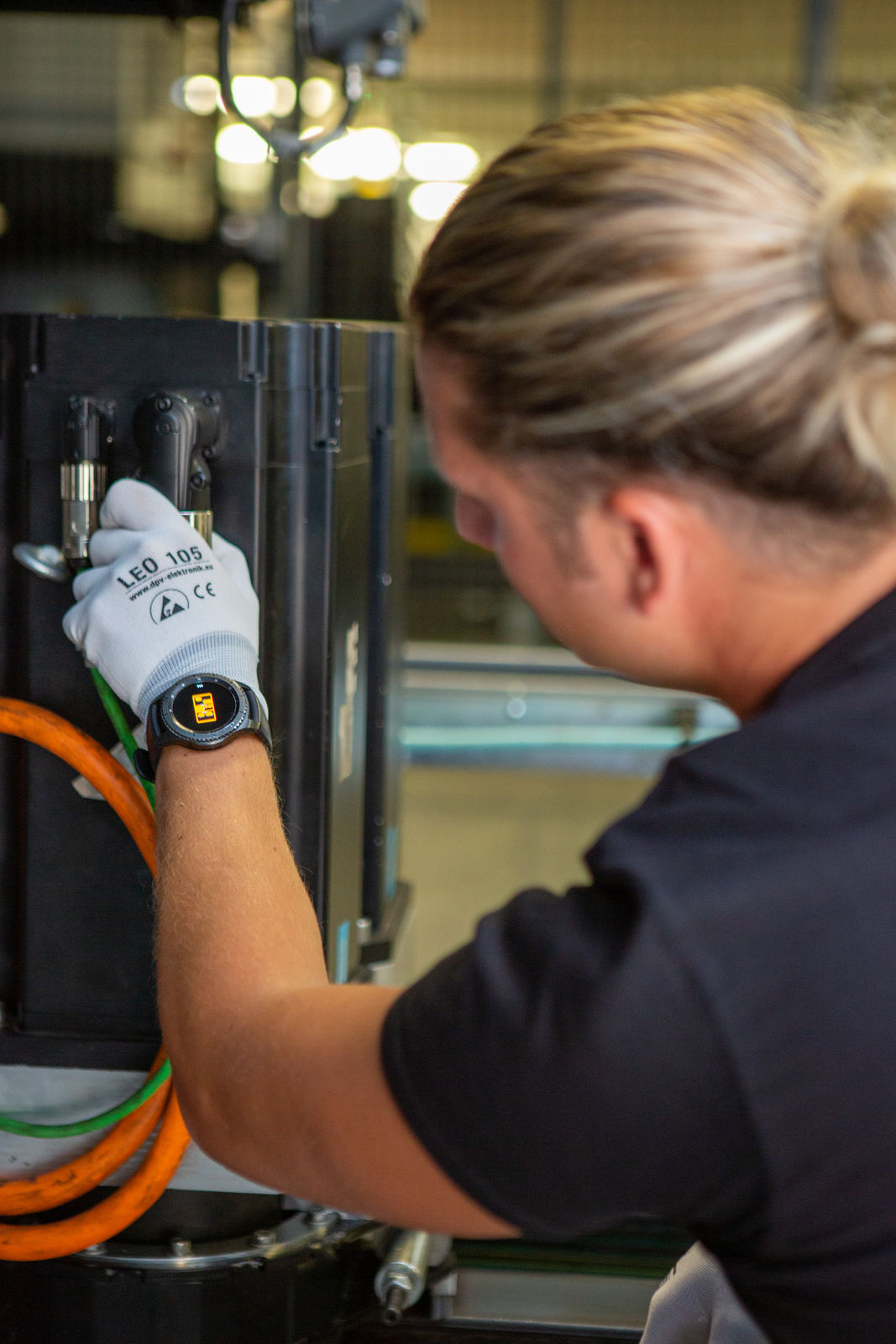
Mit dem Ausbau der Assistenzsysteme entwickelt B&R die digitale und vernetzte Fabrik stetig weiter und zeigt damit, dass der Mensch auch weiterhin Dreh- und Angelpunkt einer modernen Produktion bleibt. Intelligente Maschinen und Systeme unterstützen und entlasten den Mitarbeiter – ersetzen ihn aber keinesfalls.
Autor: Carola Schwankner, Unternehmensredakteurin bei B&R
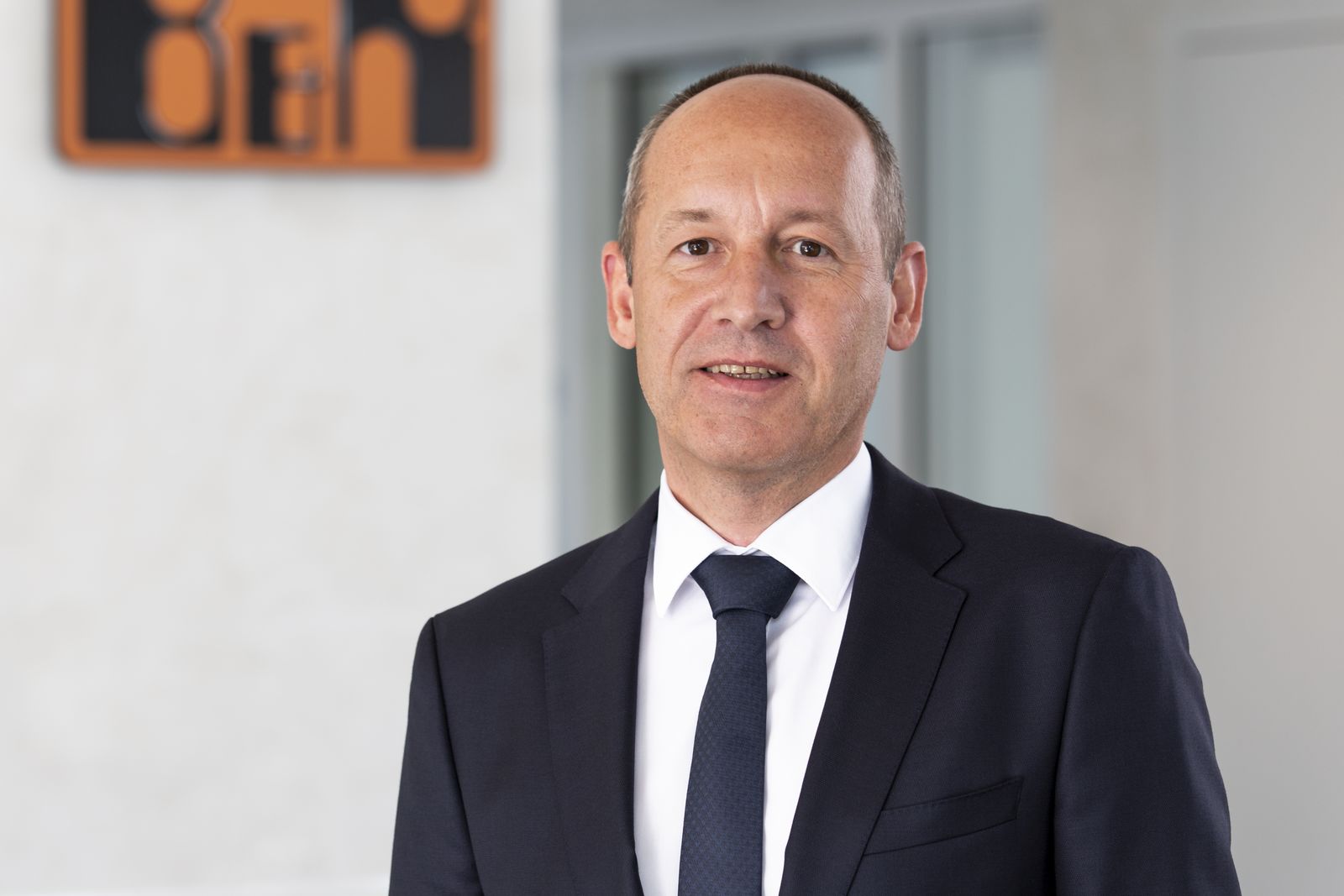