Die Visualisierung einer bestehenden Maschine auch nur geringfügig anzupassen, kann gravierende Auswirkungen haben. Ganze Anlagen stehen still, während der extra angereiste Software-Entwickler versucht, die Maschinen-Software wieder zum Laufen zu bringen. Um die explodierenden Kosten für Software-Wartung in den Griff zu bekommen, bieten sich modulare Software-Konzepte an. Wenn unterschiedliche Funktionen in der Software komplett voneinander getrennt sind, lässt sich der Wartungsaufwand beträchtlich senken.
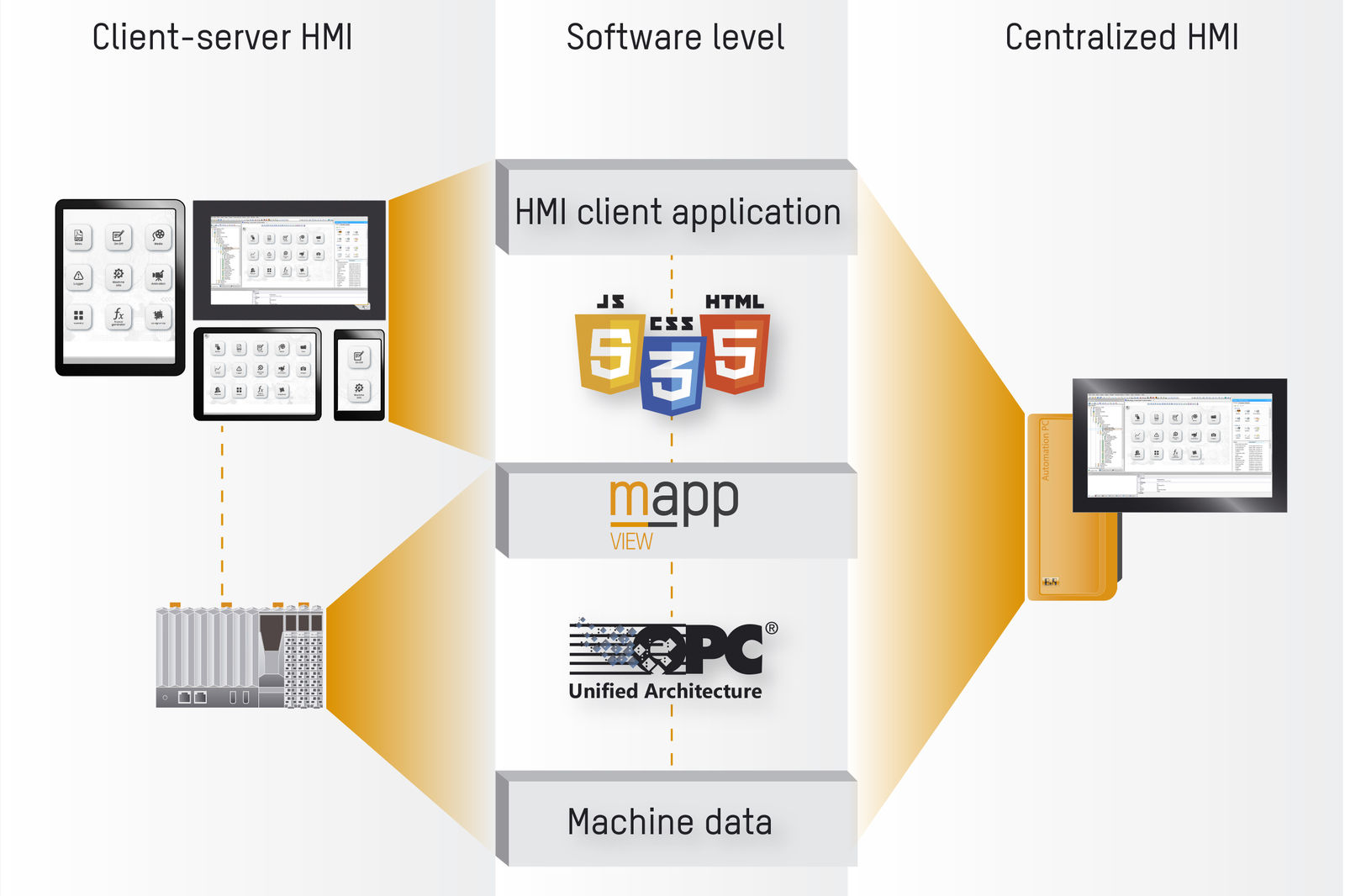
„Auf die Lebensdauer der Maschine gerechnet, übersteigen die Kosten für die Wartung der Maschinensoftware die Kosten für das ursprüngliche Software-Engineering erheblich“, erklärt Wolfgang Portugaller, Head of System Architects bei B&R. Neben den direkten Kosten – zum Beispiel für den Wartungstechniker – fallen weitere Kosten an. Die Maschine oder sogar die ganze Anlage stehen still und Wartungen können wiederum Quellen für neue Fehler sein. Um die Total Cost of Ownership (TCO) zu senken, sind Maschinenbauer darum bemüht, die Software-Wartung zu vereinfachen und kostengünstiger zu machen.
Moderne Software-Architektur
Moderne Software-Architekturen ermöglichen eine Entkopplung von Visualisierung und Maschinenapplikation: „Bisherige Visualisierungslösungen sind sehr eng mit der Maschinenapplikation verknüpft“, erklärt Portugaller. „Das heißt: Ändere ich etwas an der Maschinenapplikation, muss ich die Visualisierung mitändern. Gestalte ich die Visualisierung bedienerfreundlicher, muss ich gegebenenfalls auch die Applikation ändern.“
Soll zum Beispiel der Wert einer bestimmten Prozessvariable in der Visualisierung angezeigt werden, wird die Variable häufig direkt mit dem jeweiligen Visualisierungselement verknüpft. So lange die Maschine 20 Jahre lang unverändert läuft, ist diese Architektur kein Problem. „Doch die Realität sieht anders aus“, sagt Portugaller. Prozessvariablen ändern ihre Namen, Visualisierungsseiten werden angepasst oder ergänzt, neue Benutzer kommen hinzu. Selbst kleine Änderungen haben oft großen Programmieraufwand zur Folge.
Eine Lösung bietet das Software-Design-Prinzip „Seperation of Concerns“, bei dem unterschiedliche Funktionen vollständig voneinander getrennt werden. Übertragen auf eine Visualisierung bedeutet das, dass die Gestaltung der Visualisierungsseiten und die anzuzeigenden Daten voneinander getrennt werden.
Datenaustausch mit OPC UA
„Dieses Prinzip haben wir bei unserer neuen Visualisierungslösung mapp View konsequent umgesetzt“, sagt Portugaller. Um die Daten von der Maschinenapplikation auf die Visualisierung zu übertragen, setzt mapp View auf den unabhängigen Standard OPC UA. Soll eine Visualisierung zum Beispiel einen Temperaturwert anzeigen, fragt die Visualisierung nicht die Prozessvariable aus der Maschinenapplikation ab, sondern den Wert, den der OPC-UA-Server auf der Maschinensteuerung liefert.
Fehlerpotenzial sinkt
„Die Vorteile dieser Architektur treten besonders dann zutage, wenn Komponenten wiederverwendet, Maschinenvarianten gebildet oder Änderungen im Zuge von Wartungsarbeiten implementiert werden“, sagt Portugaller. Ändert sich zum Beispiel der Wertebereich einer Prozessvariablen, muss dies nur einmal im OPC-UA-Server angepasst werden – auch wenn der entsprechende Wert auf 10 unterschiedlichen Visualisierungsseiten verwendet wird. Damit sinkt das Fehlerpotenzial durch vergessene Änderungen oder Kopierfehler gegen Null.
Zudem hat OPC UA einen ganz großen Vorteil: Es überträgt nicht nur dimensionslose Daten, sondern reichert diese mit Kontextinformationen, sogenannten Metadaten, an. So wird bei einem Temperaturwert zum Beispiel nicht nur der numerische Wert übertragen, sondern auch die physikalische Einheit, in der der Wert zu interpretieren ist. Fehler bei der Einheitenumrechnung werden somit ausgeschlossen. Die Einheit kann mit einem Klick in der Visualisierung umgestellt werden, völlig unabhängig davon, mit welchen Einheiten die Maschinenapplikation arbeitet.
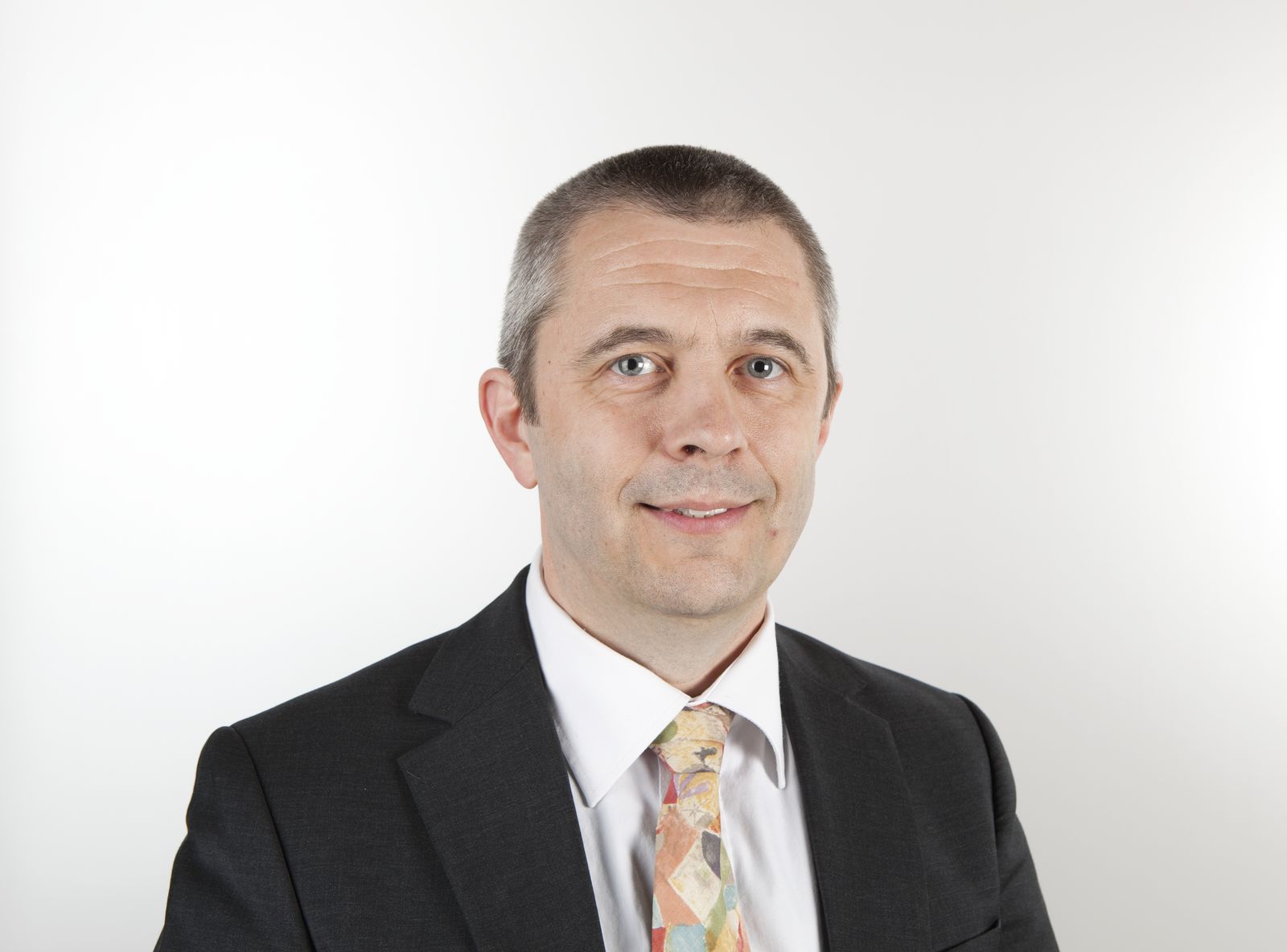
Sollwerte sicher ändern
Sehr hilfreich ist auch die Übertragung von Wertgrenzen. Die Visualisierung gibt dem Bediener sofort eine Rückmeldung, wenn ein eingegebener Sollwert außerhalb des zugelassenen Bereichs liegt. Eine Rückfrage in der Maschinenapplikation ist nicht notwendig. Wird im Zuge einer Wartungsmaßnahme zum Beispiel ein neues Kühlmittel in eine Maschine gefüllt, werden die Sollwerte in der Maschinenapplikation angepasst. Der OPC-UA-Server auf der Maschinen-Steuerung stellt diese geänderten Daten automatisch der Visualisierung zur Verfügung.
Zugriffe einfach regeln
„Beim Thema Sollwertänderung spielen auch Zugriffsrechte eine wichtige Rolle“, erklärt Portugaller. Die Information, welche Rolle, welche Änderungen an einem Wert vornehmen darf, wird mit den OPC-UA-Metadaten mitgeliefert. Mit dem B&R-Rollensystem lassen sich Rollen, Berechtigungsstufen und Nutzer ganz leicht anlegen und verwalten. „Während der Laufzeit können jederzeit neue Nutzer angelegt und einer Rolle zugewiesen werden. Das Rollensystem an sich muss dafür nicht angetastet werden.“
B&R hat mapp View auf der SPS IPC Drives 2015 erstmals der Öffentlichkeit vorgestellt. Die Visualisierungs-Lösung ist ab Version 4.2.5 LTS optionaler Bestandteil der Automatisierungs-Software Automation Studio. Pilotkunden setzen mapp View bereits seit rund einem Jahr ein, sodass nun die ersten Maschinen mit mapp View im Einsatz sind und gewartet werden. „Unsere Kunden sind begeistert, wie einfach die Software-Wartung mit mapp View ist“, sagt Portugaller. „Sie hätten nicht erwartet, dass die Architektur der Visualisierungs-Software so große Auswirkungen auf die Wartungsaufwände ganzer Maschinen und Anlagen hat.“
Autor: Stefan Hensel