Prüfaufgaben deutlich flexibler und effizienter gestalten und zudem Kosten einsparen – so die Zielsetzung der Firma Christ für seinen vollautomatischen Casepacker CaseTeq. Lichtgitter und klassische Bildverarbeitungssysteme kamen daher nicht mehr in Frage. Stattdessen setzt der Spezialist für Verpackungsmaschinen auf das vollständig integrierte Vision-System von B&R.
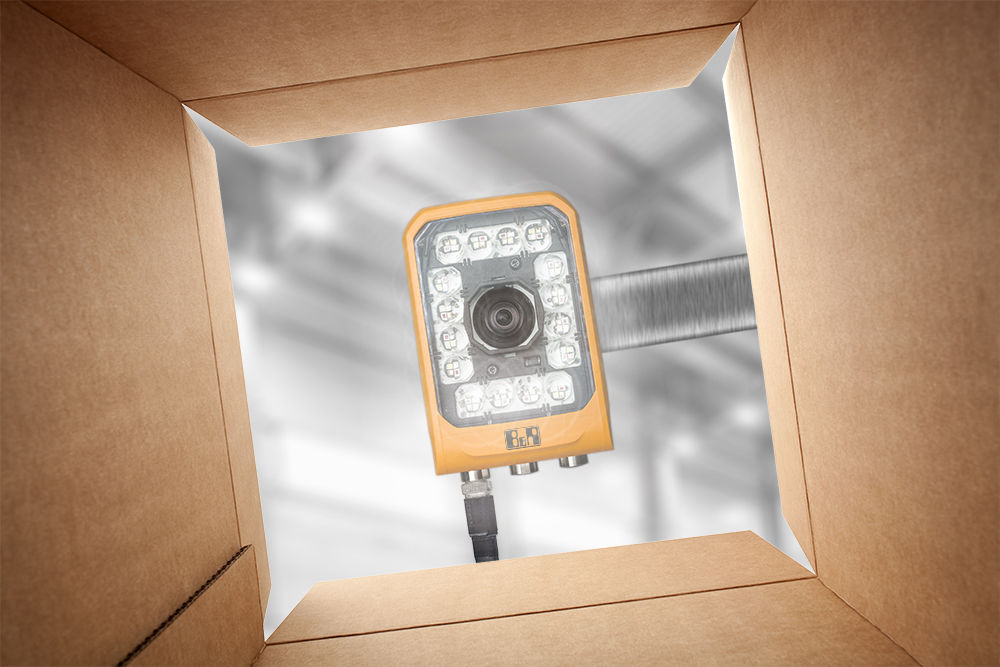
„Unsere Verpackungsmaschinen sind standardmäßig mit einer Produktanwesenheitskontrolle ausgestattet. Art und Umfang der erforderlichen Kontrolle unterscheiden sich allerdings je nach Kunde, verpacktem Produkt und Maschinentyp sehr“, sagt Timo Bochtler, Leiter der Elektrotechnikabteilung bei Christ Packing Systems. „Wir hatten daher in der Vergangenheit bei unseren Horizontal- und Vertikal-Casepacker (Top- und Side-Loader) zwei verschiedene Prüfsysteme im Einsatz: Lichtgitter und klassische Bildverarbeitungssysteme.“
Mit Lichtgittern lässt sich eine Bündelkontrolle bei einem Vertikal-Casepacker recht einfach und sehr kostengünstig umsetzen: Beim Abschieben einer Produktlage vom Stapelbereich in den Karton wird mit Hilfe der Lichtschranken des Lichtgitters überprüft, ob die Lage vollständig ist. Das Gitter ist so ausgerichtet, dass die Strahlen senkrecht auf die Lage fallen. Ist die Lage vollständig, bleiben die Lichtstrahlen während des Durchschiebens eine gewisse Zeitspanne, die sogenannte Verzögerungszeit, unterbrochen. Fehlt ein Produkt, können Strahlen die Lage durchdringen, die Zeitspanne wird unterschritten und eine Fehlermeldung ausgegeben.
Lichtgitter: Einfach aber unflexibel
Neben den geringen Komponentenkosten bietet die Kontrolle mit einem Lichtgitter einen weiteren Vorteil: Bei einer Formatumstellung lässt sich der Prüfschritt vom Anwender einfach über die Bedienerschnittstelle an die neuen Gegebenheiten anpassen. Er muss lediglich die Start- und Stoppposition des Staplerschubs, also die Breite des Stapels, sowie die benötigten Strahlen und die entsprechende Verzögerungszeit einstellen. Allerdings müssen erst einige Testfahrten vor dem eigentlichen Produktionsstart absolviert werden. Anhand dieser wird festgestellt, ob die ausgewählten Lichtstrahlen auch zu zuverlässigen Ergebnissen führen.
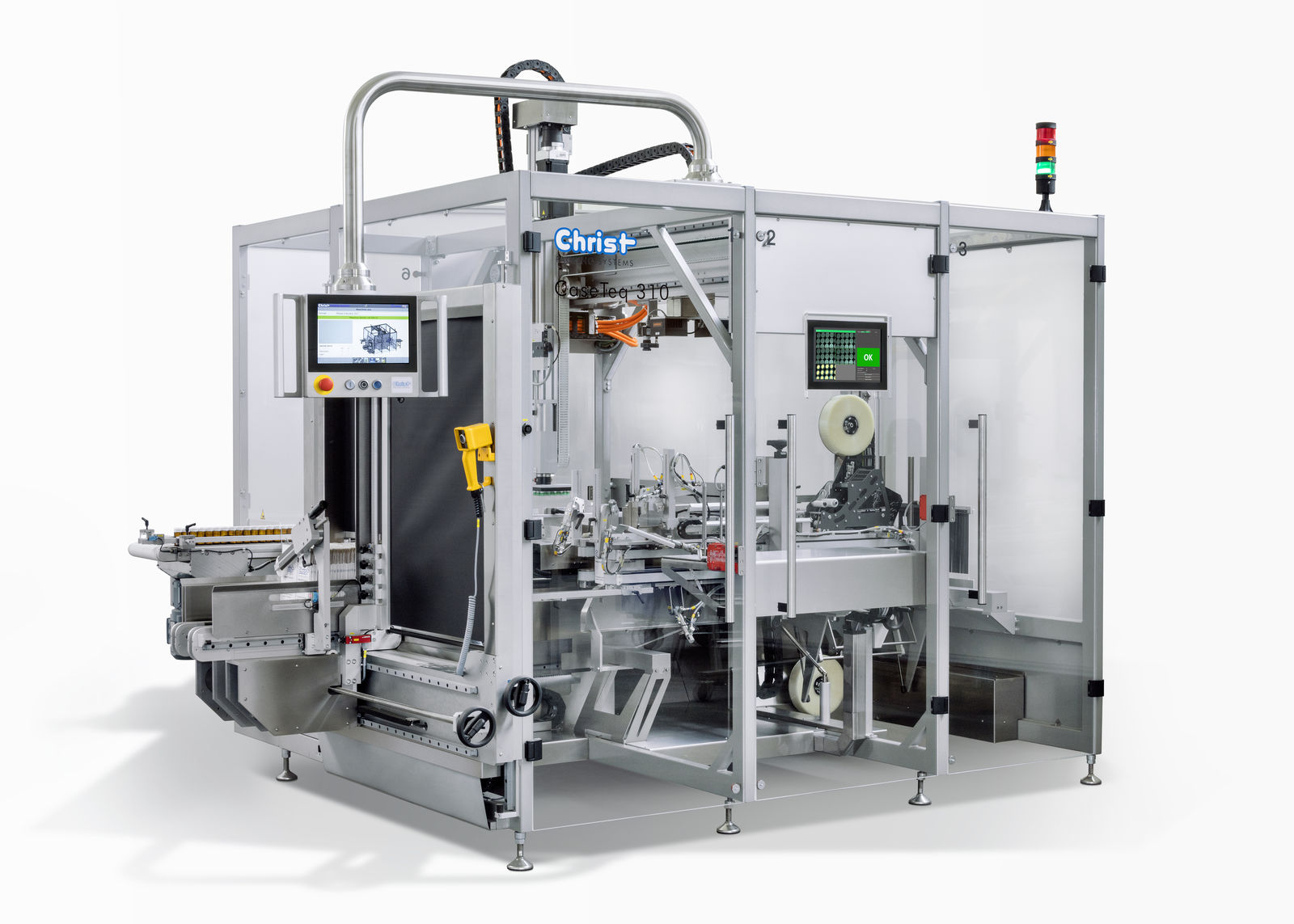
Enthält die Lage bauchige Produkte, bilden sich zwischen den Produkten Spalten, durch die Lichtstrahlen dringen können – eine Fehlermeldung entsteht. Um dies zu vermeiden, muss der Bediener die Lichtstrahlen an den betreffenden Stellen deaktivieren. „Zum Teil müssen sogar zwei Strahlen übereinander deaktiviert werden, um einen reibungslosen Produktionsablauf zu ermöglichen. Das geht aber zu Lasten der Qualität der Vollständigkeitsprüfung“, berichtet Bochtler aus der Praxis. „Darüber hinaus besteht die Gefahr, dass Bediener bei einem Formatwechsel übersehen, eigentlich erforderliche Strahlen wieder zu aktivieren.“ Zudem stößt das Lichtgitter schnell an seine Grenzen, wenn eine Lage aus vielen kleinen Produkten besteht oder sich die Kundenanforderungen ändern.
Klassische Kameralösung: Komplex, umständlich und teuer
Bei einem Horizontal-Casepacker lässt sich ein Lichtgitter prozessbedingt nicht einsetzen. Daher verwendete Christ für die Vollständigkeitsprüfung bei dieser Maschinenvariante bisher eine Kamera, die an der Pick-and-place-Achse montiert ist. Der Spezialist für Verpackungsmaschinen setzte dabei auf ein konventionelles Bildverarbeitungssystem. Konventionell bedeutet hier: Ein System, das aus einer Kamera, einer Optik, einem Bilderarbeitungssystem – meist einem PC – sowie einer speziellen Bildverarbeitungssoftware und gegebenenfalls einer Beleuchtung besteht.
Diese Lösung ist im Vergleich zum Lichtgittersystem wesentlich teurer und aufwendiger, aber auch deutlich flexibler, leistungsfähiger und prozesssicherer. Es können Bündelkontrollen und komplexere Prüfaufgaben wie Lage- oder Mustererkennung durchgeführt und Codes sowie Klartext gelesen werden.
Allerdings schlagen bei der Kameralösung hohe Anschaffungskosten für Hard- und Software zu Buche. So ist der zusätzliche Aufwand für den Programmierer der Maschine nicht zu vernachlässigen: Da es sich bei konventionellen Bildverarbeitungssystemen in der Regel um Stand-alone-Systeme handelt, müssen sich die Programmierer mit proprietärer Software und zusätzlichen Schnittstellen auseinandersetzen. Auch der Integration der Bildverarbeitungssoftware in die Maschinenanwendung sind enge Grenzen gesetzt. Darüber hinaus wird zum Bedienen der Bildverarbeitungssoftware spezielles Know-how benötigt. Für den Betreiber der Maschine bedeutet dies in der Regel, dass er auf Unterstützung durch Dritte angewiesen ist.
Nicht unerheblich für die Beteiligten ist auch, dass das System bei der Montage und bei jedem Hardwaretausch im Feld kalibriert werden muss. „Wir sind versierte Maschinenbauer, aber keine Kameraspezialisten. Für uns lässt sich daher auch kaum abschätzen, wann eine Beleuchtung erforderlich ist und wann nicht“, nennt Bochtler einen weiteren kritischen Aspekt konventioneller Kameralösungen.
Plant ein Maschinenbauer in so einer Situation die Beleuchtung aus Kostengründen nicht ein, läuft er Gefahr, kurzfristig nachrüsten zu müssen. Sieht er dagegen von Anfang an die Beleuchtung vor, obwohl sie am Ende nicht gebraucht wird, entstehen unnötige Zusatzkosten. Zusammenfassend lässt sich sagen, dass mit den bis dato verwendeten Kontrollsystemen schwer zu kalkulierende Risiken und Kosten verbunden sind.
Die Lösung: Das integrierte Vision-System von B&R
Als B&R sein integriertes Vision-System bei den Verantwortlichen von Christ vorstellte, war das Interesse sofort geweckt. Die Vorteile liegen auf der Hand: Durch die enge Integration des Vision-Systems in die Engineeringumgebung Automation Studio von B&R ist das Programmieren für den Maschinenbauer deutlich einfacher. Er kann alle Kamerafunktion nutzen und in die Maschinenanwendung einbauen, ohne die gewohnte Automatisierungswelt zu verlassen. Spezielles Know-how für die Bildverarbeitung ist nicht erforderlich. Die Einarbeitungsphase ist entsprechend kurz.
Je nach Anforderungsprofil können Anwender aus einem umfassenden Angebot wählen. Das schließt unterschiedliche Kameratypen mit integrierter Beleuchtung, diversen Auflösungen sowie Zubehör wie externe Leuchten ein. Der Clou dabei: Alle Komponenten sind Teil eines durchgängigen Systems. Sie hängen in einem Netz und werden von derselben Applikation gesteuert. Entsprechend lassen sich Blitz und Bildeinzug im Sub-Mikrosekundenbereich synchronisieren und damit die maximale Leistung der Beleuchtungs-LEDs ausnutzen.
Skalierbar und einfach in der Handhabung
Wird nur eine Bildverarbeitungsfunktion wie eine QR-Code- oder Lageerkennung benötigt, reicht die Kameravariante Smart Sensor von B&R aus. Anders als bei vielen Geräten dieser Klasse muss nicht für jede benötigte Funktion eine eigene Kamerahardware vorgehalten werden. Der Anwender konfiguriert die Funktion des Smart Sensors je nach Bedarf einfach mit Automation Studio selbst.
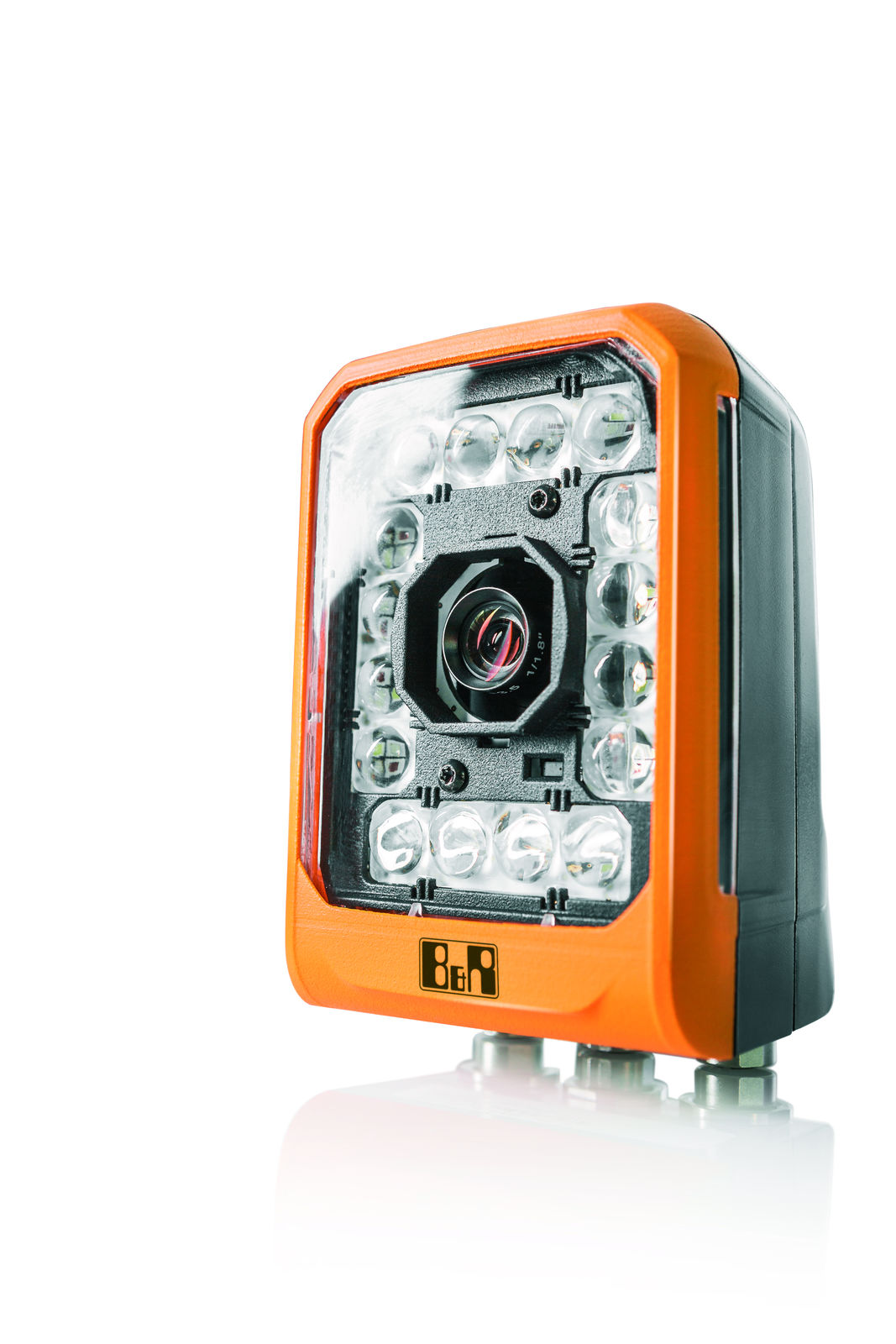
Sollen mehrere Funktionen gleichzeitig zum Einsatz kommen, ist ein Umstieg auf die leistungsfähigere Variante Smart Camera problemlos möglich. Die Applikationssoftware sowie alle bereits ermittelten Parameter und Modelle können weiterverwendet werden. Die Kamera ist inklusive Optik werkseitig bereits kalibriert, sodass dieser Schritt bei der Inbetriebnahme des Vision-Gerätes von B&R entfällt. Die Installation ist denkbar einfach, da die Kamera alle benötigten Einstellungen automatisch von der Steuerung erhält.
Produktwechsel auf Knopfdruck
Auch der Anwender profitiert klar von der engen Integration der B&R-Lösung. Da sich die Parameter inklusive Fokuseinstellung in Rezepten hinterlegen und auf Knopfdruck wiederherstellen lassen, ist auch ein Formatwechsel schnell erledigt. „Selbst wenn die Daten für ein Produkt oder Format noch nicht vorliegen, ist das kein Problem. Es muss nur ein Produkt angelernt und die Anordnung der Produkte in der Lage angegeben werden. Den Rest erledigt das System automatisch. Das ist ein Aspekt, der mir besonders gefällt“, sagt Bochtler.
Ein Produktwechsel gestaltet sich noch einfacher, wenn auch die Maschinensteuerung von B&R kommt, wie das bei Christ der Fall ist. Die Konfiguration und Rezeptverwaltung lässt sich dann direkt in die Visualisierung integrieren. Für die Diagnose können die vertrauten Werkzeuge von Automation Studio genutzt werden. Unterstützt wird der Programmierer dabei durch die B&R-Softwarekomponente mapp Vision mit der integrierten Machine-Vision-Bibliothek HALCON von MVTec. Diese stellt vorgefertigte und bewährte Algorithmen für die Positionsbestimmung, Vollständigkeitskontrolle, Qualitätsbewertung, Vermessung und Identifikation bereit. „Automatisierungsspezialisten wie wir können so das Thema Bildverarbeitung nach kurzer Einarbeitungsphase ohne externe Hilfe abdecken“, freut sich Bochtler.
Neue Prüflösungen
Aufgrund der Vorteile, die das B&R-Vision-System bietet, entschied sich Christ einen ersten vollautomatischen Horizontal-Casepacker vorzustellen, bei dem die Anwesenheitskontrolle mit der neuen Kameratechnik von B&R durchgeführt wird. Das Unternehmen will zeitnah weitere Prüfschritte mit dem Vision-System von B&R umsetzen und sukzessive alle anderen Endverpackungsmaschinen auf die neue Prüflösung umstellen.
„Das Vision-Paket von B&R deckt alles ab, was wir benötigen. Mit der skalierbaren Lösung können wir die bislang erforderlichen aber unterschiedlichen Kontrollsysteme durch ein einziges durchgängiges Vision-System ersetzen“, erläutert Bochtler. „Das ist für uns nicht nur wirtschaftlicher, sondern wir erhöhen auch noch die Flexibilität und Prozesssicherheit der Prüfung. Gleichzeitig reduzieren sich Unwägbarkeiten für uns und den Maschinenbetreiber.“
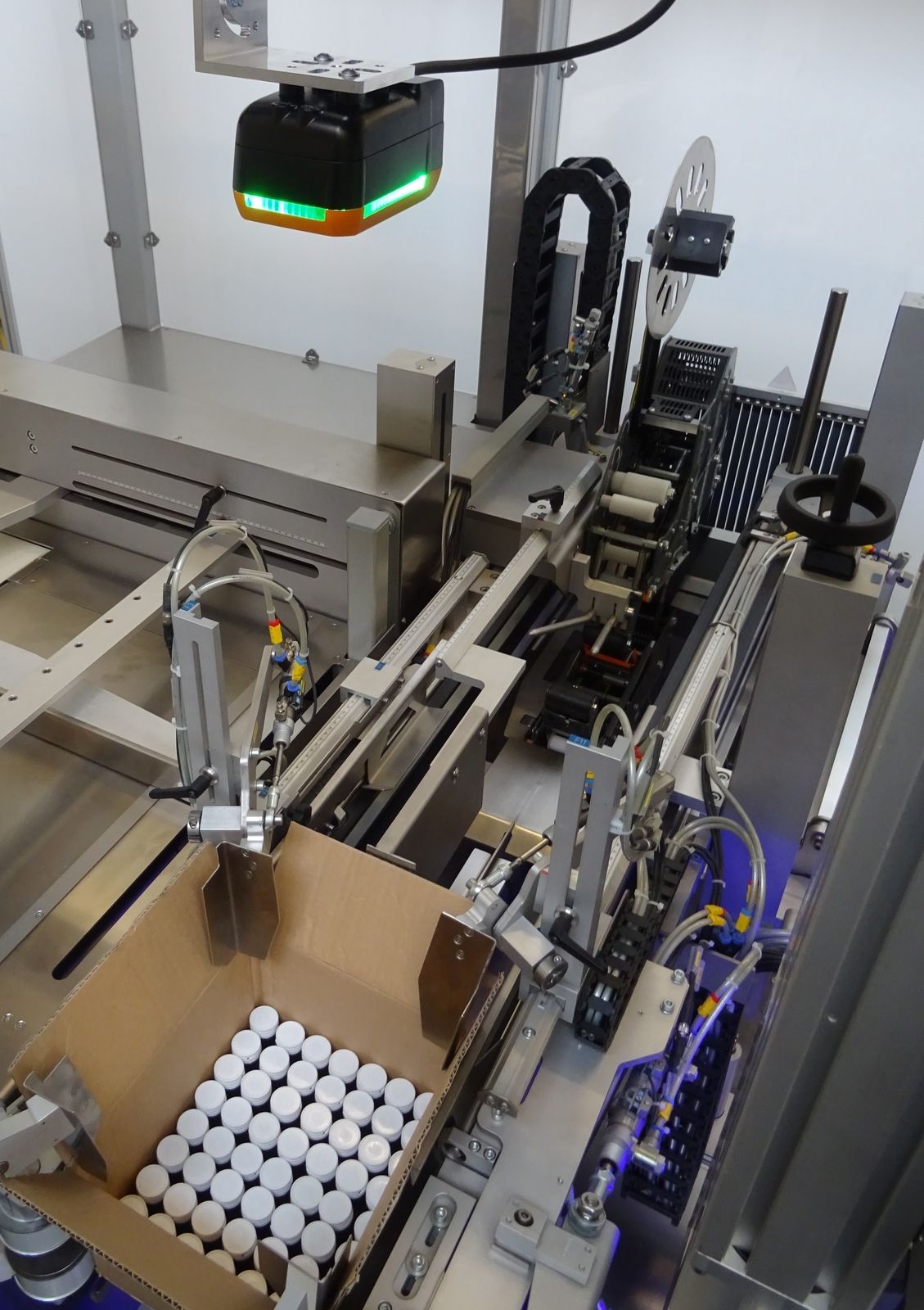
Autor: Dipl.-Ing. Franz Rossmann, Technikjournalist aus Gauting bei München
![]() | Timo Bochtler Leiter der Elektrotechnikabteilung bei Christ Packing Systems „Das Vision-Paket von B&R deckt alles ab, was wir benötigen. Mit der skalierbaren Lösung können wir die bislang erforderlichen unterschiedlichen Kontrollsysteme durch ein einziges durchgängiges Vision-System ersetzen. Das ist für uns nicht nur wirtschaftlicher, sondern wir erhöhen auch noch die Flexibilität und Prozesssicherheit der Prüfung. Gleichzeitig reduzieren sich Unwägbarkeiten für uns und den Maschinenbetreiber.“ |