Traditionally, once an OEM sells a machine, they are perfectly content to never hear from the buyer again – because that means the machine is running. How smoothly it is running is another question altogether. Beyond the occasional spare part or scheduled maintenance, contact with the customer – and any prospect of additional revenue – ends at delivery. That is all about to change, however.
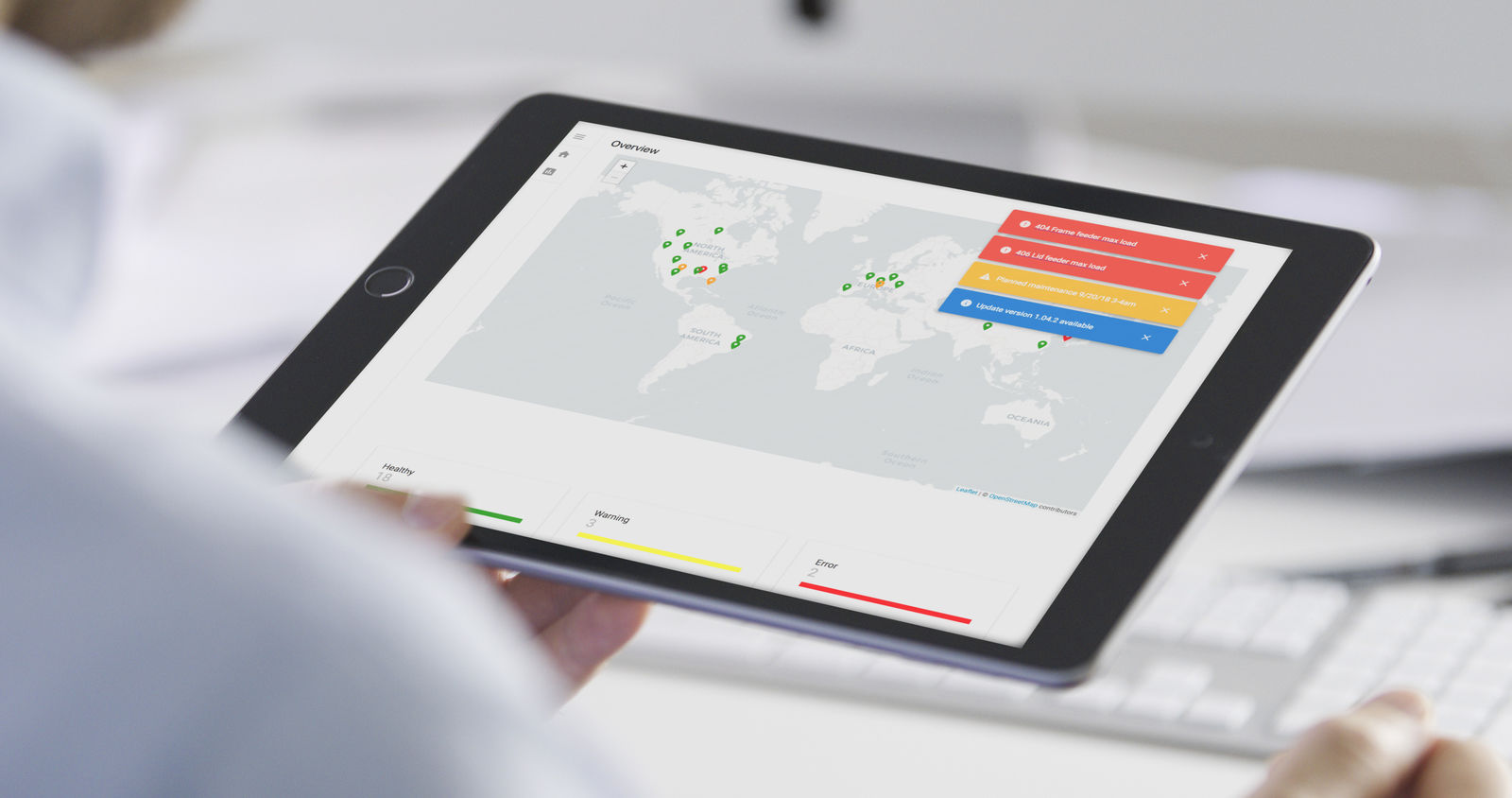
Through digitalization, the Industrial Internet of Things (IIoT) and cloud applications, it is now possible to monitor machines in the field and evaluate their performance. For machine builders, these newfound capabilities open up exciting new possibilities. If they can analyze the productivity, energy consumption and key performance indicators of the machines they have sold, what they want to know is whether they can use all this knowledge to offer new services and establish new business models. For IoT experts, the answer to this question is a resounding "yes". That is precisely what becomes possible when you have access to comprehensive data about the state of a machine.
Analyzing machine behavior
If they want to become more responsive to their customers' needs, machine builders need a connection to their machines in the field. "That's the only way they can analyze the machines' behavior and know how well they are running," explains B&R's IIoT expert, René Blaschke. Despite overwhelming arguments in favor of a cloud solution, machine manufactures still tend to be skeptical of the matter. One question they frequently ask is: "What does a cloud solution offer that I can't get through remote access? Blaschke has a simple answer: "Remote access only shows you what can be seen on the machine's HMI screen. What a cloud solution can do is much deeper and more significant: it can provide information about the condition and performance of the machine. The countless possibilities that this opens up are now available to B&R customers in the form of its first cloud application, Asset Performance Monitor.
Asset Performance Monitor collects machine data around the clock, prepares it and displays it in a clearly organized dashboard. It makes it easy for OEMs to keep track of their machines – anytime, and anywhere. "The cloud application provides them with a global view of their entire machine fleet," says Blaschke. For the first time, they have detailed evaluations of how their machines are faring in the field. "When machine builders are able to see the production rates, energy consumption and key performance indicators of their machines, they can select and compare the data for a given machine type across their entire installed base. This allows them to identify weaknesses and make targeted improvements to the machine," says Blaschke. The knowledge obtained from the data analyses can also be used to develop more efficient machines.
New business models
Well-targeted machine improvements are just one way to exploit the obtained data, however. Asset Performance Monitor also offers machine builders the ability to implement new business models. Blaschke names service level agreements and customized maintenance service as two examples. "Since they have access to data from their entire fleet, machine builders are able to offer their buyers custom-tailored service. For example, they can adapt the service interval based on how heavily the machine is actually being used."
Machine builders can also offer upgrades for entire machines or specific functions as a service to their customers. They can offer new and improved services in the area of energy and condition monitoring, including processing consumption data and displaying alarms. With B&R's mapp Technology, machine builders no longer need to develop and constantly maintain these functions in house. All they have to do is implement and configure the ready-made mapp software components.
A strong team behind the scenes
The cloud solution is based on the ABB Ability platform – the unified, cross-industry digital offering from B&R's parent company ABB. Microsoft Azure functions as the infrastructure for the ABB Ability platform. It ensures reliable access to all ABB Ability services around the world. The main benefit to OEMs of having these strong partners in the background is the peace of mind. As Blaschke says: "The system is fully scalable, so it doesn't matter whether the machine builder has five machines in the field or a thousand.
Local data regulations, such as the General Data Protection Regulation (GDPR) in Europe, can be integrated into the B&R solution because the ABB platform takes these legal requirements into account. "Only the latest encryption algorithms, protocols and technologies are used for data security," Blaschke affirms. The IoT engineers of the ABB Ability platform are responsible for ensuring that it is always state of the art.. "To achieve the same type of security in-house, machine builders would have to make considerable investments. With Asset Performance Monitor, they receive a ready-to-use solution that guarantees the security and integrity of their data," says Blaschke.
Open architecture
In order for the cloud application to collect machine data, the machine or production line must be connected to an edge gateway, such as an Automation PC. It receives data from the machine controller via OPC UA and passes it on to the cloud using the MQTT protocol. The edge gateway automatically establishes a connection to the ABB Ability cloud and installs the necessary software.
"With Asset Performance Monitor, we have created an out-of-the-box solution," emphasizes B&R's IoT expert. Simply logging in with a username and password gives the OEM access to Asset Performance Monitor and all the features it has to offer.
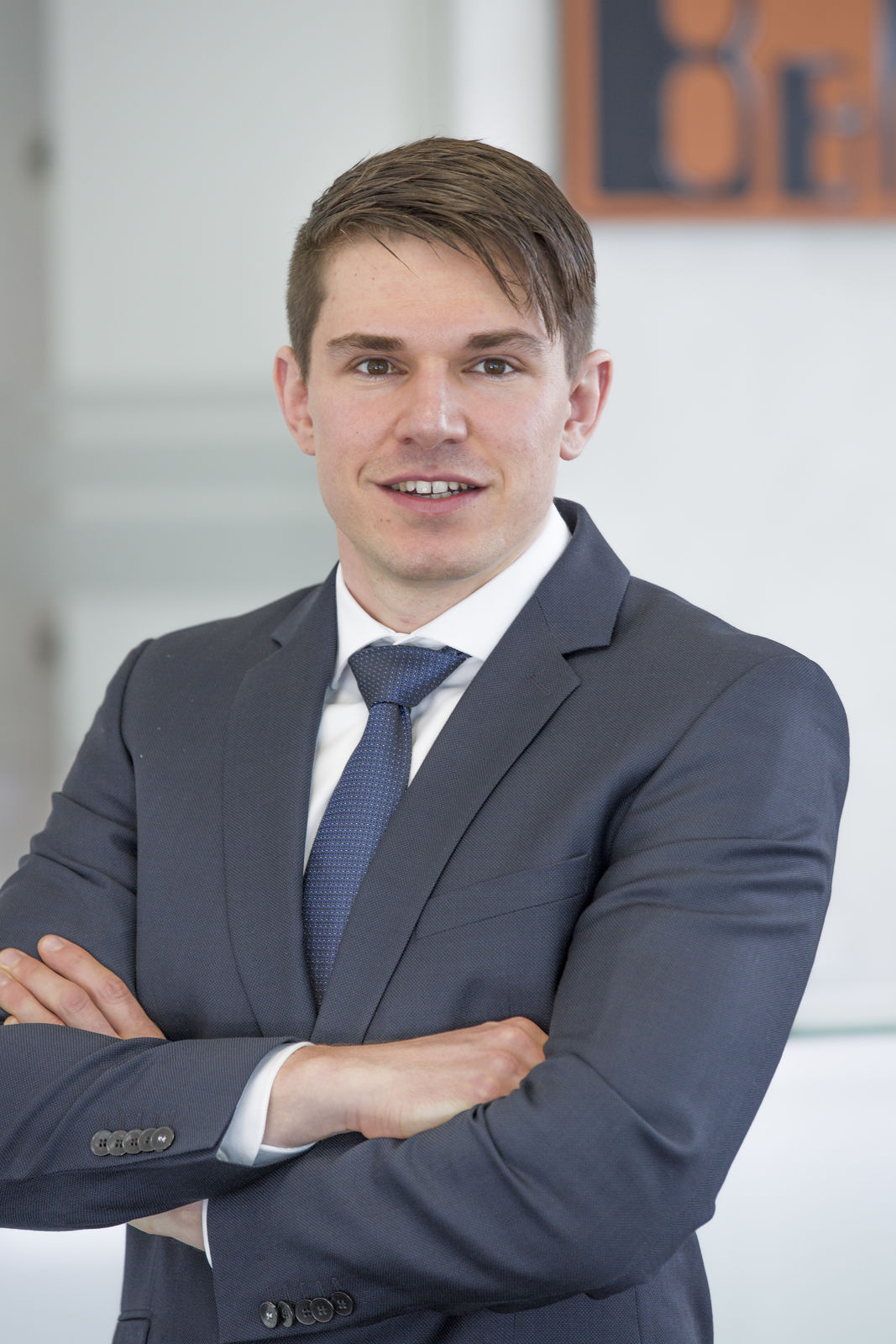
A win-win situation
Machine builders and operators both stand to benefit from a cloud solution that is fed with the corresponding data. "With a cloud solution, the machine builder is finally able to approach the end customer proactively after the machine has been sold," says Blaschke. Asset Performance Monitor is also multi-client capable. This makes it possible to limit the data that individual users are permitted to see. Machine builders can resell the system to their customers, allowing them to learn more about the machines they are using: The after-sale dialog can begin.
Author: Carmen Klingler-Deiseroth, freelance journalist